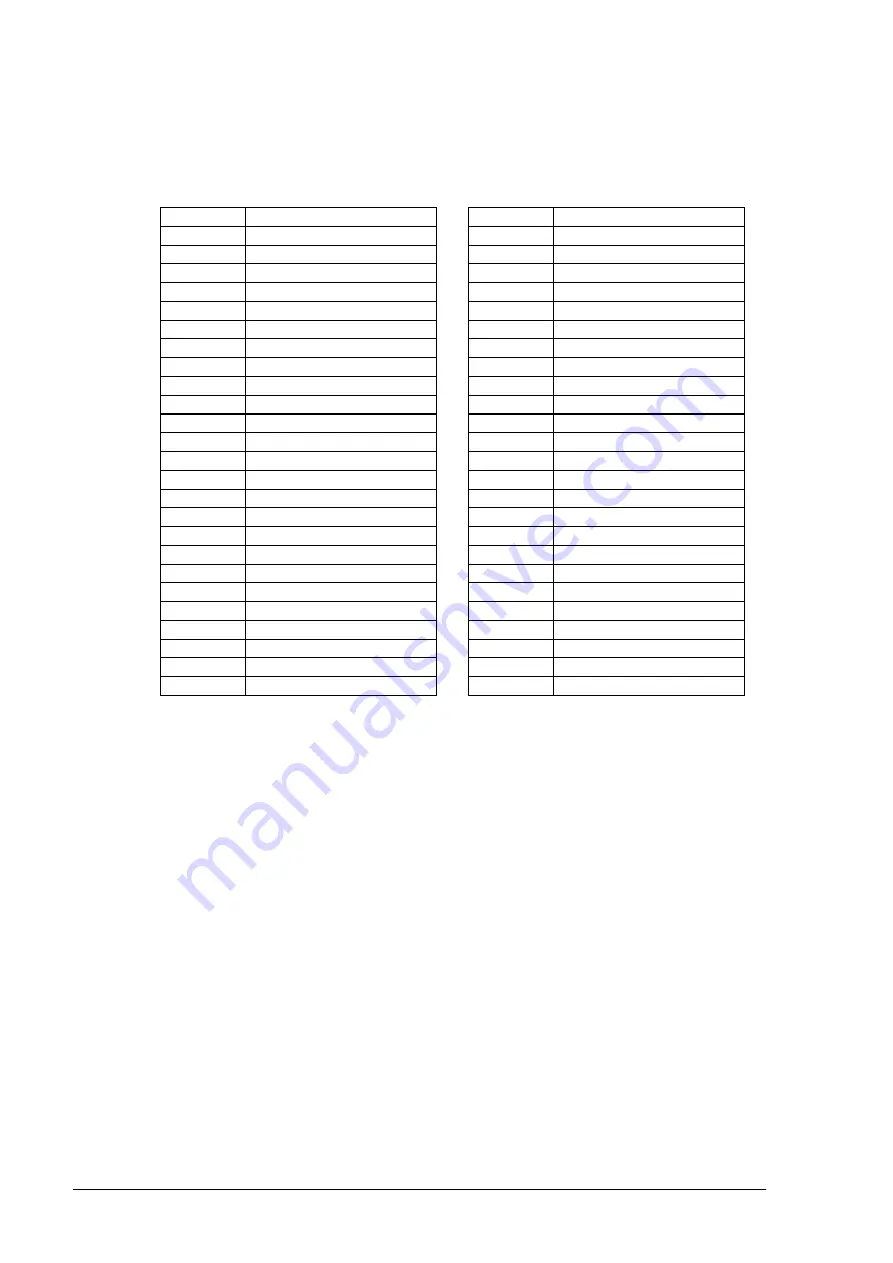
Page
40
Issue 2 22/4/98
MPC2000D
17. Fast Scan Analogue Data
The Fast Scan Analogue 1,2 and 3 can have the following data assigned to them to be read back to the PCX:-
Address
Data Represented.
Address
Data Represented.
0
Current in I1
27
Hardwire Command
1
Current in I2
32
Total run time
2
Current in I3
33
Total starts
3
Current in I0
34
Total trips
4
Voltage in VP1
35
Thermal capacity
5
Voltage in VP2
36
Trip fault number
6
Voltage in VP3
37
Logic status
7
Voltage in VL12
38
Pre trip I1
8
Voltage in VL23
39
Pre trip I2
9
Voltage in VL31
40
Pre trip I3
10
Drive Status
41
Pre trip I0
11
Trips
42
Pre trip VP1
12
Alarms
43
Pre trip VP2
13
Time to trip
44
Pre trip VP3
14
Time to start
45
Last start period
15
Average RMS current
46
Last start peak current
16
Motor load
47
Pre trip Power
17
Unbalance
48
Fault status
18
Alarm fault number
70
RTD4
19
Frequency
71
RTD5
20
Resistance(4)
86
Dip Switch
23
Phase Sequence
92
Average Power
24
Control Input 1
93
Power Factor
25
Control Input 2
94
Power VA
26
Control Input 3
18. Changes To The Manual.
From Issue 1.
Earth Fault Display lower range is noted. (Section 5.4.)
Accuracy of Power for small motors is noted. (Section 5.6.)
Fast Scan Update Time Added. (Section 9.1.)
This manual is applicable to relays with software version 17/4/98.
All information is subject to change without notice.