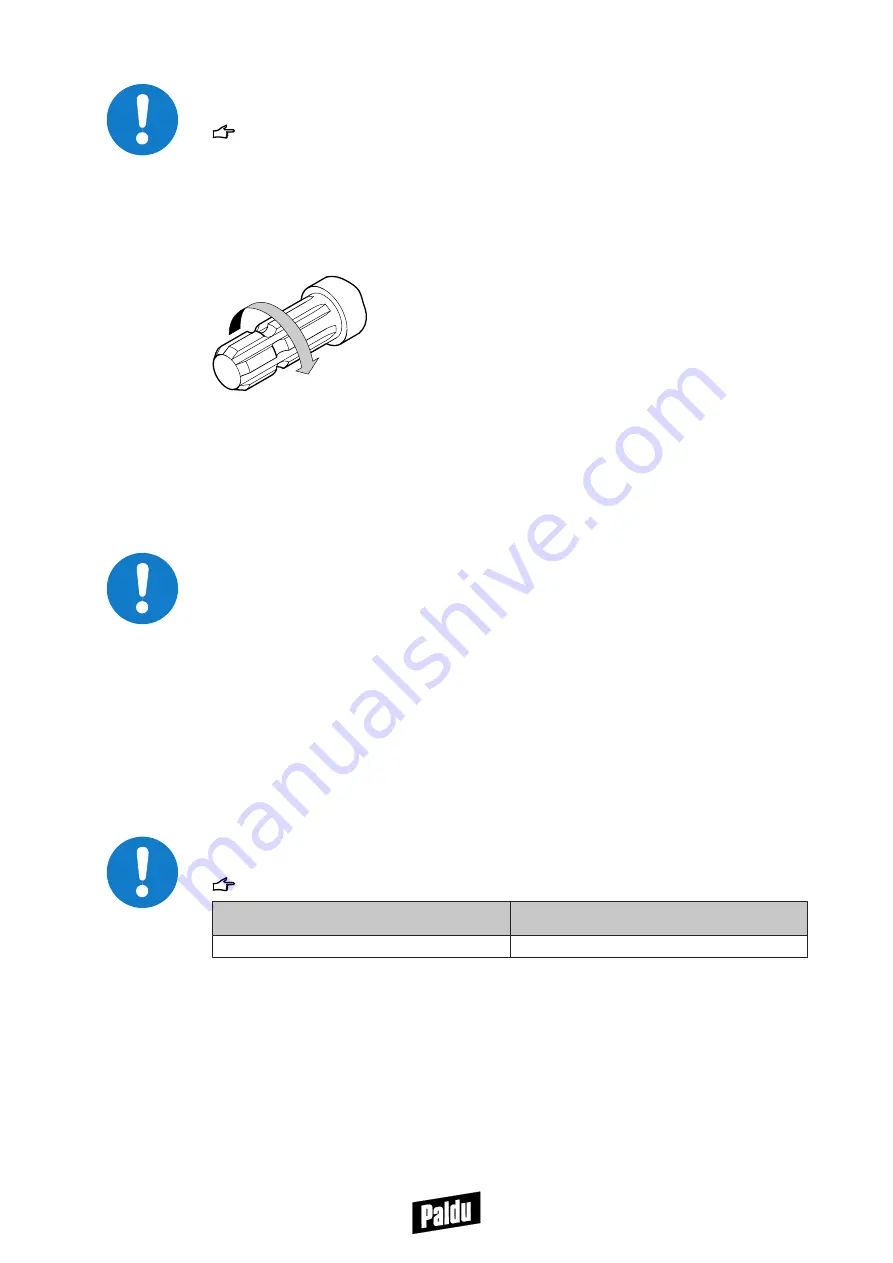
A tight plug connection can rip the CEE plug out of the switch housing.
▪ This can be remedied using standard plugs and a silicone spray.
Any such damage to the switch is not covered by the guarantee.
Driven by tractor via cardan shaft (type Z)
▪ Assemble the machine on the three-point linkage of the tractor.
▪ Attach the universal joint shaft and secure with the safety chain.
▪ Clockwise rotation of the tractor PTO shaft.
▪ Turn the tractor's manual throttle to minimum.
▪ Slowly engage the tractor PTO shaft and allow the machine to start moving.
▪ Set the required PTO shaft speed using the manual throttle.
Maximum PTO shaft speed:
▪ 380 rpm
The maximum PTO shaft speed must on no account be exceeded, otherwise the oil will
become too hot. This leads to premature wear and leaks in the pump, cylinder and hydraulic
pipes.
Before disengaging the universal joint shaft, set the manual throttle of the tractor to
minimum.
The universal joint shaft must be stored in the universal joint shaft linkage when it is
disconnected.
Driven by the tractor's hydraulic system (type PS)
▪ Assemble the machine on the three-point linkage of the tractor.
▪ Connect the hydraulic hoses to the tractor's hydraulic system.
▪ Turn the control valve on the tractor to the "On" position.
Ensure that the viscosity of the tractor hydraulic oil is compatible with that of the machine.
▪ Hydraulic oil HLP M46
Observe the flow and return.
Maximum efficiency of tractor's hydraulic
system
Maximum working pressure of tractor's
hydraulic system
16 l/min
230 bar
4.2
4.3
Start-up
15
Summary of Contents for 1100-12
Page 35: ......
Page 36: ...Your Paldu Dealer ...