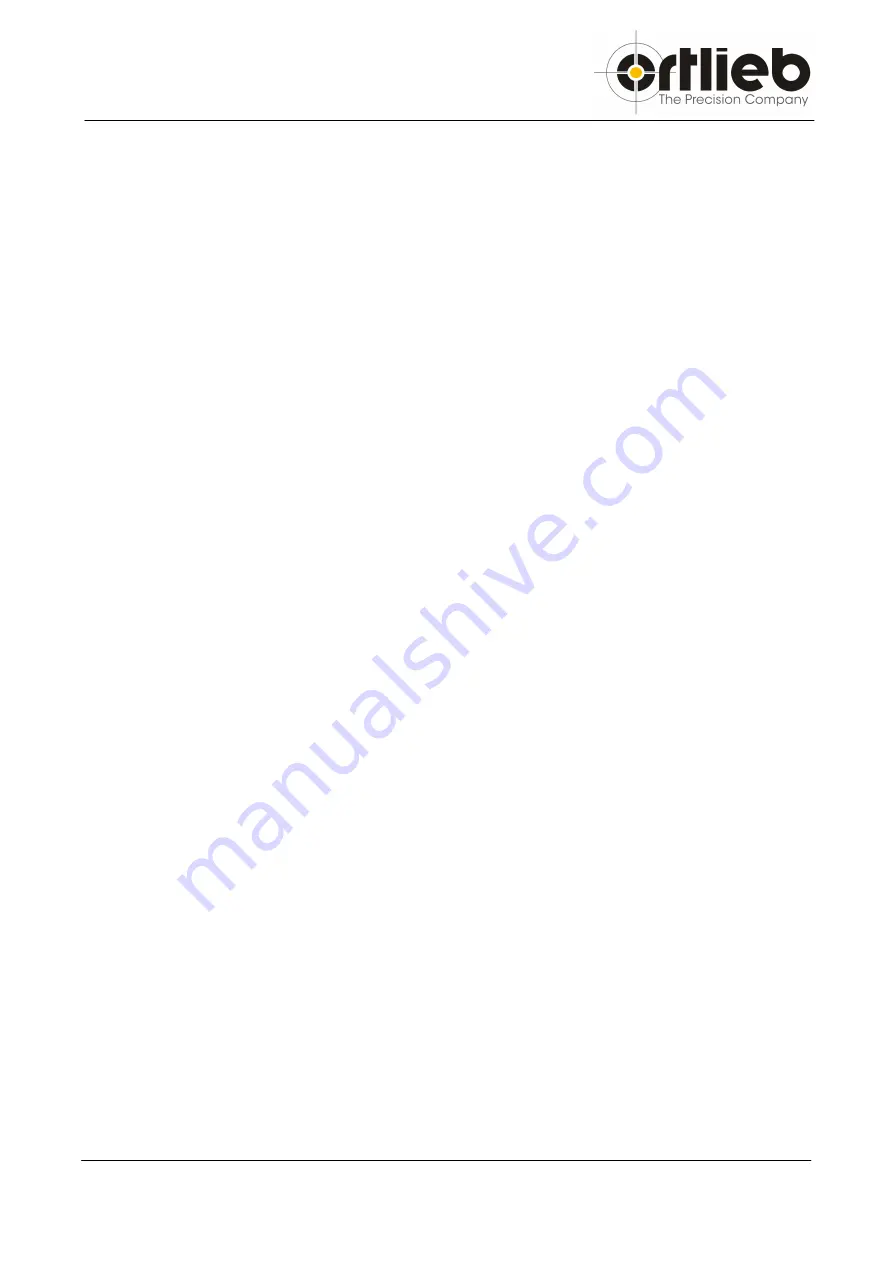
5. General Safety Instructions
Ortlieb Präzisionssysteme GmbH & Co. KG • Jurastr.11 • 73119 Zell unter Aichelberg • Germany
17
e-mail: [email protected] • www.ortlieb.net
10.)
The tool gripper is a part which is subject to wear. Under favourable operation conditions,
the complete tool gripper must be exchanged every 2x10
6
load alternations. We do not
assume liability and guarantee on consequential damages in case only parts (TGR +
TGZ) are exchanged).
11.)
Refer to the installation instructions for information about how to change the TG. Before
installing the TG, check the spindle for damage. Grease the functional surfaces.
12.)
For optimal drawing-in force, RPM
max.
and n
max.
, please refer to WLZ RWTH Aachen:
Richtlinie zur Grenzbelastbarkeit HSK-Schnittstelle (Project Jan. 2003)
13.)
Tools must meet DIN 69893 standards. After usage, please check that the cooling
lubricant supply tube in the tool is tightened. If it gets loose, the tool cannot be pulled-in
properly!
14.)
Without an HSK tool insert, there is no operation of the spindle allowed.
(Out-of-balance caused by TGR + TGZ)
15.)
After every crash, the TGR and TGZ must always be exchanged completely.
16.)
The clamping force transmitted to the HSK by the tool gripper TG should not be below the
standard values specified in DIN 69063 / DIN 69893. It is also important that the
functional surfaces and the clamping system are greased regularly (with ball bearing or
assembly grease.)
Based on experience, re-greasing should be done after every 200.000 load alternations
at the least in order to keep the clamping force as uniform as possible. Regular
measurement of the clamping force, either quarterly or semi-annual, will ensure the
required safety for the work process.
17.)
Check the tightening of the draw-bolt TGZ and the drawbar regularly to ensure a proper
function of the tool-gripper.
A loose draw-bolt causes a loss of clamping force and ejects the tool far over the allowed
max. 0,5mm.