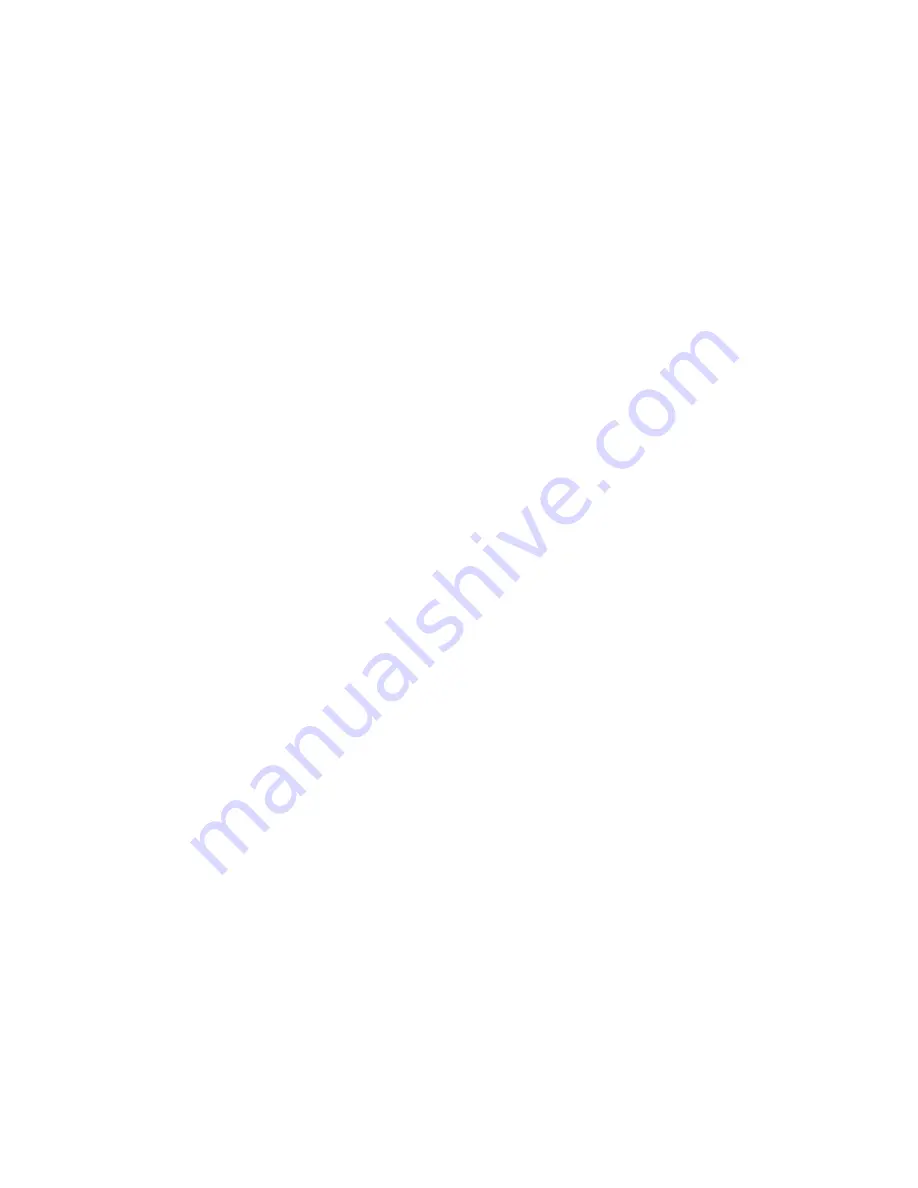
4-4
INTEGRA Operations Revision A
7/26/00
20-0200-231 (CR), 20-0200-232 (Std), 20-0200-251 (CD)
In order to maintain optimum cleaning efficiency, the brushes are
periodically cleaned and/or conditioned through processes defined
in three sets of variables provided on the
BRUSH STATION DEFINE
CLEANING SCREEN
. See “Modify Brush Cleaning Options” on page
9-23, and “Process Idle Time” on page 4-6.
2%
NH
4
OH
Application (Standard)
The 2% NH
4
OH drip configuration is standard for Brush Station #1
in the Integra system. Brush Station #1 may also be configured for
29% NH
4
OH through-the-brush chemical delivery.
If Brush Station #1 is set up with the 2% NH
4
OH chemical drawer
and the specified process recipe for Brush Station #1 is set for
NH
4
OH cleaning, then for each EVENT in which it is activated, 2%
NH
4
OH drips from a drip manifold onto the top brush as it turns.
The DI HIGH FLOW valve is closed, to prevent the NH
4
OH from
becoming too dilute. The DI LOW FLOW has no solenoid/air valve
and is always on. Although process recipe (POR) dependent,
normally when the processing is complete, the DI HIGH FLOW
valve opens to allow DI water to flush the chemical and
contamination out of the brush.
29% NH
4
OH
TTB
Processing (Option)
When Brush Station #1 is configured with a 29% NH
4
OH chemical
drawer*, and the Process Recipe for Brush Station #1 is set with
NH
4
OH cleaning parameters, then for each EVENT in which
NH
4
OH is activated, 29% NH
4
OH flows from the chemical dispense
unit (CDU) into a mixing manifold housed in the 29% chemical
drawer. In the mixing manifold the 29% NH
4
OH mixes with DI
water, supplied through the DI LOW FLOW valve, to form a 2%
process solution. Exiting the mixing manifold, the 2% process
solution flows to the top brush core and out through the permeable
brush material as the brush turns.
B
CAUTION!:
In order to ensure operator safety, component reliability, and proper
wafer cleaning,
always
use 29% NH
4
OH in conjunction with the DI LOW FLOW option.
During 29% NH
4
OH processing (2% at the brush), the brushes continue
turning in opposite directions to exert constant pressure on the wafer,
keeping the wafer firmly pressed against the Brush Station rollers. The
continuously turning rollers rotate the wafer between the brushes. This
dual action of rotating the wafer between the turning brushes creates
the scrubbing action which cleans both surfaces of the wafer.
Summary of Contents for Synergy Integra
Page 8: ......
Page 24: ...1 4 INTEGRA Operations Revision A 7 26 00 20 0200 231 CR 20 0200 232 Std 20 0200 251 CD...
Page 38: ...2 14 INTEGRA Operations Revision A 7 26 00 20 0200 231 CR 20 0200 232 Std 20 0200 251 CD...
Page 222: ...9 62 INTEGRA Operations Revision A 7 26 00 20 0200 231 CR 20 0200 232 Std 20 0200 251 CD...
Page 314: ...10 76 INTEGRA Operations Revision A 7 26 00 20 0200 231 CR 20 0200 232 Std 20 0200 251 CD...