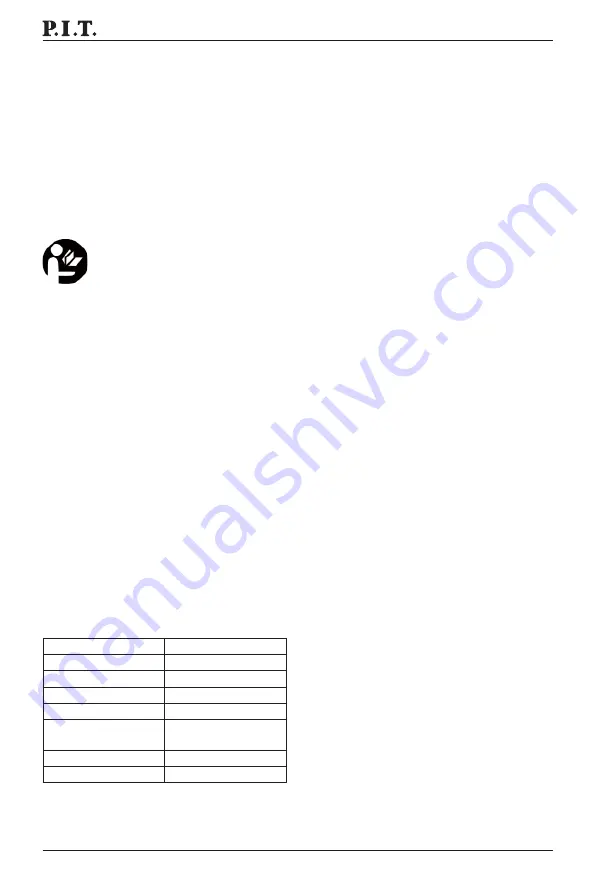
Automatic Welding Machine
4
droplets.
Do not allow water to enter the
inside of the machine.
►
Avoid welding in dusty or corrosive gas
environments.
►
Avoid gas welding in a strong air flow
environment.
►
A worker who has a pacemaker in-
stalled should consult a doctor before
welding.
Because the electromagnetic
field can interfere with the normal opera-
tion of the pacemaker.
Product description and specifi-
cations
Read all safety warnings and all
instructions.
Failure to follow the
warnings and instructions may result
in electric shock, fire and/or serious
injury.
Intended use
Semiautomatic inverter type direct current
welding machine (hereinafter referred to as
the product) is designed for welding using the
MIG / MAG methods (welding with electrode
wire in a shielded gas) and MMA (manual arc
welding with stick fusible covered electrodes).
The product can be used for welding various
types of metals.
Product features
The numbering of the components shown re-
fers to the representation of the power tool on
the graphic pages.
1. Polarity reversing cable
2. Torch connection socket
3. Power connector “+”
4. Power connector “-”
5. Fan
6. Power button
7. Connection for shielding gas
8. Power cable inlet
Technical data
Model
PMIG145-C1
3BUFEWPMUBHF
190-250 V~ / 50 Hz
3BUFEQPXFS
4000 W
Output current range
10-145 A
Wire diameter (MIG)
0.8-1.0 mm
Electrode diameter
(MMA)
1.6-3.2 mm
Duty cycle (DC)
25
˫
60%
Weight
7 kg
Contents of delivery
Automatic welding machine
1pc
Cable with electrode holder
1pc
Cable with grounding terminal 1pc
Torch cable
1pc
Welding shield
1pc
Hammer brush
1pc
Instruction manual
1pc
Note
The text and numbers of the instructions may
contain technical errors and typographical er-
rors.
Since the product is constantly being im-
proved, P.I.T. reserves the right to make
changes to the specifications and product
speci
fi
cations speci
fi
ed here without prior no-
tice.
Preparation for work
Place the machine on a flat surface. The
workplace must be well ventilated, the weld-
ing machine must not be exposed to dust,
dirt, moisture and active steam. To ensure
adequate ventilation, the distance from the
apparatus to other objects must be at least 50
cm.
ATTENTION!
To avoid electric shock, use
only electrical mains with a protective earth
conductor and grounded receptacles. DO
NOT alter the plug if it does not
fi
t into the out-
let. Instead, a quali
fi
ed electrician must install
an appropriate outlet.
Ensuring the safety of preparation
for work
Before turning on the product, set the switch
to the “0” position, and the current regulator to
the extreme left position.
Prepare for work:
– Prepare the parts to be welded;
– Provide adequate ventilation in the work-
place;
– Make sure that there are no solvent
vapors, flammable, explosive and chlo-
rine-containing substances in the air;
– Check all connections to the product; they
must be made correctly and securely;
– Check the welding cable, if damaged it
must be replaced;
– The power supply must be equipped with
protective systems.
If you encounter problems that you cannot
cope with, contact the service center.
Summary of Contents for PMIG145-C1
Page 1: ......
Page 2: ...Automatic Welding Machine 1...
Page 15: ...14...
Page 16: ...15...
Page 17: ...16 90 10 40 MIG MAG...
Page 20: ...19 1 2 3 MIG MAG 15 2 2 4 VRD 12 24 VRD VRD MIG MAG...
Page 21: ...20 V U 6 16 GAS...
Page 22: ...21 10 NO GAS...
Page 23: ...22 off 1 2 3 4 5 6 20 30 7...
Page 25: ...24 7...
Page 26: ...25 1 2 3 4 5 6 7 U0 V X I2 A U2 V U1 I1max A I1eff A IP21S S...
Page 27: ...26 P I T P I T P I T https pittools ru servises 0 40 80...
Page 28: ...27 2 2 2 1 2 OnePower 12 I 3 4...
Page 29: ...28 3 2 2 5...
Page 34: ......