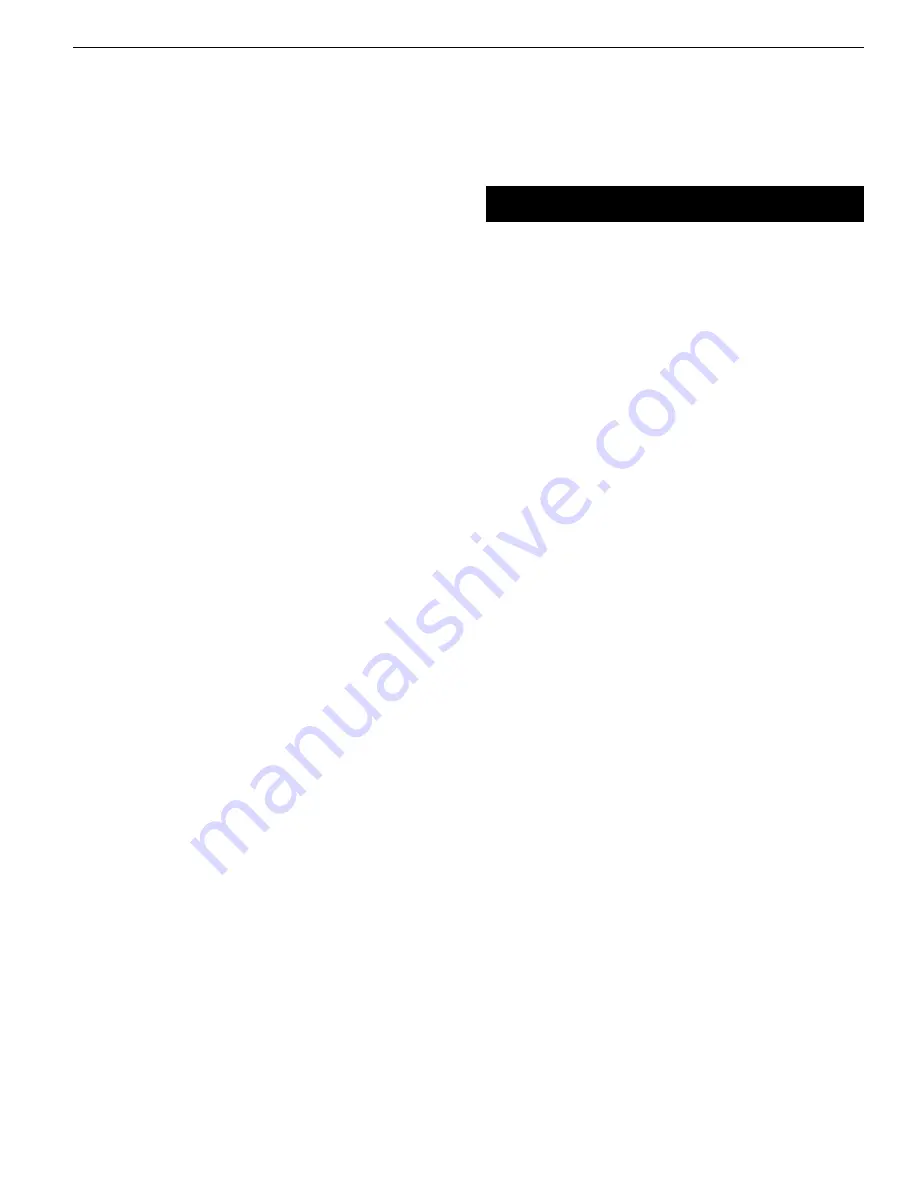
3
WORK AREA SHOULD BE READY FOR JOB
•
Keep work area clean. Cluttered work areas and work benches
invite accidents.
•
Do not use power tools in dangerous environments. Do not use
power tools in damp or wet locations. Do not expose power
tools to rain.
•
Work area should be properly lighted.
•
Proper electrical outlet should be available for tool.
Three-prong plug should be plugged directly into properly
grounded, three-prong receptacle.
•
Extension cords should have a grounding prong, and the three
wires of the extension cord should be of the correct gauge.
•
Keep visitors at a safe distance from work area.
•
Keep children out of workplace. Make workshop childproof. Use
padlocks, master switches or remove switch keys to prevent
any unintentional use of power tools.
TOOL SHOULD BE MAINTAINED
•
Always unplug tool prior to inspection.
•
Read operating instructions manual for specific maintaining
and adjusting procedures.
