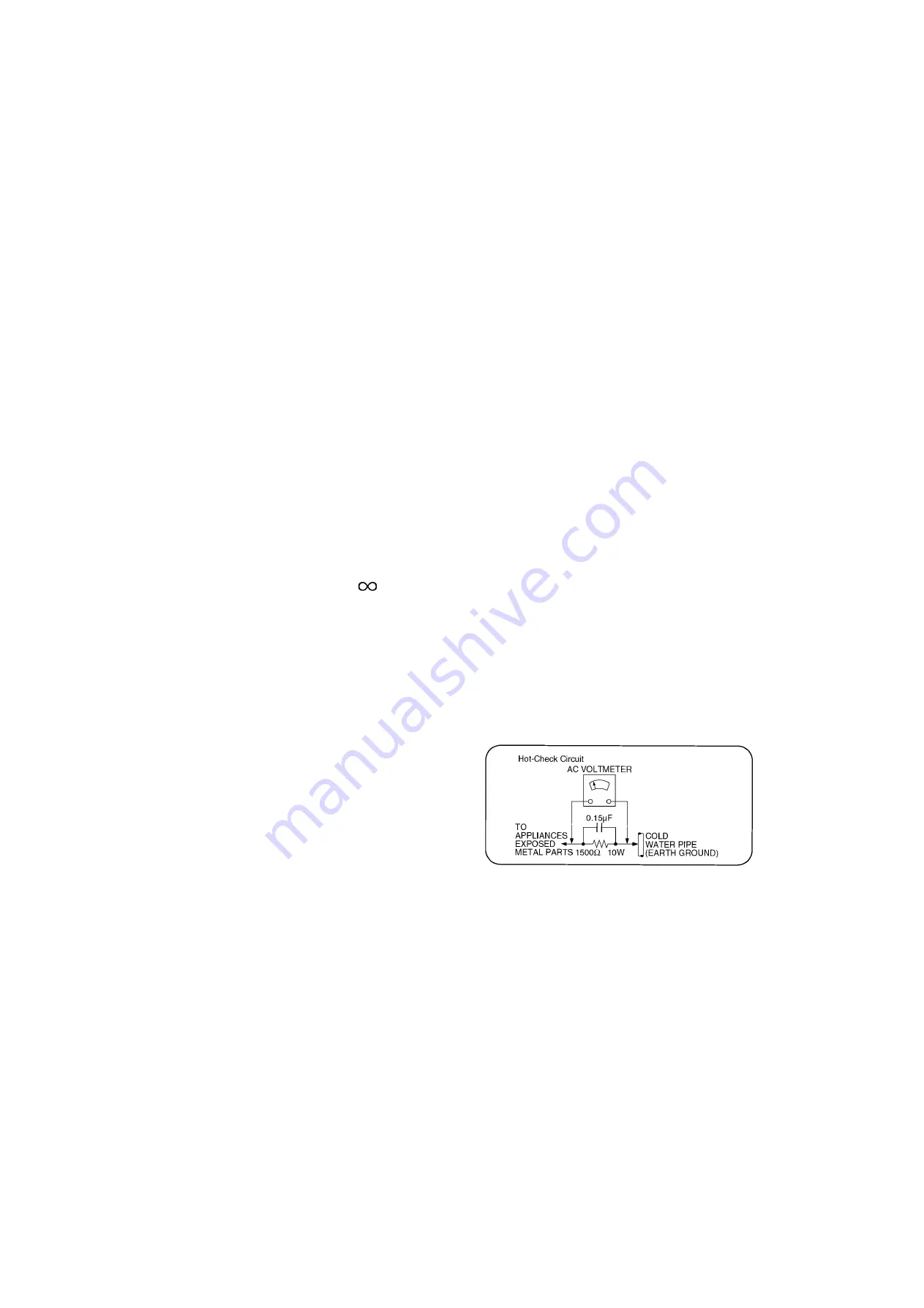
TH-L37D25R
3
1 Safety Precautions
1.1.
General Guidelines
1. When servicing, observe the original lead dress. If a short circuit is found, replace all parts which have been overheated or
damaged by the short circuit.
2. After servicing, see to it that all the protective devices such as insulation barriers, insulation papers shields are properly
installed.
3. After servicing, make the following leakage current checks to prevent the customer from being exposed to shock hazards.
4. When conducting repairs and servicing, do not attempt to modify the equipment, its parts or its materials.
5. When wiring units (with cables, flexible cables or lead wires) are supplied as repair parts and only one wire or some of the
wires have been broken or disconnected, do not attempt to repair or re-wire the units. Replace the entire wiring unit instead.
6. When conducting repairs and servicing, do not twist the Faston connectors but plug them straight in or unplug them straight
out.
1.1.1.
Leakage Current Cold Check
1. Unplug the AC cord and connect a jumper between the
two prongs on the plug.
2. Measure the resistance value, with an ohmmeter,
between the jumpered AC plug and each exposed
metallic cabinet part on the equipment such as
screwheads, connectors, control shafts, etc. When the
exposed metallic part has a return path to the chassis, the
reading should be 100 Mohm and over.
When the exposed metal does not have a return path to
the chassis, the reading must be
.
1.1.2.
Leakage Current Hot Check (See
Figure 1.)
1. Plug the AC cord directly into the AC outlet. Do not use
an isolation transformer for this check.
