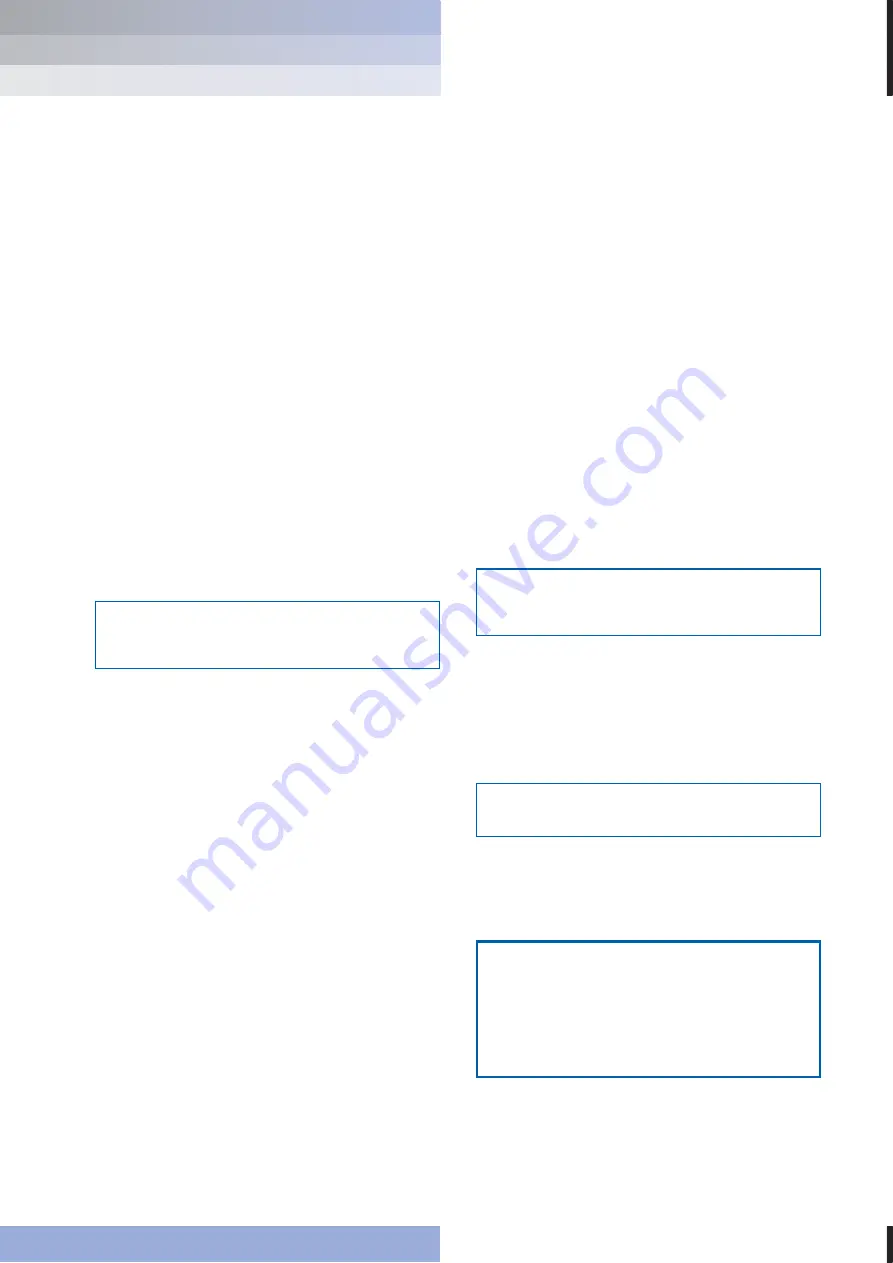
UT319
UT319 Series
R E T U R N L I N E I N - TA N K F I LT E R S
s e r v i c e
i n s t r u c t i o n s
2
1
Specifications
Housing materials:
Head and Cover:
Cast aluminium
YR85 option available for
cast iron head and cover
Shell:
Steel, with corrosive resistant
plating
Maximum operating pressure:
10 bar (150 psi)
Element burst pressure:
UE319 element 10 bard (150 psid) differential minimum
Operating temperature range:
-29°C to 120°C (-20°F to 250°F) with fluorocarbon seals for
petroleum based and specified synthetic fluids
60°C (140°F) maximum in HWCF, water-oil emulsion or
water glycol
Bypass valve setting options:
1.7 ± 0.3 bard (25 ± 5 psid) cracking pressure
4.5 ± 0.3 bard (65 ± 5 psid) cracking pressure
Seals:
Fluorocarbon
The actual operating conditions should be checked by the user
to ensure that the element, housing and all seals are
compatible with the fluid and application, and are within local
safety codes. Please contact Pall or an approved distributor if
further information is required.
