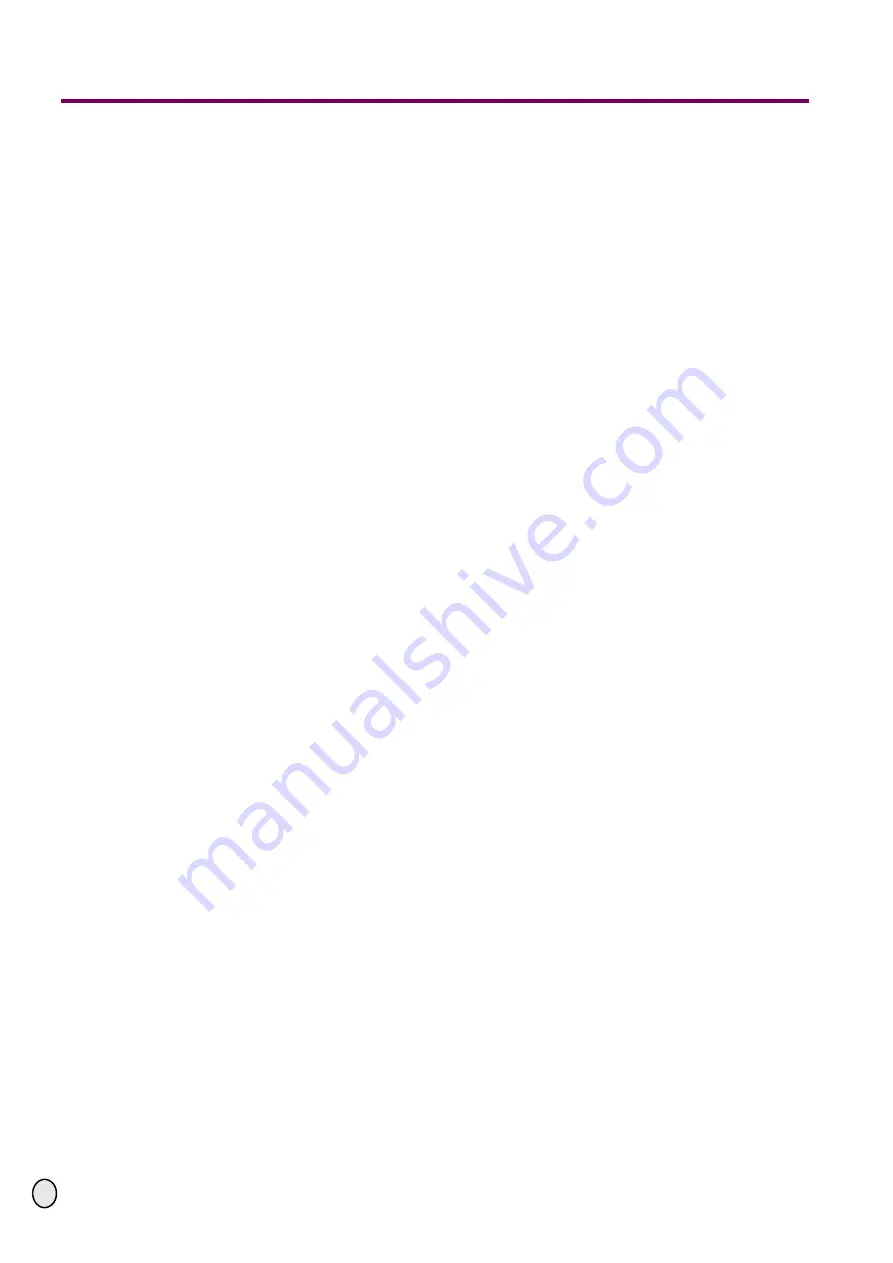
OPTIMUM
M A S C H I N E N - G E R M A N Y
Appendix
30 / 11 / 2007
Page 38
Appendix Add-on kit D240/D280 ; Version 1.3.3
©
2007
GB
7
Appendix
7.1
Copyright
©
2007
The documentation is copyright. All derived rights are also reserved, especially those of transla-
tion, re-printing, use of figures, broadcast, reproduction by photo-mechanical or similar means
and recording in data processing systems, neither partial or total.
The company reserves the right to make technical alternations without prior notice.
7.2
Terminology/Glossary
Term
Explanation
CNC
Computerised Numerical Control
Adapter kit
Components
Movement rate
Free, smooth mobility of components
Blow-back proof plas-
tic tip hammer
A plastic tip hammer which is filled with
sand which does not prevent to spring
back when knocking.
Disassembly
Remove, relieve
Toothed belt disc
Disc with gearing to receive the toothed
belt.