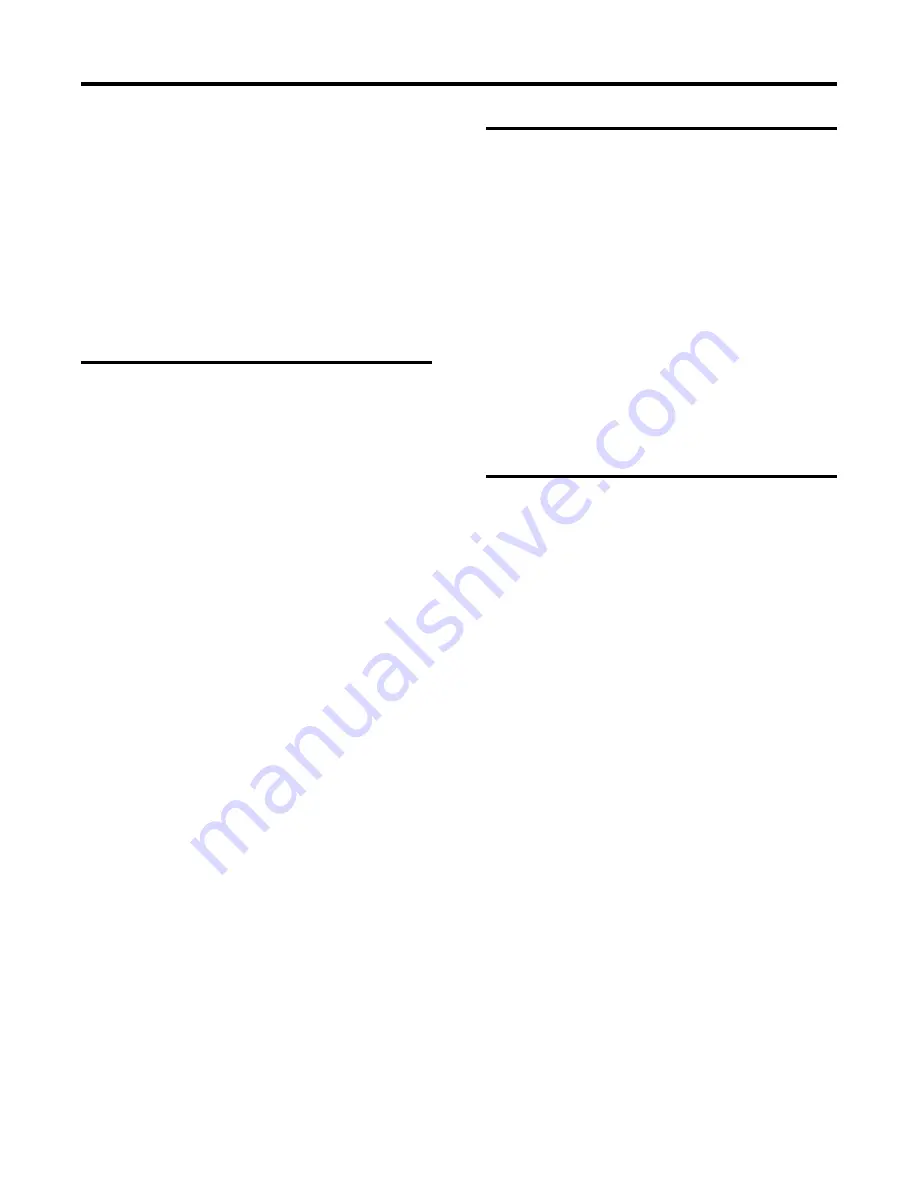
WARNING! For the safe operation of this machine fol-
low the instructions given in this booklet and the train-
ing given by your supervisor. Failure to do so can result
in personal injury and/or damage to machine and prop-
erty!
DO NOT OPERATE MACHINE IN AN EXPLOSIVE
ENVIRONMENT!
The models shown in this manual are intended for com-
mercial use.
PREPARATION
To prepare the machine for operation, make sure it is of
correct voltage and properly assembled. If in doubt, ask
your supervisor.
Your new floor machine operates in a straight-line forward
motion, rather than the normal side to side motion of a
conventional single disc machine. Be prepared by having
your floor area cleared and ready for the fast action of a
burnisher.
Prepare the floor area by sweeping, dusting or mopping as
needed. Check the proper application recommendations
and procedures found on the label of your finish container.
IF IN DOUBT, CALL YOUR SUPERVISOR .
WARNING! NEVER USE THIS MACHINE WITH
FLAMMABLE OR EXPLOSIVE MATERIAL!
For Burnishing:
Select the correct clean floor pad (your
supplier can help you). The lighter color floor pads (buff or
white) are normally used for the burnishing procedure.
NEVER OPERATE THE MACHINE WITHOUT THE
FLOOR PAD INSTALLED!
It is very important to select clean, dry pads of uniform
thickness. Pads with high or low sections, or hard or soft
spots are unacceptable. Pads of open weave are recom-
mended; because close weaves tend to load up fast, bog
down the machines, cause circuits to overload and gener-
ally give poor results.
Tip the machine back to expose the pad driver. Remove
the pad center lock ring. Carefully center the pad onto the
pad driver and secure with the locking ring. Check for
level, centering and flatness.
OPERATION
Set the machine upright onto the pad. Plug the machine’s
power cable into a properly grounded outlet (see Safety
Instructions). Next, release the handle locking knob and
allow the handle to lower into a comfortable position. Then
secure the handle locking knob. This will allow the opera-
tor to easily control the brush pressure.
Depress the handle slightly to elevate the pad from the floor.
This is to avoid burning the floor on initial start up, before
the operator is ready to move forward. Pull out on the
“Watch Dog” Safety Lock button and start the machine by
depressing either the left or right switch levers.
When you’re ready to move forward, lower the machine
head and pad to the floor and proceed forward in a straight
line, at a steady pace.
MAINTENANCE
AFTER EACH USE:
Store the machine in a clean dry
area. Wipe the entire machine and cord down with a clean
cloth. Remove the pad and clean thoroughly. Wrap the
machine’s electrical cord onto the handles and the cord
hook provided. CHECK the cord and plug for nicks, cuts
or damage. Report these to your supervisor for correction.
WARNING! Always disconnect the machine’s electri-
cal plug from the electrical outlet before performing any
service, maintenance, pad changing or inspection of the
machine.
MOTOR:
The motor is lubricated for life under normal
use. No oiling or greasing is necessary. However, if the
machine is used in dusty areas the motor should be cleaned.
Blowing the motor out with compressed air or with the
exhaust from a vacuum is suggested. Keeping the motor
clean will allow the clear passage of air for ventilation and
prevent overheating.
BELT TENSION:
Proper belt tension is important for
smooth operation and belt life. Check the belt tension and
have no more than a 1/8-inch deflection. If adjustment is
needed, loosen the four (4) motor mounting bolts. Then
turn the belt tension adjustment screw (located at the rear
of the chassis) clockwise to tighten or counter-clockwise to
loosen the belt. Tighten the four (4) motor mounting bolts.
CARBON BRUSH INSPECTION:
Long life 3000-hour
carbon brushes are installed in the motor. The machine is
also equipped with a carbon brush wear indicator light to
signal when a carbon brush change is required.
OPERATING PROCEDURES
3