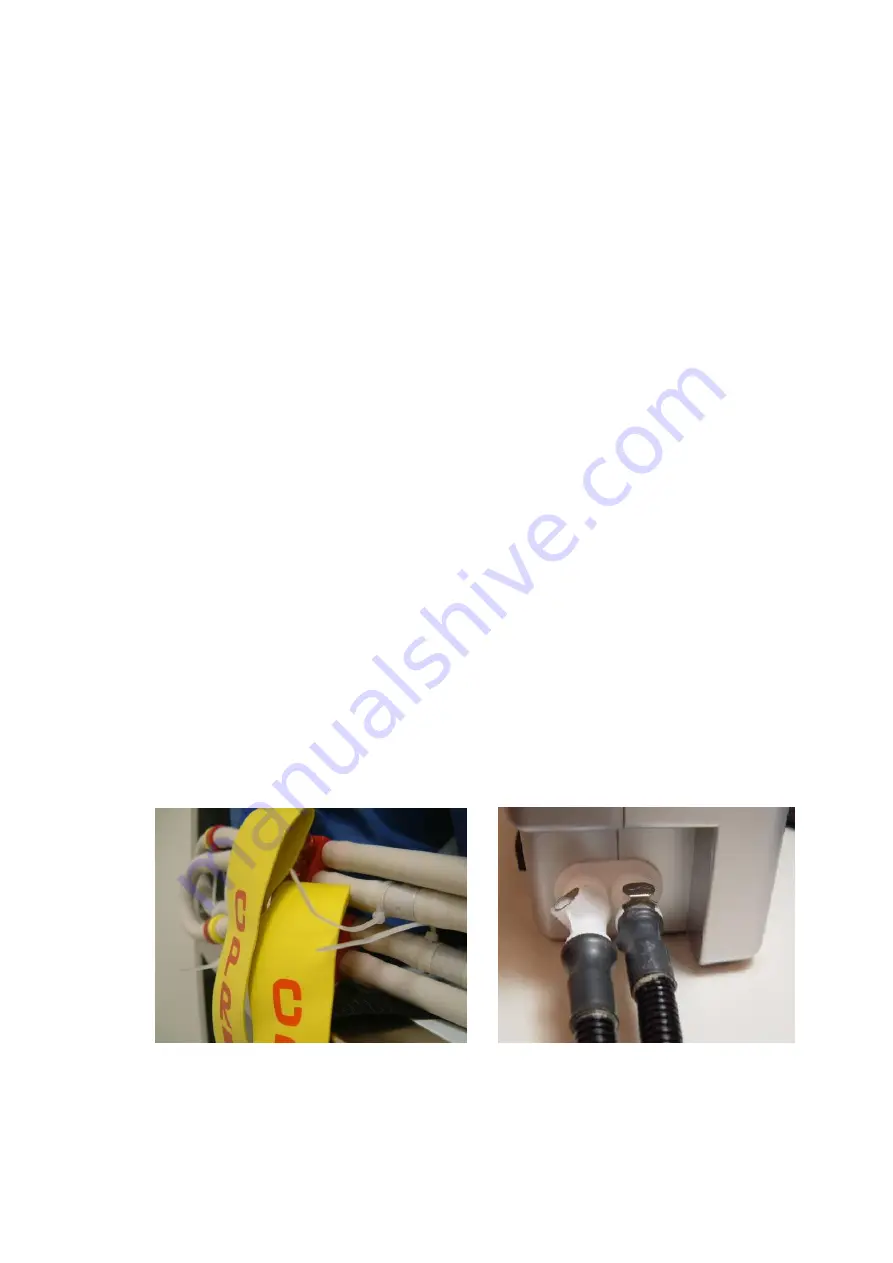
Service Manual - PHP 1000 Pump
2008.04 V1.0
6
2
Service Instruction:
Instruction for all general service repairs
WARNING
Disconnect power cord from the
mains plug, prior to any repair
Attention:
Before commencing the repair please follow instructions indicated
from below.
Such as CPR isn’t snapped securely, See Fig A
Quick connectors are not connected securely to the control
unit, See Fig B
For all the required replacement parts, please contact
your agent for part number. Once the BOM
(Bill of Material) is obtained, proceed to the parts order
and repair as follows.
Fig A
Fig B