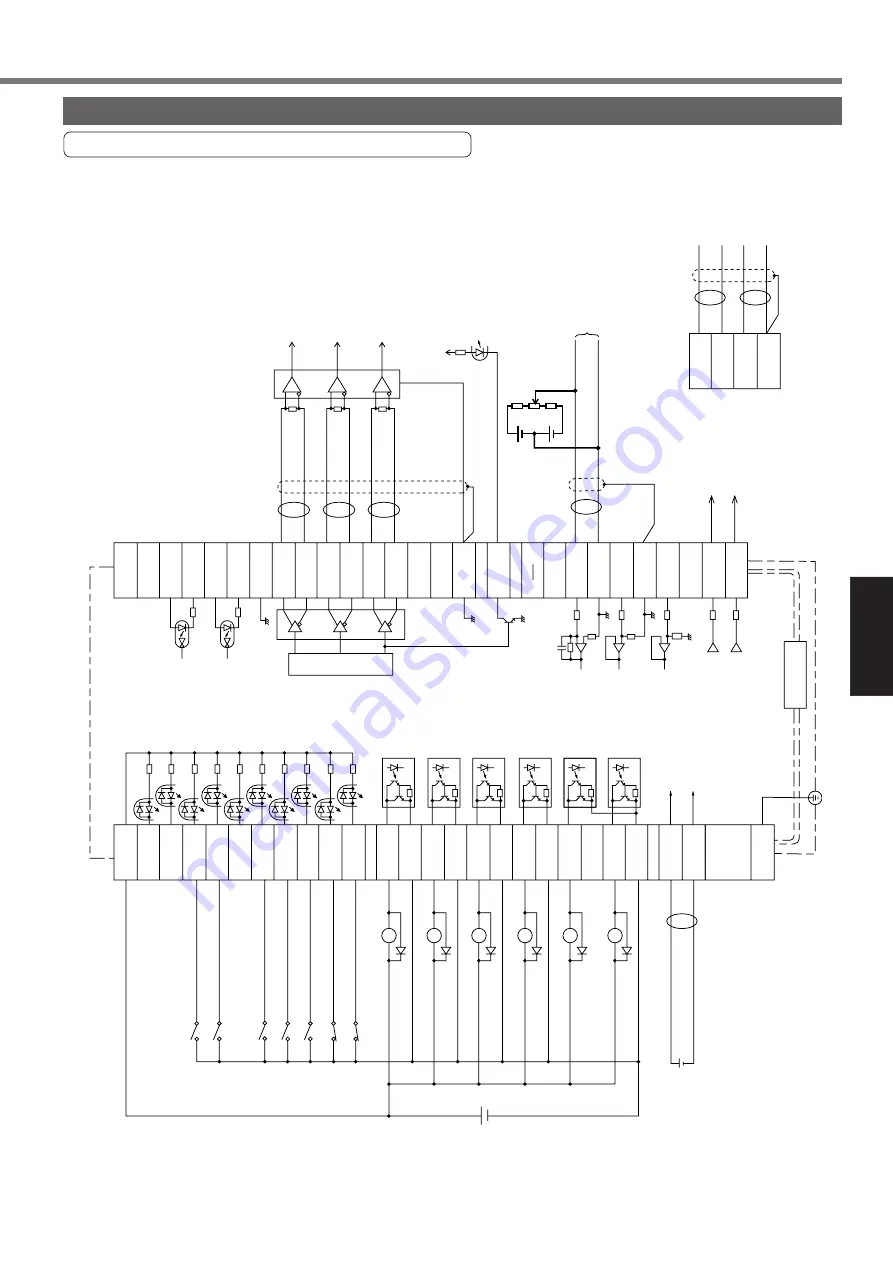
133
[Connections and Settings in Torque Control Mode]
Connections and Settings in
Torque Control Mode
Battery for absolute encoder
7
4.7k
Ω
COM+
PULS2
SIGN1
SIGN2
GND
OA+
OA
-
OB+
OB
-
OZ+
OZ
-
GND
CZ
SPR/TRQR
GND
CCWTL/TRQR
GND
CWTL
SP
IM
1
2
3
4
5
6
13
21
22
48
24
46
47
25
19
20
14
15
16
17
43
18
42
49
23
10k
Ω
10k
Ω
20k
Ω
220
Ω
220
Ω
10k
Ω
10k
Ω
1k
Ω
1k
Ω
PULS1
INH
CL
SR
V
-ON
GAIN
DIV
ZEROSPD
C-MODE
A-CLR
CCWL
CWL
S-RDY+
S-RDY
-
ALM+
COIN+
BRKOFF
+
BRKOFF
-
TLC
V
DC
12
-
24V
ZSP
COM
-
BA
TT+
to CN X4 (5th pin)
to CN X4 (6th pin)
BA
TT
-
CN X5
FG
COIN
-
ALM
-
33
30
29
27
28
26
32
31
9
8
35
34
37
36
39
38
11
10
40
12
41
44
45
50
Servo-ON
P-operation/2nd gain
switching
Control mode switching
Scaler
Alarm clear
CCW overtravel inhibit
A-phase
output
B-phase
output
Z
Z-phase
output
Speed monitor
T
orque monitor
Z-phase output (Open collector)
CW overtravel inhibit
Servo ready
Servo alarm
At-speed
Mechanical brake release
· In case the battery for absolute encoder
is installed at the controller side
T
orque limited
(Pr09)
Zero speed detected
(Pr0A)
<Note> Specify the speed limit value using
4th speed set-up (Pr56) parameter
.
SPR/TRQR
GND
CCWTL/TRQR
GND
14
15
16
17
330
Ω
330
Ω
330
Ω
Zero speed clamp (Pr06)
T
orque command
(0 to
±
10V)
Wiring when Pr02
(Control Mode) = 5
Speed
command
(0 to
±
10V)
T
orque
command
(0 to
±
10V)
CN X5 Connector
Circuits Available for Torque control mode
CN X5 Connector