2. Connect a 1.5kohm, 10 watts resistor, in parallel with a
0.15
μ
F capacitors, between each exposed metallic part
on the set and a good earth ground such as a water pipe,
as shown in Figure 1.
3. Use an AC voltmeter, with 1000 ohms/volt or more
sensitivity, to measure the potential across the resistor.
4. Check each exposed metallic part, and measure the
voltage at each point.
5. Reverse the AC plug in the AC outlet and repeat each of
the above measurements.
6. The potential at any point should not exceed 0.75 volts
RMS. A leakage current tester (Simpson Model 229 or
equivalent) may be used to make the hot checks, leakage
current must not exceed 1/2 milliamp. In case a
measurement is outside of the limits specified, there is a
possibility of a shock hazard, and the equipment should
be repaired and rechecked before it is returned to the
customer.
Figure 1
Summary of Contents for TH-L37D25R
Page 16: ...TH L37D25R 16 7 2 AC Cord Dressing 2 ...
Page 18: ...TH L37D25R 18 7 4 AC Cord Bracket Installation Put on AC CORD BRACKET on cabinet and screw it ...
Page 19: ...TH L37D25R 19 7 5 Control Panel Assembly Put CONTROL PANEL ASSY on cabinet ...
Page 25: ...TH L37D25R 25 7 11 SP Unit Installation Put SP UNIT L and SP UNIT R on CABINET ...
Page 40: ...TH L37D25R 40 11 Schematic Diagram 11 1 Schematic Diagram Notes ...
Page 41: ...TH L37D25R 41 11 2 A Board 1 17 Schematic Diagram 6 5 4 3 2 1 A B C D E F G H I ...
Page 42: ...TH L37D25R 42 11 3 A Board 2 17 Schematic Diagram 6 5 4 3 2 1 A B C D E F G H I ...
Page 43: ...TH L37D25R 43 11 4 A Board 3 17 Schematic Diagram 6 5 4 3 2 1 A B C D E F G H I ...
Page 44: ...TH L37D25R 44 11 5 A Board 4 17 Schematic Diagram 6 5 4 3 2 1 A B C D E F G H I ...
Page 45: ...TH L37D25R 45 11 6 A Board 5 17 Schematic Diagram 6 5 4 3 2 1 A B C D E F G H I ...
Page 46: ...TH L37D25R 46 11 7 A Board 6 17 Schematic Diagram 6 5 4 3 2 1 A B C D E F G H I ...
Page 47: ...TH L37D25R 47 11 8 A Board 7 17 Schematic Diagram 6 5 4 3 2 1 A B C D E F G H I ...
Page 48: ...TH L37D25R 48 11 9 A Board 8 17 Schematic Diagram 6 5 4 3 2 1 A B C D E F G H I ...
Page 49: ...TH L37D25R 49 11 10 A Board 9 17 Schematic Diagram 6 5 4 3 2 1 A B C D E F G H I ...
Page 50: ...TH L37D25R 50 11 11 A Board 10 17 Schematic Diagram 6 5 4 3 2 1 A B C D E F G H I ...
Page 51: ...TH L37D25R 51 11 12 A Board 11 17 Schematic Diagram 6 5 4 3 2 1 A B C D E F G H I ...
Page 52: ...TH L37D25R 52 11 13 A Board 12 17 Schematic Diagram 6 5 4 3 2 1 A B C D E F G H I ...
Page 53: ...TH L37D25R 53 11 14 A Board 13 17 Schematic Diagram 6 5 4 3 2 1 A B C D E F G H I ...
Page 54: ...TH L37D25R 54 11 15 A Board 14 17 Schematic Diagram 6 5 4 3 2 1 A B C D E F G H I ...
Page 55: ...TH L37D25R 55 11 16 A Board 15 17 Schematic Diagram 6 5 4 3 2 1 A B C D E F G H I ...
Page 56: ...TH L37D25R 56 11 17 A Board 16 17 Schematic Diagram 6 5 4 3 2 1 A B C D E F G H I ...
Page 57: ...TH L37D25R 57 11 18 A Board 17 17 Schematic Diagram 6 5 4 3 2 1 A B C D E F G H I ...
Page 58: ...TH L37D25R 58 11 19 V Board Schematic Diagram 6 5 4 3 2 1 A B C D E F G H I ...
Page 59: ...TH L37D25R 59 11 20 TC Board 1 6 Schematic Diagram 6 5 4 3 2 1 A B C D E F G H I ...
Page 60: ...TH L37D25R 60 11 21 TC Board 2 6 Schematic Diagram 6 5 4 3 2 1 A B C D E F G H I ...
Page 61: ...TH L37D25R 61 11 22 TC Board 3 6 Schematic Diagram 6 5 4 3 2 1 A B C D E F G H I ...
Page 62: ...TH L37D25R 62 11 23 TC Board 4 6 Schematic Diagram 6 5 4 3 2 1 A B C D E F G H I ...
Page 63: ...TH L37D25R 63 11 24 TC Board 5 6 Schematic Diagram 6 5 4 3 2 1 A B C D E F G H I ...
Page 64: ...TH L37D25R 64 11 25 TC Board 6 6 Schematic Diagram 6 5 4 3 2 1 A B C D E F G H I ...
Page 82: ...Model No TH L37D25R Parts Location ...
Page 83: ...Model No TH L37D25R Packing Exploded View 1 ...