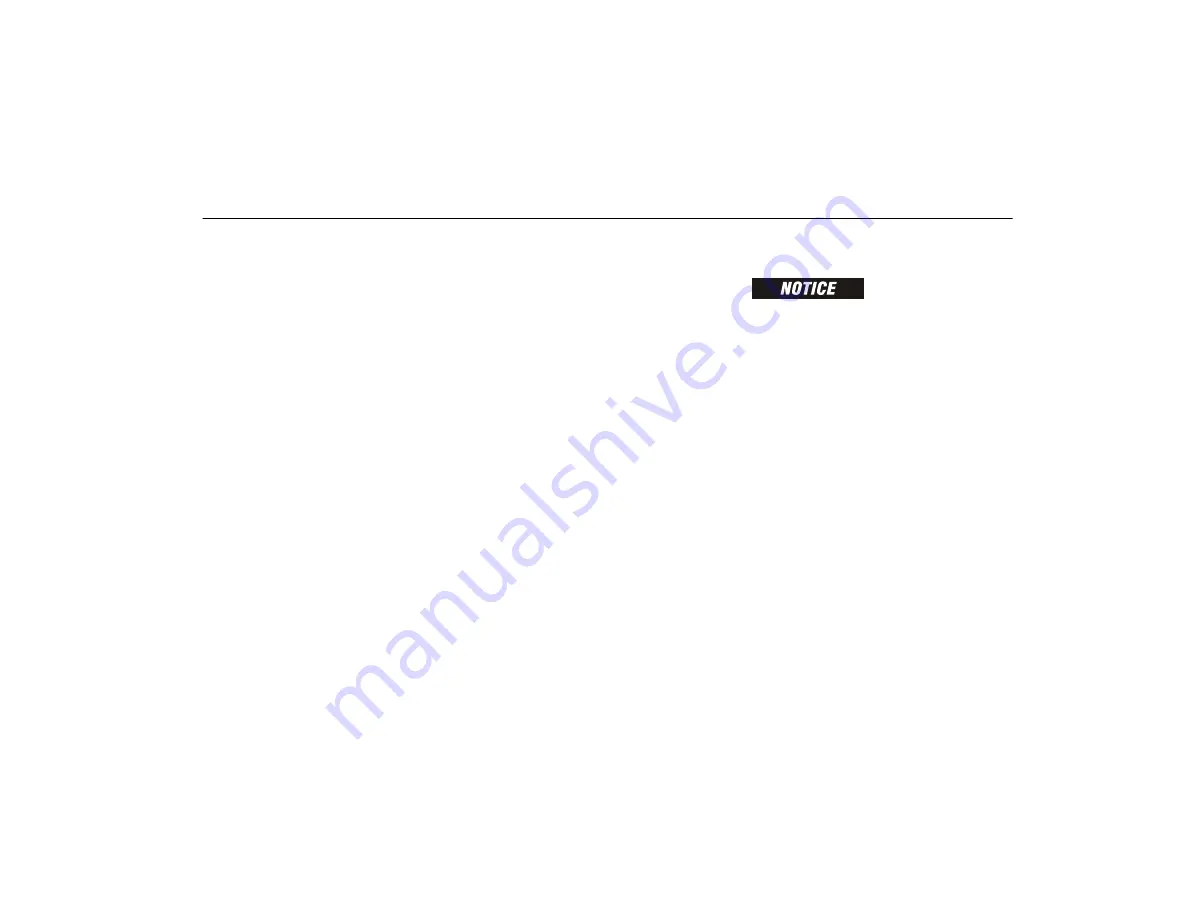
SECTION 5 - EMERGENCY PROCEDURES
3121258
– JLG Lift –
5-1
SECTION 5. EMERGENCY PROCEDURES
5.1 GENERAL
This section explains the steps to be taken in case of an
emergency situation while operating.
5.2 INCIDENT NOTIFICATION
JLG Industries, Inc. must be notified immediately of any inci-
dent involving a JLG product. Even if no injury or property
damage is evident, the factory should be contacted by tele-
phone and provided with all necessary details.
In USA:
JLG Phone: 877-JLG-SAFE (554-7233)
Outside USA:
240-420-2661
E-mail:
Failure to notify the manufacturer of an incident involving a
JLG Industries product within 48 hours of such an occur-
rence may void any warranty consideration on that particular
machine.
FOLLOWING ANY INCIDENT, THOROUGHLY INSPECT THE MACHINE
AND TEST ALL FUNCTIONS FIRST FROM THE GROUND CONTROLS,
THEN FROM THE PLATFORM CONTROLS. DO NOT LIFT ABOVE 3 M (10
FT.) UNTIL YOU ARE SURE THAT ALL DAMAGE HAS BEEN REPAIRED, IF
REQUIRED, AND THAT ALL CONTROLS ARE OPERATING CORRECTLY.
5.3 EMERGENCY OPERATION
Operator Unable to Control Machine
IF THE PLATFORM OPERATOR IS PINNED, TRAPPED OR
UNABLE TO OPERATE OR CONTROL MACHINE:
1.
Other personnel should operate the machine from
ground controls only as required.
2.
Other qualified personnel on the platform may use the
platform controls. DO NOT CONTINUE OPERATION IF
CONTROLS DO NOT FUNCTION PROPERLY.
3.
Cranes, forklift trucks or other equipment can be used to
stabilize motion of the machine.