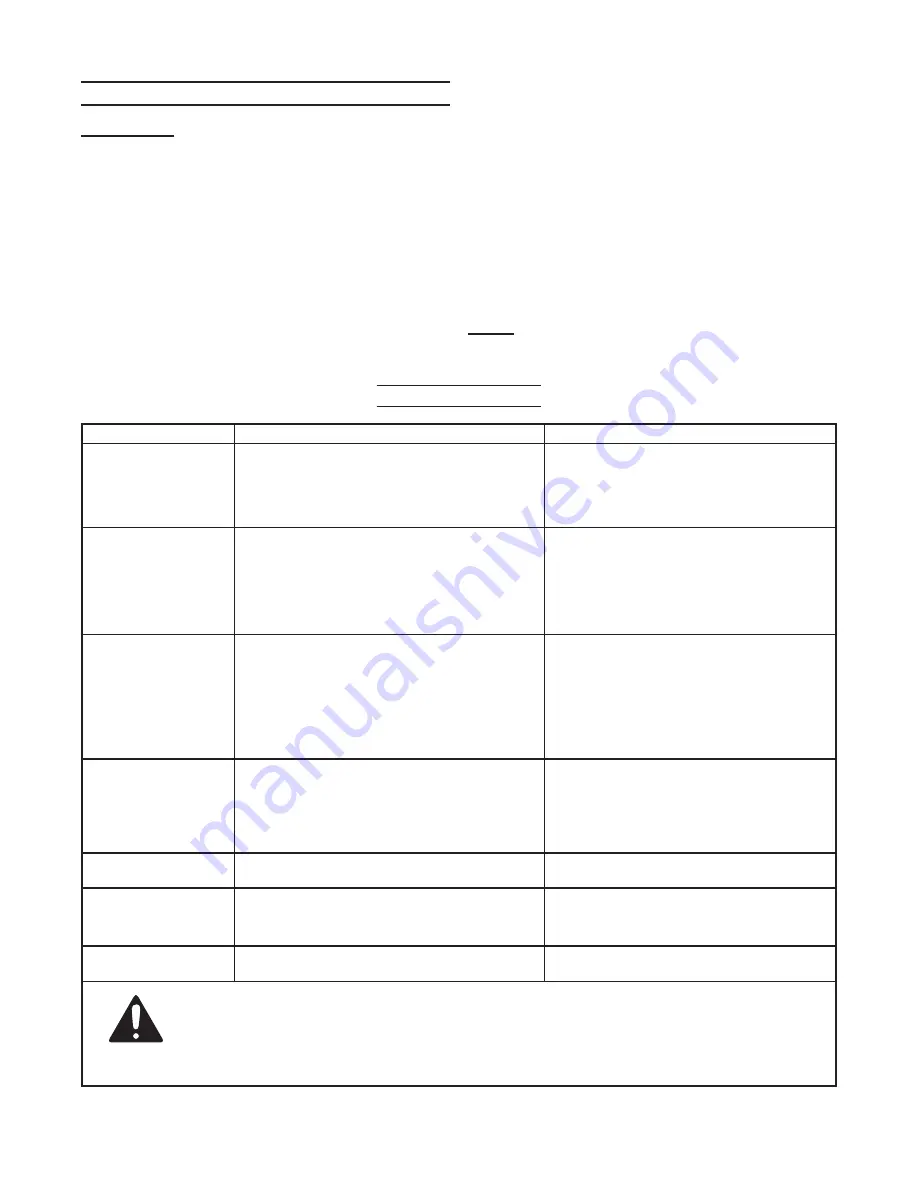
Page 8
For technical questions, please call 1-800-444-3353.
SKU 47907
MAintEnAnCE
WArning! disconnect pump from power
source before maintenance.
Clean the inlet screen on the intake port
1.
regularly to remove accumulated debris.
Wipe the pump clean with a soft, damp
2.
cloth with soapy water. Do not use sol-
vents. Do not get the electrical compo-
nents wet.
Drain water from pump before storage
3.
by disconnecting the water lines and
turning the Pump upside down. If storing
the pump for a long time, store it in a dry
location, and apply a light layer of oil to
the metal parts prior to storage, to inhibit
rust.
do not expose to freezing tem-
peratures.
After storage, check the Impeller to make
4.
sure it turns easily and is not oxidized.
note:
Turn off the
Switch
and unplug the
pump when performing maintenance.
troubleshooting
Problem
Cause
Solution
The pump won’t start
No power.
1.
Pressure switch disconnected.
2.
Thermal Protection cut out.
3.
Blocked impeller.
4.
Check connections, and breaker/fuse.
1.
Check gauge.
2.
Allow pump to cool.
3.
Free the impeller.
4.
The pump operates
but it won’t discharge
water
Pump not primed.
1.
Lift height exceeded.
2.
Inlet tube not submerged.
3.
Air in suction pipe.
4.
Inlet screen clogged.
5.
Prime pump.
1.
Reduce lift height.
2.
Submerge the inlet.
3.
Check pipe and seals.
4.
Clean screen.
5.
Only a low volume of
water flows
Inlet pipe is too small.
1.
Liquid is too dirty.
2.
Lifting height exceeded.
3.
Tank’s rubber bladder under-inflated.
4.
Piping corroded, causing friction.
5.
Increase pipe diameter.
1.
Clean screen frequently.
2.
Reduce lifting height.
3.
Inflate to 26-29 PSI.
4.
Replace piping, with plastic where
5.
possible.
Motor overheats often
Extension cord too long or wire size too
1.
small.
Pump cycling too often.
2.
Eliminate use of extension cord or use
1.
shorter/heavier gauge cord.
Cut-in and cut-out pressure may be set
2.
too closely; Have the pressure switch
adjusted by a qualified technician.
Pump/motor cycles
rapidly
Cut-in and cut-out pressure may be set too
closely.
Have the pressure switch adjusted by a
qualified technician.
Tank bladder will not
hold pressure
Air inlet valve is leaking.
1.
Bladder is broken.
2.
Check air tank for leaks using soapy
1.
water and replace bladder if needed.
Replace bladder.
2.
Water pumps
intermittently
Water level is being drawn below foot valve. Lower foot valve.
Follow all safety precautions whenever diagnosing or servicing the pump.
disconnect power supply before service.
do not disassemble the pump or motor as this will damage the water seals.
All repairs should be performed by a qualified technician.
rEV 06i, 07g, 08l