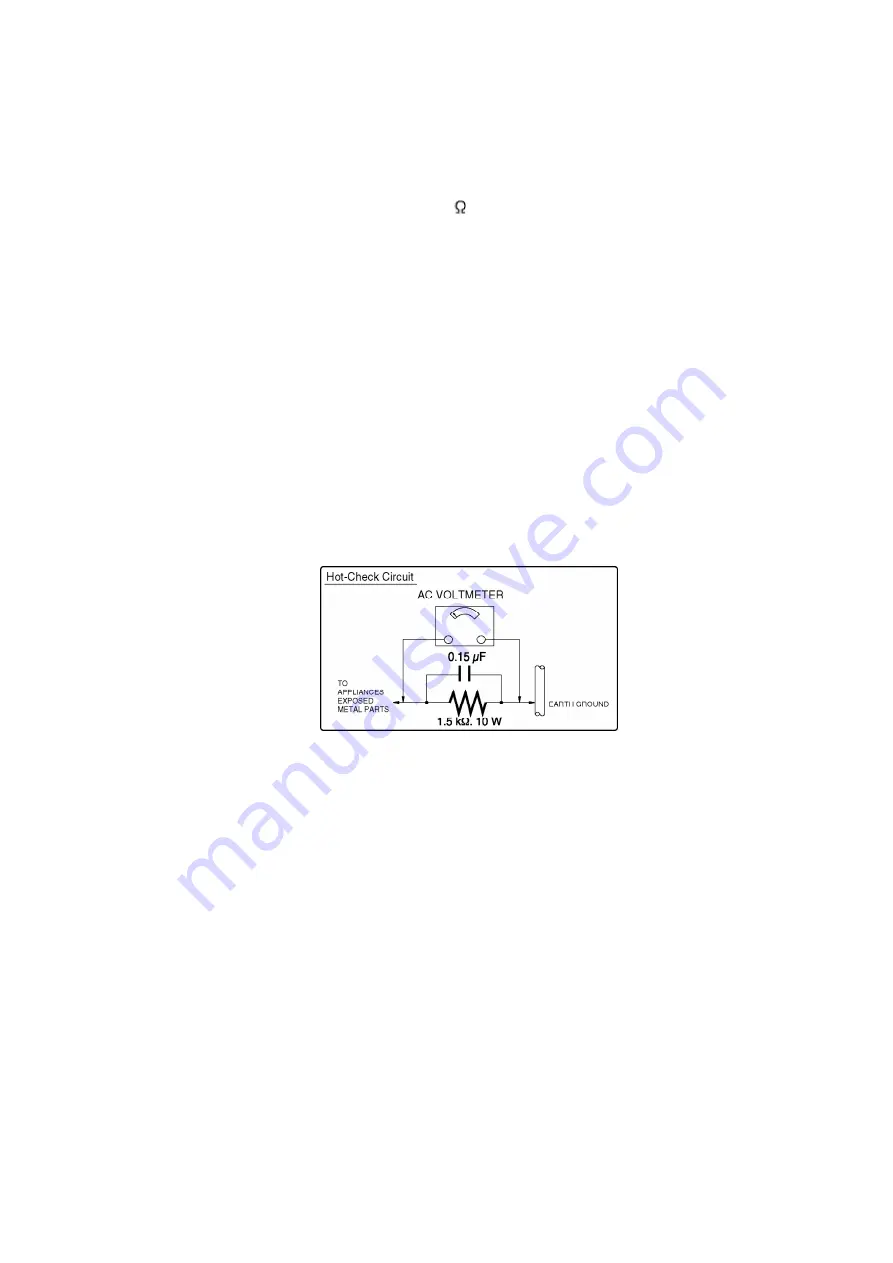
capacitor, between each exposed metallic part on the set and a
good earth ground, as shown in Figure 1.
3. Use an AC voltmeter, with 1 k /V or more sensitivity, to measure
the potential across the resistor.
4. Check each exposed metallic part, and measure the voltage at
each point.
5. Reverse the AC plug in the AC outlet and repeat each of the above
measurements.
6. The potential at any point should not exceed 0.75 V RMS. A
leakage current tester (Simpson Model 229 or equivalent) may be
used to make the hot checks, leakage current must not exceed 1/2
mA. In case a measurement is outside of the limits specified,
there is a possibility of a shock hazard, and the equipment should
be repaired and rechecked before it is returned to the customer.
