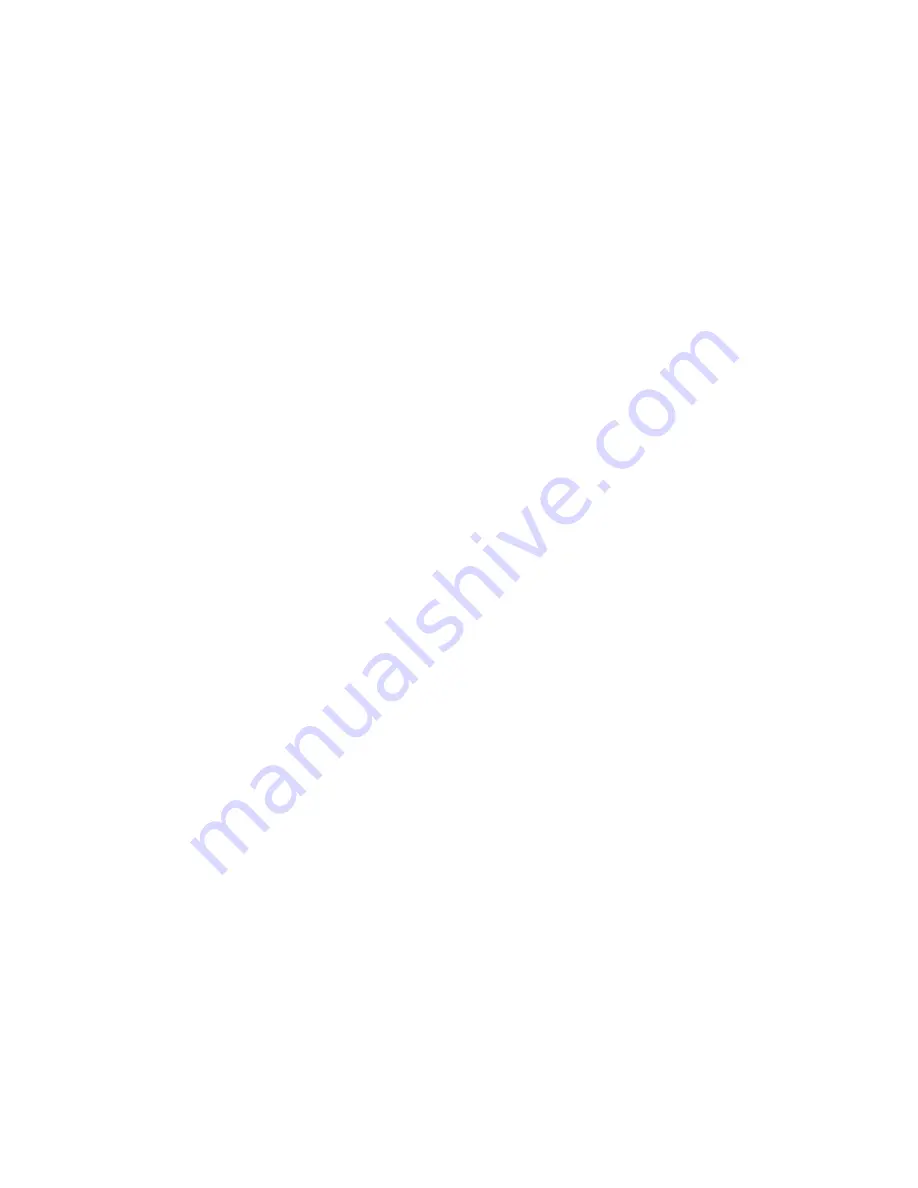
C h a p t e r 4 P R O C E S S D E S C R I P T I O N
7/26/00
INTEGRA Operations Revision A
4-3
20-0200-231 (CR), 20-0200-232 (Std), 20-0200-251 (CD)
BRUSH STATION #1
W
AFER
T
RANSPORT
I
N
As the wafer transfers from the Input Station to Brush Station #1, it is
sprayed with DI water as an initial rinse. A fiber optic sensor, located
between the Input Station and the Brush Station #1, detects the
wafer. (See “WAFER SENSOR” on page 3-11, in the sensor table.)
The top brush initially raises as part of the roller reset procedure and
is up as the wafer enter the station. The rollers are closed to a pre
programmed position according to wafer size. The upper brush
remains up for a set period of time after the sensor detects the trailing
edge of the wafer as it moves to the rollers. The upper and lower
brushes turn in opposite directions in such a way that they facilitate
the wafer movement in the same direction as the conveyor track. After
the time delay, the top brush moves down into place. Because the top
and bottom brushes turn in opposite directions, they exert constant
pressure on the wafer and guide it into the rollers.
W
AFER
C
ENTERING
The position of the rollers in combination with the continual forward
pressure exerted by the rotating brushes causes the wafer to be
centered between the brushes. Roller heights are set so that the wafer
is in correct contact with them, its horizontal position is adjusted
slightly so that no part of the wafer touches the conveyor track while
the wafer is being cleaned.
W
AFER
C
LEANING
Introduction
The wafer cleaning process used in Brush Station #1 contains variables
which may be programmed using the Process Recipe. Each cleaning
cycle has three programmable
EVENTS. Each EVENT has
six variables.
These variables are of two types, ON/OFF and variable settings.
1 ON/OFF options for
chemical dispense
(NH
4
OH or HF
depending on the station configuration),
DI HIGH FLOW
and
DI
LOW FLOW
.
2 Variable setting options for
TIME
,
ROLLER SPEED
, and
BRUSH SPEED
.
In addition to the three cleaning cycle programmable EVENTS, there
are also four independent EVENT settings that must be define for
the Brush #1 Process Recipe. For more information see “Modify
Brush #1 Recipe” on page 9-5.
Brush Station #1 usually processes with either 29% (standard) (see
“29% NH4OH TTB Processing (Option)” on page 4-4 for the actual
process) or 2% (option) NH
4
OH. The chemical dispense process for
each Process Recipe is defined in three EVENTS. Each EVENT allows
the choice of using NH
4
OH, DI HIGH FLOW, DI LOW FLOW or
certain combinations of the three.
Summary of Contents for Synergy Integra
Page 8: ......
Page 24: ...1 4 INTEGRA Operations Revision A 7 26 00 20 0200 231 CR 20 0200 232 Std 20 0200 251 CD...
Page 38: ...2 14 INTEGRA Operations Revision A 7 26 00 20 0200 231 CR 20 0200 232 Std 20 0200 251 CD...
Page 222: ...9 62 INTEGRA Operations Revision A 7 26 00 20 0200 231 CR 20 0200 232 Std 20 0200 251 CD...
Page 314: ...10 76 INTEGRA Operations Revision A 7 26 00 20 0200 231 CR 20 0200 232 Std 20 0200 251 CD...