2
Receipt of equipment
The filter housing, and any optional equipment, are packed
individually for assembly by the customer. Unpack carefully
and ensure optional items are not mislaid in packaging to be
discarded.
3
General sources of information
3.1
For dimensions, operating parameters,
assembly/element part number, ordering information,
notes, performance data and specifications refer to
datasheet IMUT319EN.
3.2
This equipment has been assessed in accordance with
the guidelines laid down in the European Pressure
Directive 97/23/EC and has been classified within sound
engineering practice S.E.P. We hereby declare the
equipment meets the requirements of article 3, section
3, thus meeting the directive requirements. Under the
provisions of this directive the filter assembly is suitable
for use with group 2 fluids only.
3.3
Where under reasonably foreseeable conditions,
including external fires, the allowable limits could be
exceeded, suitable protective devices must be installed
by the customer within the connecting fluid system.
4
Installation of housing
4.1
The filter should be installed vertically with the cover
pointing upwards.
4.2
The minimum clearance required for element removal of
is as follows:
4.2.1
UT319 series: 229mm (9in) for length 8,
361mm (14.2in) for length 13, 534mm (21in) for
length 20 and 1042mm (41in) for length 40
assemblies.
4.2.2
The UT319 Housing is supplied without a filter
element. For element installation and servicing
procedures, refer to Section 7.
4.3
Threaded pressure gauges or electrical pressure
switches, when fitted, hand tighten plus 1-2 turns with a
wrench. Threaded differential pressure indicator, if fitted,
must be torque tightened to 30-33 ft/lb or 40-45 Nm.
If no differential pressure warning device is ordered, the
shipping plug must be removedand replaced with a ‘B’
type blanking plug (HA9000-P8-Kit Z) and torque
tightened to 40 lb/ft /54 Nm.
NOTE: Never place the port plug in this port without first
installing uniform size -014 O-ring in lower O-ring groove,
otherwise a small bypass flow will result, allowing contaminant
downstream of the filter element.
NOTE: The UT319 housing is supplied with two machined
pressure gauge/switch ports and one differential pressure
indicator port, all fitted with blanking plugs.
4.4
Mount the filter assembly in position using four 3/8-16
bolts (housing with 'A' ports) or M10 x 1.25 bolts
(housing with 'C' ports) in the holes on the head
mounting pads. Torque bolts to 16-20 lb/ft
(22-27 Nm).
4.5
Install the filter housing using additional piping/valving to
allow complete filter assembly bypass if filter maintenance
is required without system shutdown. This series is not
available in a duplex or service bypass configuration.
NOTE: Piping supports should be provided as close as is
practicable to the port connections in order to minimize
external loads. This filter assembly must not be electronically
isolated from the user’s earthing system. This filter assembly
must be earthed by connecting the user’s earthing system to
one of the inlet/outlet connections.
4.6
Connect lines or hoses to housing inlet ports.
Note: Painting of the filter housing is optional. The coating on
the filter housing is a suitable painting base. Cover the
pressure warning device and nameplate if painting of the
housing takes place.
CAUTION:
Maximum surge flow should not exceed 1.3 times
normal flow.
WARNING:
USE FITTINGS OR ADAPTORS COMPATIBLE WITH
PORTS SUPPLIED AS SHOWN BY PART NUMBER ON
NAMEPLATE AND NOTED IN DATA SHEETS: USE OF
INCORRECT FITTINGS OR ADAPTORS CAN CAUSE
FILTER HOUSING OR MANIFOLD FAILURE
RESULTING IN LOSS OF PRESSURE AND POSSIBLE
SYSTEM FAILURE OR PERSONAL INJURY.
CAUTION:
Reverse flow through filter element will cause damage.
CAUTION:
Never operate the filter unless all warning device ports
are sealed.