Figure. 1
2. PREVENTION OF ELECTRO STATIC DISCHARGE
(ESD) TO ELECTROSTATICALLY SENSITIVE (ES)
DEVICES
Some semiconductor (solid state) devices can be damaged easily by static electricity. Such
components commonly are called Electrostatically Sensitive (ES) Devices. Examples of typical
ES devices are integrated circuits and some field-effect transistors and semiconductor "chip"
components. The following techniques should be used to help reduce the incidence of
component damage caused by electro static discharge (ESD).
1. Immediately before handling any semiconductor component or
semiconductor-equipped assembly, drain off any ESD on your
body by touching a known earth ground. Alternatively, obtain and
wear a commercially available discharging ESD wrist strap, which
should be removed for potential shock reasons prior to applying
power to the unit under test.
4
Summary of Contents for NV-DS29EG
Page 15: ...15...
Page 16: ...16...
Page 23: ...7 2 1 Inner Parts Location 7 2 1 1 TOP VIEW Fig DM1 1 23...
Page 24: ...7 2 1 2 BOTTOM VIEW Fig DM1 2 24...
Page 26: ...7 2 3 Mechanism Base Unit Fig DM3 26...
Page 27: ...7 2 4 Guide Piece L Guide Piece R Garage Unit Fig DM4 27...
Page 28: ...7 2 5 Cylinder Unit Fig DM5 28...
Page 29: ...7 2 6 Dumper Unit Fig DM6 29...
Page 30: ...7 2 7 DEW Sensor DEW Cable Fig DM7 30...
Page 31: ...7 2 8 Mechanism F P C Unit Fig DM8 31...
Page 32: ...7 2 9 Reduction Gear B Fig DM9 32...
Page 33: ...7 2 10 Mechanism Cover Unit Fig DM10 33...
Page 34: ...7 2 11 Idler Arm Unit Center Gear Fig DM11 34...
Page 35: ...7 2 12 Tension Arm Unit Fig DM12 35...
Page 36: ...7 2 13 S Reel Table T Reel Table Fig DM13 36...
Page 37: ...7 2 14 T Break Unit Fig DM15 37...
Page 38: ...7 2 15 Pinch Arm Unit Fig DM16 38...
Page 39: ...7 2 16 Rail Fig DM17 39...
Page 40: ...7 2 17 Cylinder Base Unit Fig DM18 40...
Page 41: ...7 2 18 S T Arm Unit S T Post Unit Fig DM19 41...
Page 42: ...7 2 19 Loading Motor Unit Fig DM20 42...
Page 43: ...7 2 20 Sensor F P C Fig DM21 43...
Page 44: ...7 2 21 Tension Drive Arm S Brake Drive Lever Fig DM22 44...
Page 45: ...7 2 22 Cam Gear Fig DM23 45...
Page 46: ...7 2 23 Pinch Drive Arm Intermediate Gear Fig DM24 46...
Page 47: ...7 2 24 Mode Switch Fig DM25 47...
Page 48: ...7 2 25 MIC Switch Fig DM26 48...
Page 49: ...7 2 26 Main Plate Unit Fig DM27 49...
Page 50: ...7 2 27 T4 Drive Arm Fig DM28 50...
Page 51: ...7 2 28 Drive Pulley Fig DM29 51...
Page 52: ...7 2 29 Capstan Unit Timing Belt Capstan Adjust Spring Fig DM30 52...
Page 53: ...7 2 30 Lock Lever Unit Lock Pick Lever Fig DM31 53...
Page 54: ...8 ADJUSTMENT PROCEDURES 8 1 SERVICE FIXTURES TOOLS 54...
Page 55: ...55...
Page 56: ...8 2 MECHANICAL ADJUSTMENT 8 2 1 Comparison between adjustment items and replacement parts 56...
Page 68: ...12 2 FRONT CASE SECTION 68...
Page 69: ...12 3 CCD AND LENS SECTION 69...
Page 70: ...12 4 TOP CASE AND EVF SECTION 70...
Page 71: ...12 5 SIDE CASE R AND LCD SECTION 71...
Page 72: ...12 6 MECHANISM SECTION 72...
Page 73: ...12 7 PACKING PARTS AND ACCESSORIES SECTION 73...
Page 131: ......
Page 132: ......
Page 133: ......