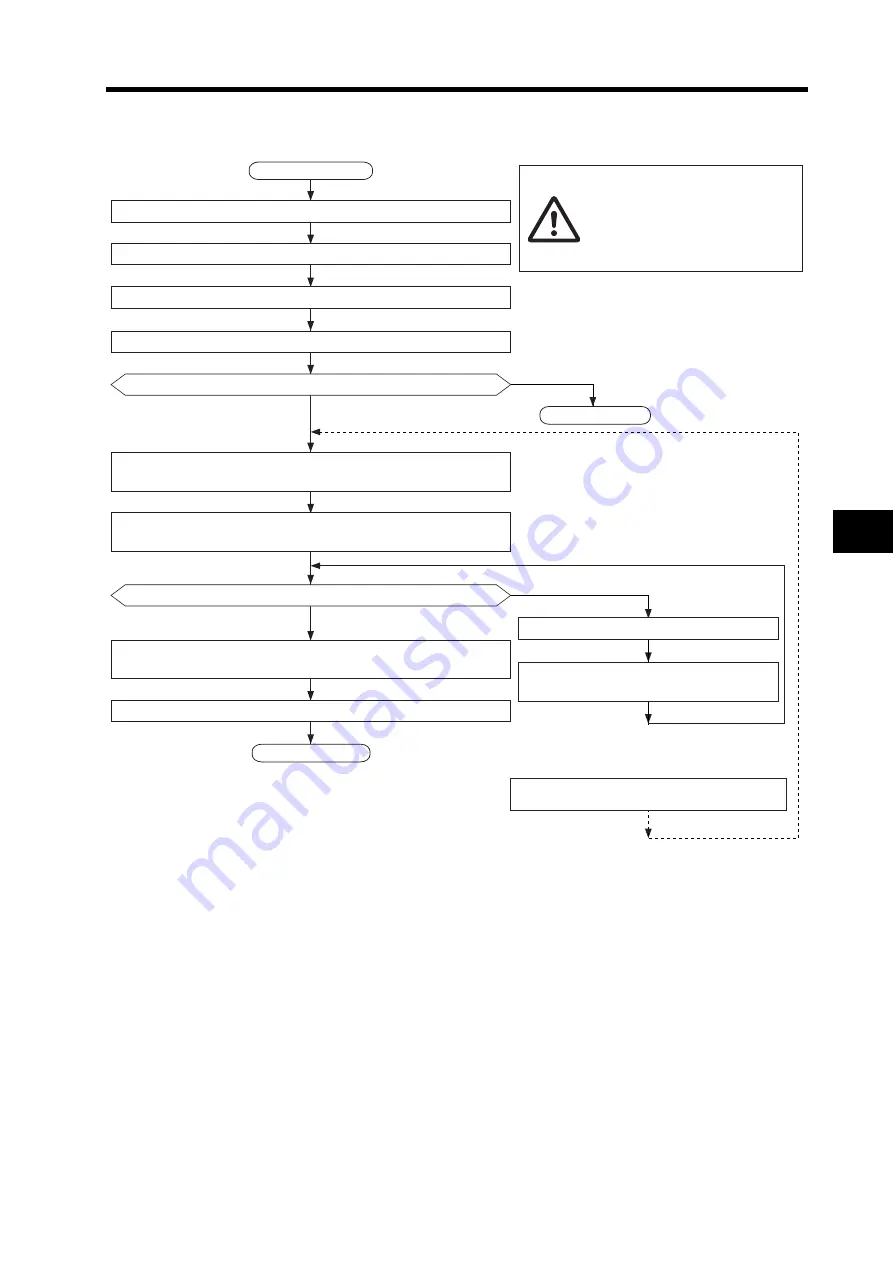
7-22
7-5 Manual Tuning
7
Adjustment Functions
Position Control Mode Adjustment
Use the following procedure to make adjustments in position control for the OMNUC G Series.
Write the data to EEPROM in the parameter write mode.
Increase the Position Loop Gain (Pn10),
but not so much that it causes overshooting.
Reduce the Speed Loop Gain (Pn11).
Start of adjustment
Disable realtime autotuning (Pn21 = 0 or 7).
Set each parameter to the values in Table 1.
Set the Inertia Ratio (Pn20) (value calculated at motor selection).
Operate with a normal operating pattern and load.
Positioning time and other operation performance satisfactory?
Yes
No
End of adjustment
Never make extreme adjustment or
changes to settings. Doing so will result
in unstable operation and may lead to
injuries. Adjust the gain in small
increments while checking Servomotor
operation.
Increase the Speed Loop Gain (Pn11),
but not so much that it causes hunting when the servo is locked.
Reduce the Speed Loop Integration Time Constant (Pn12),
but not so much that it causes hunting when the servo is locked.
Yes
No
Does hunting (vibration) occur when the Servomotor is rotated?
End of adjustment
Increase the Speed Loop Integration Time
Constant (Pn12).
If vibration does not stop no matter how many times
you perform adjustments, or if positioning is slow:
Increase the Torque Command Filter Time
Constant (Pn14).
Summary of Contents for R88D-GT series
Page 20: ...18 Table of Contents ...
Page 234: ...3 133 3 8 Reactor Specifications 3 Specifications ...
Page 448: ...7 37 7 5 Manual Tuning 7 Adjustment Functions ...
Page 474: ...8 25 8 5 Periodic Maintenance 8 Troubleshooting ...
Page 475: ...Chapter 9 Appendix 9 1 Connection Examples 9 1 9 2 Parameter Tables 9 11 ...
Page 509: ......