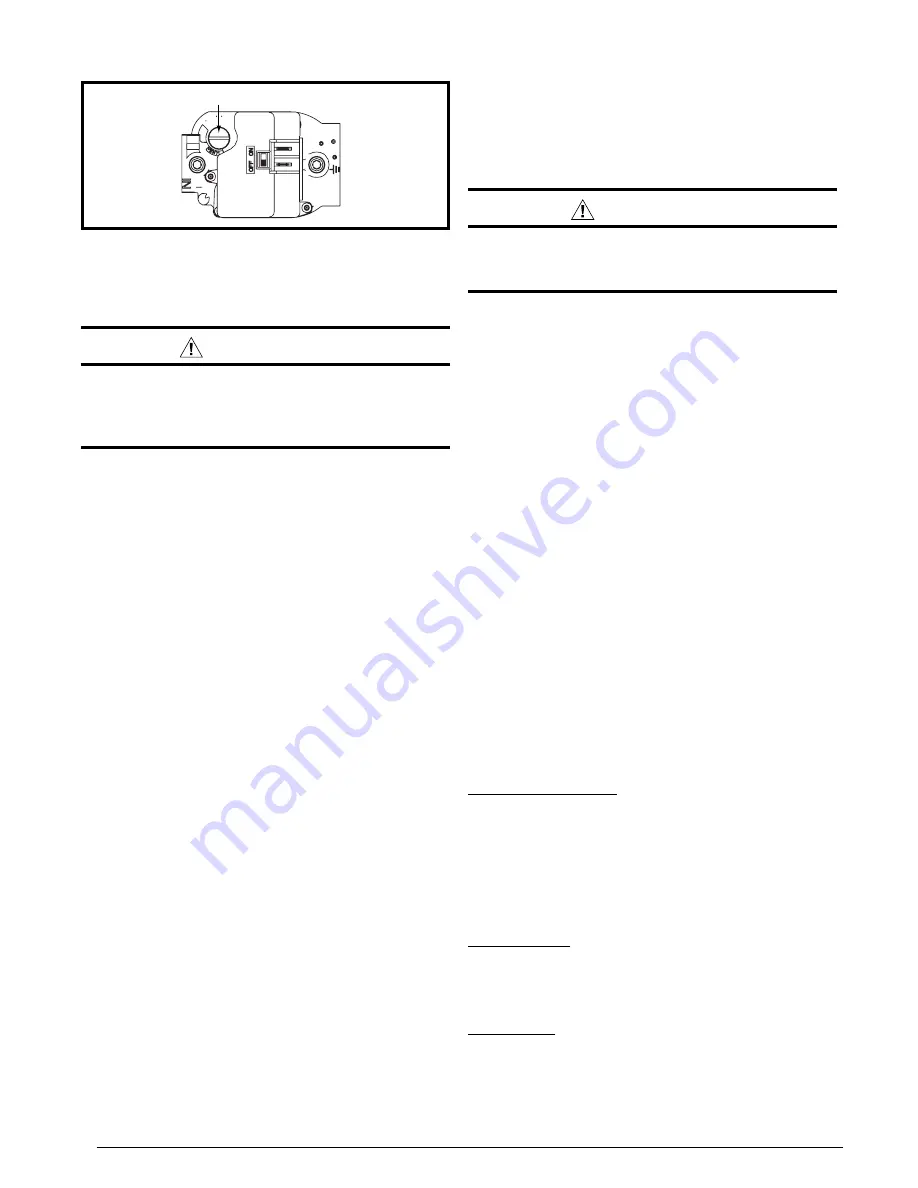
26
Figure 28. Regulator Capscrew
Capscrew
6. The manifold pressure must be set to the appropriate
value for each installation by a qualified installer, service
agency or the gas supplier.
WARNING:
Do not attempt to drill the gas orifices. Use only
factory supplied orifices. Improperly drilled
orifices may cause fire, explosion, carbon
monoxide poisoning, personal injury or death.
a.) Obtain the manifold pressure setting required for
this installation by referring to
for
Propane or
b.) Remove the regulator capscrew (
) from the
INLET side of the regulator.
c.) Slowly turn the adjustment screw inside the regulator
to obtain the appropriate manifold pressure.
NOTE:
Turning the screw clockwise increases the
pressure and turning the screw counter-clockwise
decreases the pressure. To prevent backing the screw
all the way out from the valve, turn the screw slowly.
d.) Replace and tighten the regulator capscrew over the
adjustment screw.
Verifying & Adjusting Temperature Rise
After installation of the furnace, confirm the temperature rise
of the furnace is within the limits specified on the rating plate.
Any temperature rise outside the specified limits could result
in premature failure of the heat exchanger.
1. Place thermometers in the return and supply air stream
as close to the furnace as possible. The thermometer on
the supply air side must be shielded from direct radiation
from the heat exchanger to avoid false readings.
2. Adjust all registers and duct dampers to the desired position
and run the furnace for 10 to 15 minutes before taking
any temperature readings. The temperature rise is the
difference between the supply and return air temperatures.
For typical duct systems, the temperature rise will fall within the
limits specified on the rating plate with the blower speed at the
factory recommended setting. If the measured temperature
rise is outside the specified limits, it may be necessary to
change the speed of the blower.
NOTE:
Lowering the blower speed will increase the
temperature rise and a higher blower speed will decrease
the temperature rise.
The furnace is equipped with a 5-speed ECM motor. Heating
and cooling speed selection is made by moving the switch on the
integrated control inside of the furnace. The furnace is shipped
from the factory pre-wired for 4 blower speeds. There is a fifth
alternate speed available on the motor. To utilize the alternate
speed, remove the wire at the motor plug of the desired speed to
be changed (H, MH, ML, L). Reconnect this wire to the alternate
motor plug speed tap.
Verifying Burner Operation
CAUTION:
The door over the burners may only be open
for inspection purposes only. The door must be
installed during unattended operation.
1. Remove the burner compartment door.
2. Set the thermostat above room temperature and observe
the ignition sequence.
NOTE
: The burner flame should
carry over immediately between all burners without lifting
off, curling, or floating. The flames should be blue, without
yellow tips.
3. After validating the flame, change thermostat setting to
below room temperature.
4. Verify the burner flame is completely extinguished.
5. Replace the burner compartment door.
Verifying Operation of the Supply Air Limit
Switch
NOTE
: A properly functioning limit switch should turn off
the gas valve when the return is blocked (time depends on
how well the return air is blocked). The circulating air and
combustion blowers should continue to run when the limit
switch opens.
1. Verify the blower door is securely mounted in place and
that there is power to the furnace.
2. Block the return airflow to the furnace by installing a close-
off plate in place of or upstream of the filter(s).
3. Set the thermostat above room temperature and observe
the Operating Sequence.
4. Remove the close-off immediately after the limit switch
opens. If the furnace continues to operate with no return
air, set the thermostat below room temperature, shut off
power to the furnace, and replace the limit switch.
System Operation
(Gas) Heating Mode
When the thermostat calls for heating, the circuit between
R
and
W
is completed. The furnace control board initiates the
ignition sequence. Approximately 30 seconds after the gas
flame has proven, the blower motor will start. The blower will
continue to operate after the call for heat has been removed
for a selectable (switch on furnace control board) number of
seconds.
NOTE:
All on- and off-delays for heating continue
to be controlled by the furnace control board.
Cooling Mode
When the thermostat calls for cooling or heat pump heating,
the circuit between
R
,
G
, and
Y
(
O
is ignored by the blower)
is completed. The blower runs at the selected cooling motor
torque.
Manual Fan
Select the speed using the jumper on the control board.