•
Keep tool lubricated.
•
Use sharp cutters and keep the tool clean for safest operation.
•
Remove adjusting tools. Form the habit of checking that adjust-
ing tools are removed before turning on the machine.
•
Keep all parts in working order. Check to determine that the
guard or other parts will operate properly and perform their
intended function.
•
Check for damaged parts. Check for alignment of moving parts,
binding, breakage, mounting and any other condition that may
affect a tool’s operation.
•
Damaged parts should be properly repaired or replaced. Do not
perform makeshift repairs. (Use the parts list provided to order
replacement parts.)
KNOW HOW TO USE TOOL
•
Use the right tool for the job. Do not force tool or attachment
to do a job for which it was not designed.
•
Disconnect tool when changing accessories such as bits, cut-
ters and the like.
•
Avoid accidental start-up. Make sure switch is in OFF position
before plugging in.
•
Do not force tool. It will work most efficiently at the rate for
which it was designed.
•
Handle workpiece correctly. Secure work with clamps or vise.
Leave hands free to operate machine, Protect hands from
possible injury.
•
Never leave a tool running unattended. Turn the power off and
do not leave tool until it comes to a complete stop.
•
Do not overreach. Keep proper footing and balance.
•
Never stand on tool. Serious injury could occur if tool is tipped
or if cutter is unintentionally contacted.
•
Keep hands away from moving parts and cutting surfaces.
•
Know your tool. Learn its operation, application and specific
limitations.
•
Feed work into a bit or cutter against the direction of rotation
of bit or cutter.
•
Turn the machine off if it jams. A cutter jams when it digs too
deeply into the workpiece. (The motor force keeps it stuck in
workpiece.)
•
Use recommended accessories. Refer to page 11. Use of
improper accessories may cause risk of injury to persons.
•
Clamp workpiece or brace against column to prevent rotation.
•
Use recommended speed for drill accessory and workpiece
material.
WARNING:
Think Safety! Safety is a combination of operator com-
mon sense and alertness at all times when drill press is being used.
ASSEMBLY
MOUNT COLUMN ASSEMBLY TO BASE
Refer to Figure 7.
•
Place base (Ref. No. 1) on flat level surface.
•
Mount column assembly (Ref. No. 7) to base using four socket
head bolts (Ref. No. 6).
MOUNT TABLE
Refer to Figure 7.
•
Loosen set screw (Ref. No. 15). Remove rack and rack retaining
ring (Ref. Nos. 8 and 14) from column (Ref. No. 7).
•
Place worm gear (Ref. No. 18) into hole of table bracket (Ref. No.
11). Make sure worm gear meshes with pinion gear (Ref. No. 17).
•
Place rack inside table bracket assembly with large, unma-
chined portion of rack to the top. Slide rack into slot in bracket
so that teeth of rack engage pinion gear in bracket.
•
Slide table assembly with rack over column. Place bottom end
of rack inside beveled edge of column flange.
•
Slide rack retaining ring over column with beveled edge down.
Position ring against top of rack so that rack is in beveled edge
of ring. Secure ring with set screw (Ref. No. 15).
•
Rotate table assembly around column. Adjust rack retaining
ring as necessary to prevent binding of rack.
•
Attach crank handle (Ref. No. 19) to shaft on worm gear, rotate
worm gear to remove slack, and shoulder crank handle against
table bracket. Secure handle with set screw.
•
Thread handle (Ref. No. 16) into table bracket assembly. Position
bracket over the center of the base and secure bracket in
position.
MOUNT HEAD ASSEMBLY
Refer to Figure 9.
WARNING:
Although compact, the drill press head assembly is
heavy. Two people are required to mount the drill press head
assembly onto the column.
•
Slide drill press head assembly onto top of column.
•
Position head so that it is centered over base.
•
Secure head by tightening the set screws (Ref. No. 24) on the
right side of the head casting.
INSTALL QUILL FEED HANDLES
Refer to Figure 8.
Thread the two quill feed handles (Ref. No. 18) securely into pinion
assembly (Ref. No. 17).
INSTALL CRANK ARM AND FEED GRIP
Refer to Figure 8.
•
Attach crank arm (Ref. No. 20) to pinion (Ref. No. 17) using sock-
et head bolt (Ref. No. 19).
•
Thread feed grip (Ref. No. 21) into crank arm and secure with
hex nut.
Palmgren Operating Manual & Parts List
80150