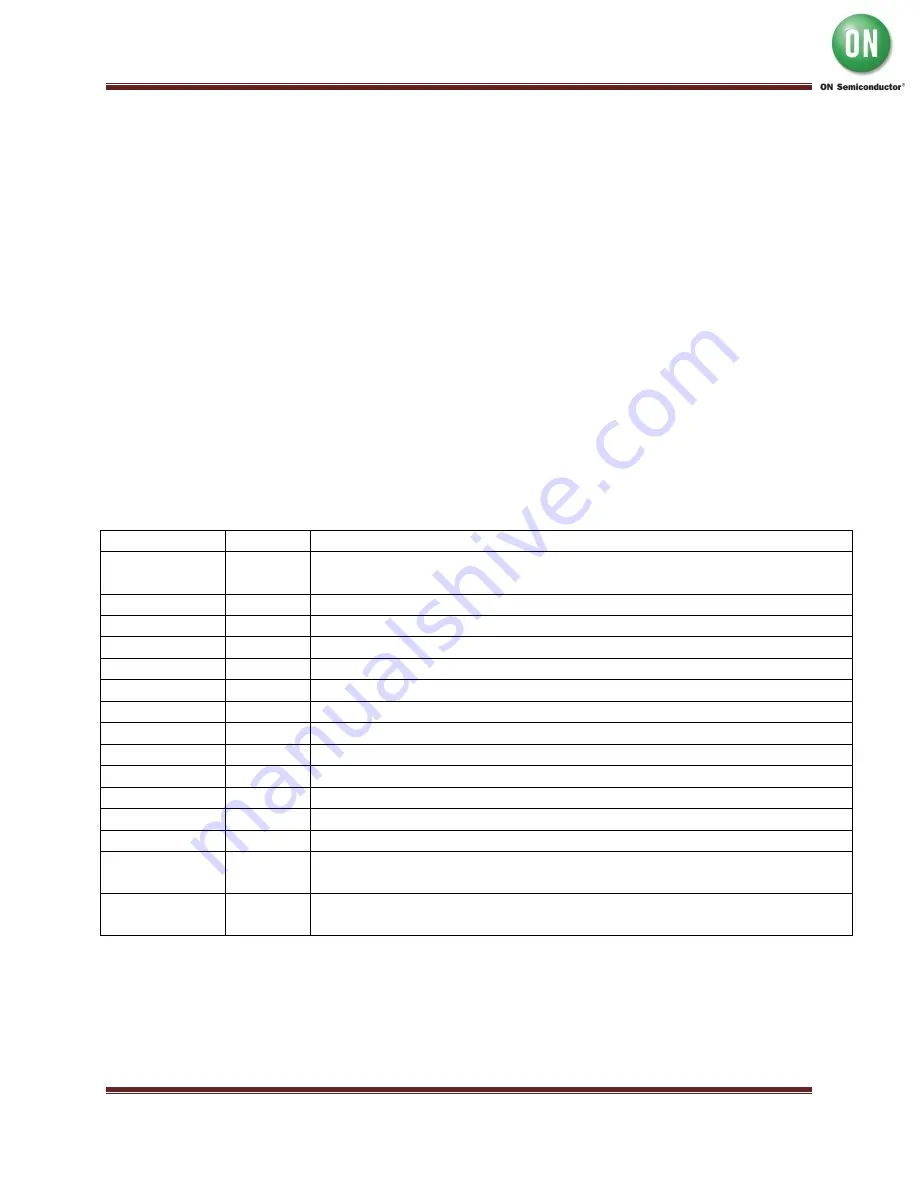
LV8811GEVB Evaluation Board User Guide
2.
Features
The followings are key features of the board.
•
Supports 12.0V (typ.) supply voltage
•
Speed control input: PWM duty cycle
•
Selectable Hall sensor type; sensor or IC
o
Factory default: configured for sensor type
•
Configureable minimum PWM duty cycle
o
Factory-default:
14% for enable (start)
8% for disable (stop)
•
Configurable lead angle range and its proportional constant to rotational speed
o
Factory-default:
15degree at the lowest FG frequency
Lead angle = 0.15 × 𝑓𝑓𝑓𝑓
𝐹𝐹𝐹𝐹
+ 15
Pin name
I/O
description
PWM
IN
Speed control PWM input. 20kHz – 50kHz 3Vpp
The higher duty cycle gives the higher rotational speed.
FG
OUT
3Vpp pulse whose frequency is proportional to motor speed
VTH
NA
Not applicable
RFS
Monitor Current feedback signal can be monitored
GND
IN/OUT Ground
VCC
IN
Power supply input. Typical 12V is assumed.
PWR
Floating No connection
RF
Monitor Power supply node for the power stage
VREG
OUT
3V voltage regulator output
CPWM
Monitor Triangle waveform of the PWM generator can be monitored
HB
OUT
Bias voltage output for a Hall sensor. 1.18V DC
IN1/IN2
IN
Hall sensor signal input
U/V/W Out
OUT
Motor driver output
MDS
IN
Voltage level of MDS pin (minimum duty cycle setting) can be
monitored.
PH1/PH2
IN
Voltage level of PH1 and PH2 pins (lead angle setting) can be
monitored.
Page 4