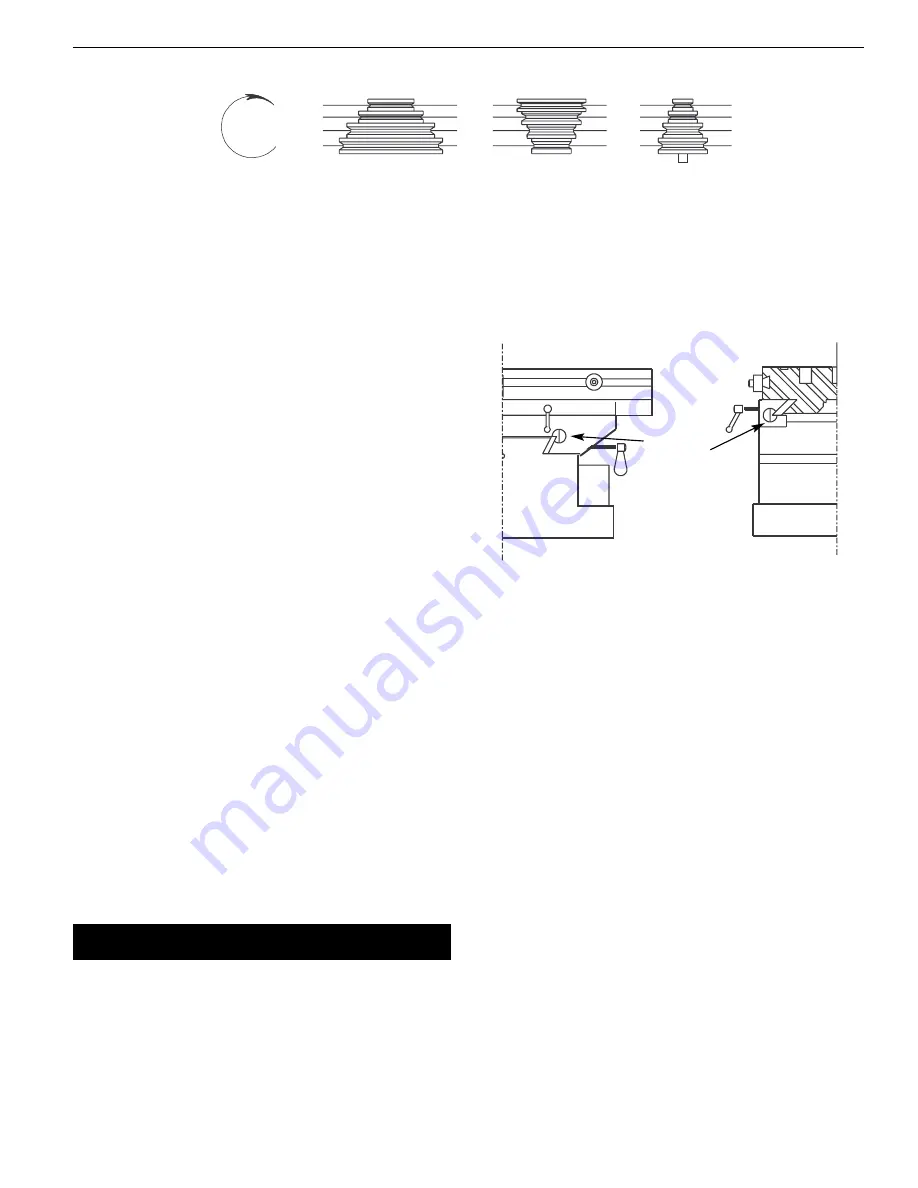
5
Palmgren Operating Manual & Parts List
80161 & 70104
OPERATION (CONTINUED)
DEPTH STOP
Refer to Figures 6 and 7.
Repeated operations where depth of cut is consistent are made
easier by using depth scale (Figure 6, Ref. No. 47) and depth setting
knob (Figure 7, Ref. No. 9).
Depth of cut is shown on depth scale and indicated by depth indi-
cator (Figure 6, Ref. No. 48).
Depth of cut is set by rotating depth setting knob until desired
depth is obtained.
HANDWHEEL SCALES
Refer to Figure 8.
The cross feed handwheel and right-hand longitudinal handwheel
are equipped with graduated collars.
One full rotation of handwheel moves table .100”. Handwheel
scales are graduated in .001”.
Scales are used when precise movement of table is required.
Scales can be zeroed by loosening dial screw (Ref. No. 16) and
rotating lead screw dial (Ref. No. 13) until zero marks are aligned.
Tighten dial screw.
TABLE STOP BLOCKS
Refer to Figure 8.
Longitudinal travel can be limited to make repeated operations
easier by using the table stop blocks (Ref. No. 40).
Table stop blocks are positioned to contact table stop bracket (Ref.
No. 26) limiting table travel.
Adjust stop blocks by loosening socket head bolts (Ref. No. 39) and
moving stop blocks to desired position. Secure socket head bolts.
TABLE LOCKS
Refer to Figure 8.
Mill drill table can be locked into position using table lock handles
(Ref. No. 27).
Longitudinal position is secured by tightening lock handles on
front of saddle.
Cross feed position is secured by tightening lock handles on right
side of saddle.
REMOVE ARBOR
Loosen draw bar with wrench and remove arbor from spindle.
M
MA
AIIN
NT
TE
EN
NA
AN
NC
CE
E
Refer to Figures 5, 6, 7 and 8.
Keep all moving parts and surfaces clean of dirt, metal chips, etc.
Keep a light coating of oil on all exposed surfaces, including table
top and slots, all dovetail way surfaces, lead screws, rack and col-
umn.
Replace worn V-belts.
Check electrical connections and replace any worn or frayed wires
or line cords.
Replace worn way cover.
GIB ADJUSTMENT
Refer to Figures 5 and 8.
Palmgren mill drill is equipped with adjustable gibs (See Figure 5)
on longitudinal and cross feed that eliminate excess play in table
as dovetail ways wear over time.
Rotating gib adjustment bolts (Ref. No. 25) clockwise tightens
dovetail ways. Adjust gib bolts until a slight drag is felt when mov-
ing the table with handwheels. Loosen bolts if table is too tight.
REPLACE RETURN SPRING
Refer to Figure 6 and 7.
Return spring may wear after extended use and will need replace-
ment. If spindle does not return to full up position when released,
then replace return spring.
CAUTION:
Spring is under tension and may tend to twist forceful-
ly when relaxed.
To replace return spring, push spindle to fully up position and lock
it in place by tightening quill lock handle (Figure 7, Ref. No. 23).
Loosen spring cover knob (Figure 6, Ref. No. 38) slowly and careful-
ly rotate spring and cover clockwise to relax spring tension.
Remove spring cover knob and washer (Figure 6, Ref. No. 38 and
40). When tension is released, rotate spring and cover clockwise to
release spring from mounting screw.
Remove spring and cover. Place new spring over pinion shaft and
slide slot at end of spring over mounting screw. Press spring and
cover against head casting.
Replace washer and spring cover knob. Rotate cover counterclock-
wise to tension spring. Rotate cover approximately three full turns
and tighten cover knob. Release quill lock handle.
Test spring tension by pulling down on crank handle (Figure 6, Ref.
No. 19). Adjust spring tension as needed.
Overtightening spring causes quill to return with excessive
force damaging quill and rubber bumper (Figure 7, Ref. Nos. 5
and 19).
Figure 4 – Spindle Speed Chart
B
C
A
1
2
3
4
Motor
Spindle
Spindle
Rotation
D
X
Y
W
Z
Figure 5 – Gib Adjustment
Gib
Adjustment
Bolts