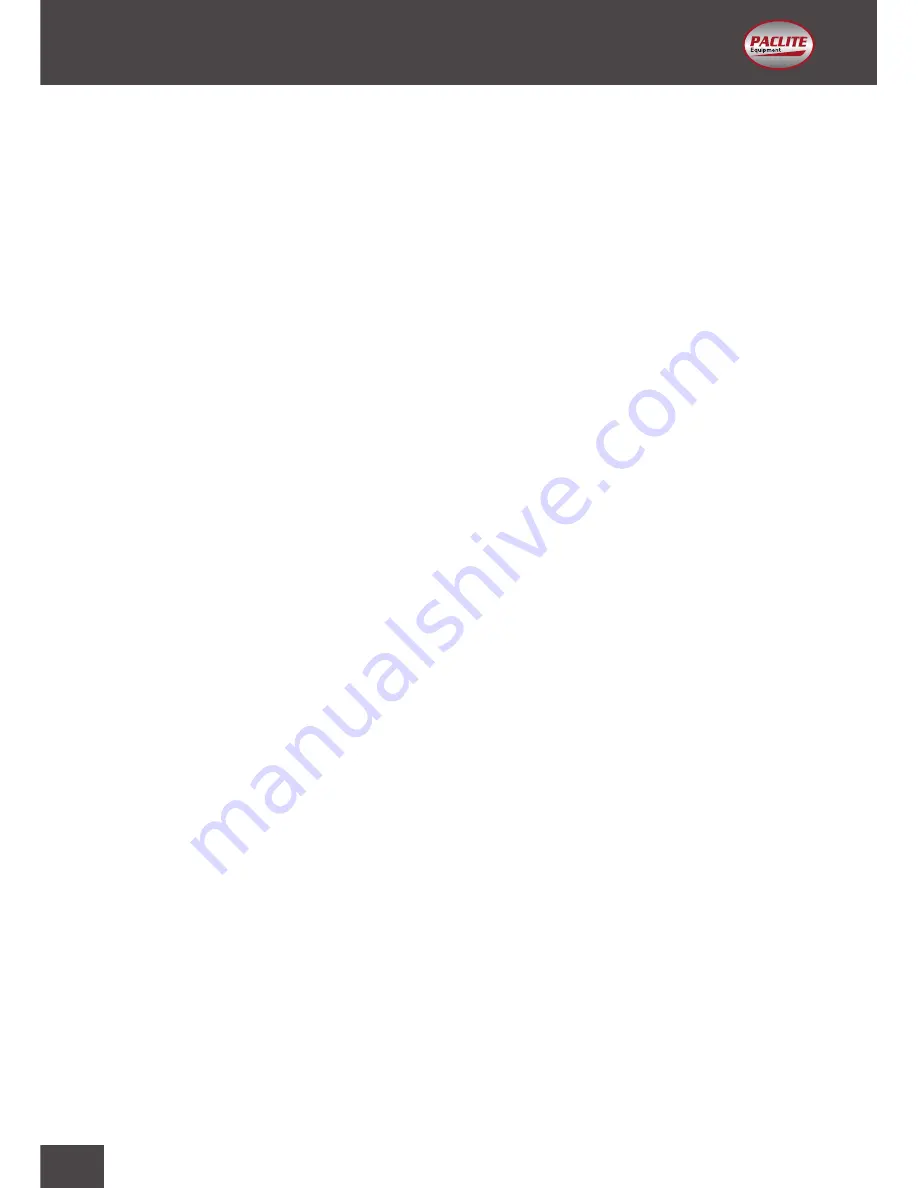
MASTER 600-700-900-1200
12
FLOATING OPERATION
Before starting the floating operation make sure that the Round Pan is correctly mounted on the finishing
blades. Be aware that with the blade arms turning clockwise, the floats should also be positioned in the same
way. The slab will be ready to work for the first floating operation when the heel of your shoe leaves a print of
2-3mm on the surface of the slab. On all other floating operations the blades should be almost flat. After the
floated slab has set and your footprint is only slightly visible, it is ready to start the finishing operation. The
timing of all these operations is dependent on weather conditions. After each operation the engine should be
stopped.
Never park the machine with the engine running, especially during the floating operation when the concrete is
relatively soft. If you were to leave it running on soft concrete in the same position, the finished floor tolerances
would be damaged as the concrete would be pushed down and spread out under the weight of the machine.
FINISHING OPERATION
After the floating operation, the first thing to do is remove the Round Pan from the finishing blades and clean
the blades, spider plate and protection ring of cement/concrete paste collected during the floating operation.
Increase the blade pitch up to 10 mm for the first finishing operation and then continue to increase the pitch
on the subsequent finishing operations.
Continue the finishing passes until you obtain the desired finished floor surface. The time required between
each finishing pass is dependent on weather conditions, cement and water content of the concrete. If some
areas of the concrete set harden too fast, you may apply a small amount of water with a brush to help achieve
a finish. Be careful when running the machine on areas where water has been applied because the machine
will tend to skate away as the water will act as a lubricant and reduce friction. Be sure to have a safe hold on the
handle and maintain control of the machine at all times.
PITCH ADJUSTMENT
The pitch control knob is in easy reach of the operator. He pitch adjustment has a limited pitch variation. Rotate
the pitch control knob clockwise to tilt the blades and counterclockwise to flatten the angle of the blades.
Adjustment is based on the desired performance for the specific job application.
SPIDER PLATE
From experience we know that a lack of lubrication on the trowel arms can lead to problems. During assembly
we undertake the greasing and sealing of the trowel arms on the spider plate. Greasing should be carried out
on a weekly basis using the grease nipple provided. If an arm becomes jammed, this is probably due to an arm
being bent and will need replacing.
Summary of Contents for MASTER 600
Page 18: ...MASTER 600 700 900 1200 18...
Page 34: ...MASTER 600 700 900 1200 34...
Page 50: ...MASTER 600 700 900 1200 50...
Page 66: ...MASTER 600 700 900 1200 66...
Page 69: ...MASTER 600 700 900 1200 69 67 68 70 71 71 72 73 74 74 75 78 79 80 81...
Page 71: ...MASTER 600 700 900 1200 71 WARNING MASTER...
Page 72: ...MASTER 600 700 900 1200 72 1 2 3 4 5 1 2 3 4 5 6 7 8 9 10 11 6 7 8 9...
Page 73: ...MASTER 600 700 900 1200 73 1 1 M12 x 90 x1 M12 x 75 x1 30 2 1 3 M8 2 M8 4 3 1 4 2 3 4 4 4 5 4...
Page 76: ...MASTER 600 700 900 1200 76 2 3 10...
Page 77: ...MASTER 600 700 900 1200 77 Paclite MASTER 900 1200...
Page 78: ...MASTER 600 700 900 1200 78 MASTER Paclite Paclite Paclite 4 20 3 50 6 100...
Page 82: ...MASTER 600 700 900 1200 82...
Page 98: ...MASTER 600 700 900 1200 98...
Page 114: ...MASTER 600 700 900 1200 114...
Page 130: ...MASTER 600 700 900 1200 130...
Page 146: ...MASTER 600 700 900 1200 146...
Page 147: ...MASTER 600 700 900 1200 147...