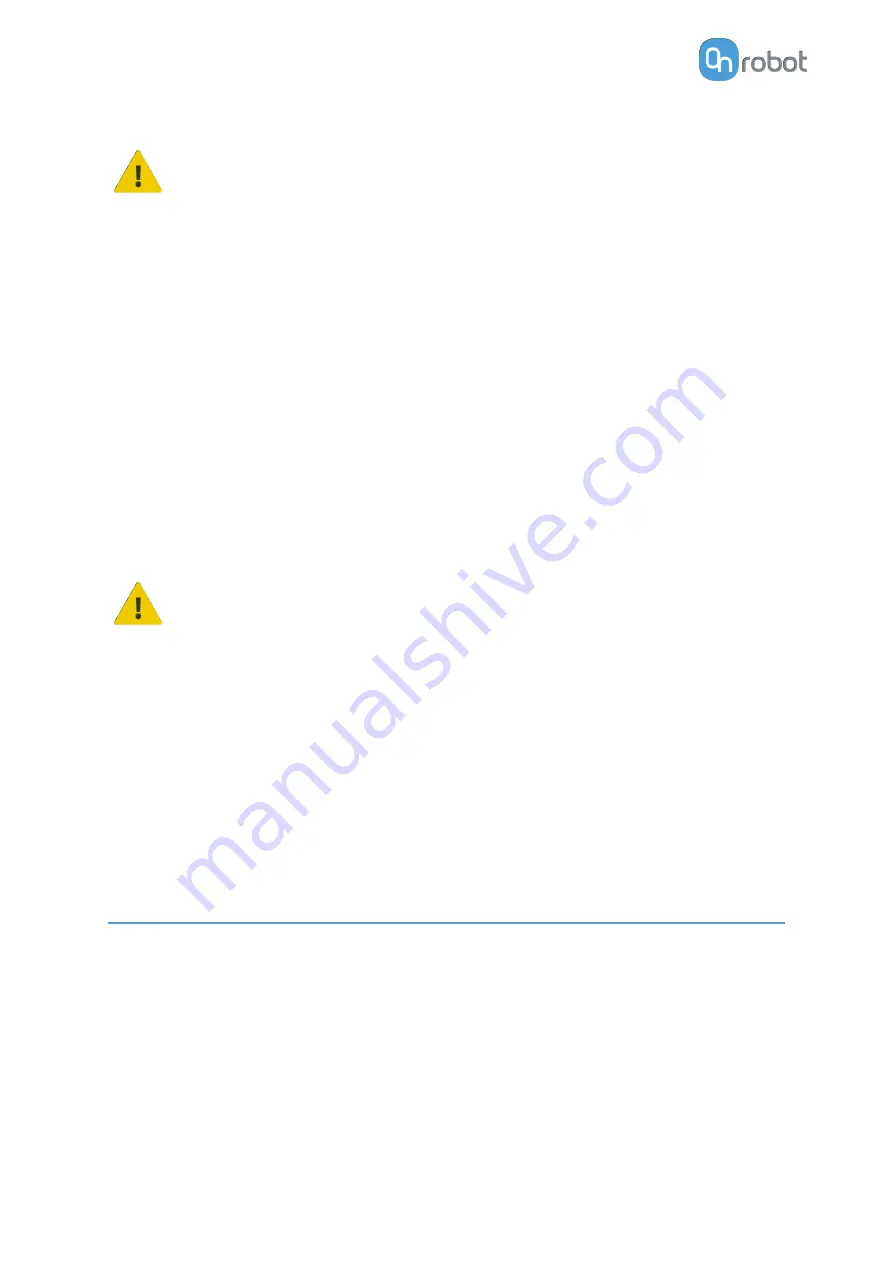
DANGER:
You must read, understand, and follow all safety information in this manual, and
the robot manual and all associated equipment before initiating robot motion.
Failure to comply with safety information could result in death or serious injury.
The information in this manual does not cover designing, installing, and
operating a complete robot application, nor does it cover other peripheral
equipment that can influence the safety of the complete system. The complete
system must be designed and installed in accordance with the safety
requirements set forth in the standards and regulations of the country where
the robot is installed.
Any safety information provided in this manual must not be construed as a
warranty, by OnRobot A/S, that the robot application will not cause injury or
damage, even if robot application complies with all safety instructions.
OnRobot A/S disclaims any and all liability if any of OnRobot tools tooling are
damaged, changed or modified in any way. OnRobot A/S cannot be held
responsible for any damages caused to any of OnRobot tools tooling, the
robot, or any other equipment due to programming errors or malfunctioning of
any of OnRobot tools.
WARNING:
OnRobot tools are not allowed to be exposed to condensing conditions when
power is on or when connected to a robot. If condensing conditions appear
during transport or storage, the product must be placed between 20 and 40
Celsius degrees for 24 hours before power is applied or before connected to a
robot.
It is recommended that OnRobot tools are integrated in compliance with the following guides
and standards:
•
ISO 10218-2
•
ISO 12100
•
ISO/TR 20218-1
•
ISO/TS 15066
2.3. Risk Assessment
The robot integrator must perform a risk assessment on the complete robot application.
OnRobot tools are only components in a robot application and therefore they can be only
safely operated if the integrator has considered the safety aspects of the whole application.
OnRobot tools are designed with relatively smooth and round design with a limited amount of
sharp edges and pinch points
In collaborative applications, the trajectory of the robot can play a significant safety role. The
integrator must consider the angle of contact with a human body, e.g. orientate OnRobot tools
and workpieces so that the contact surface in the direction of movement is as large as
possible. It is recommended that the tool connectors are pointed in the direction opposite to
the movement.
SAFETY
6