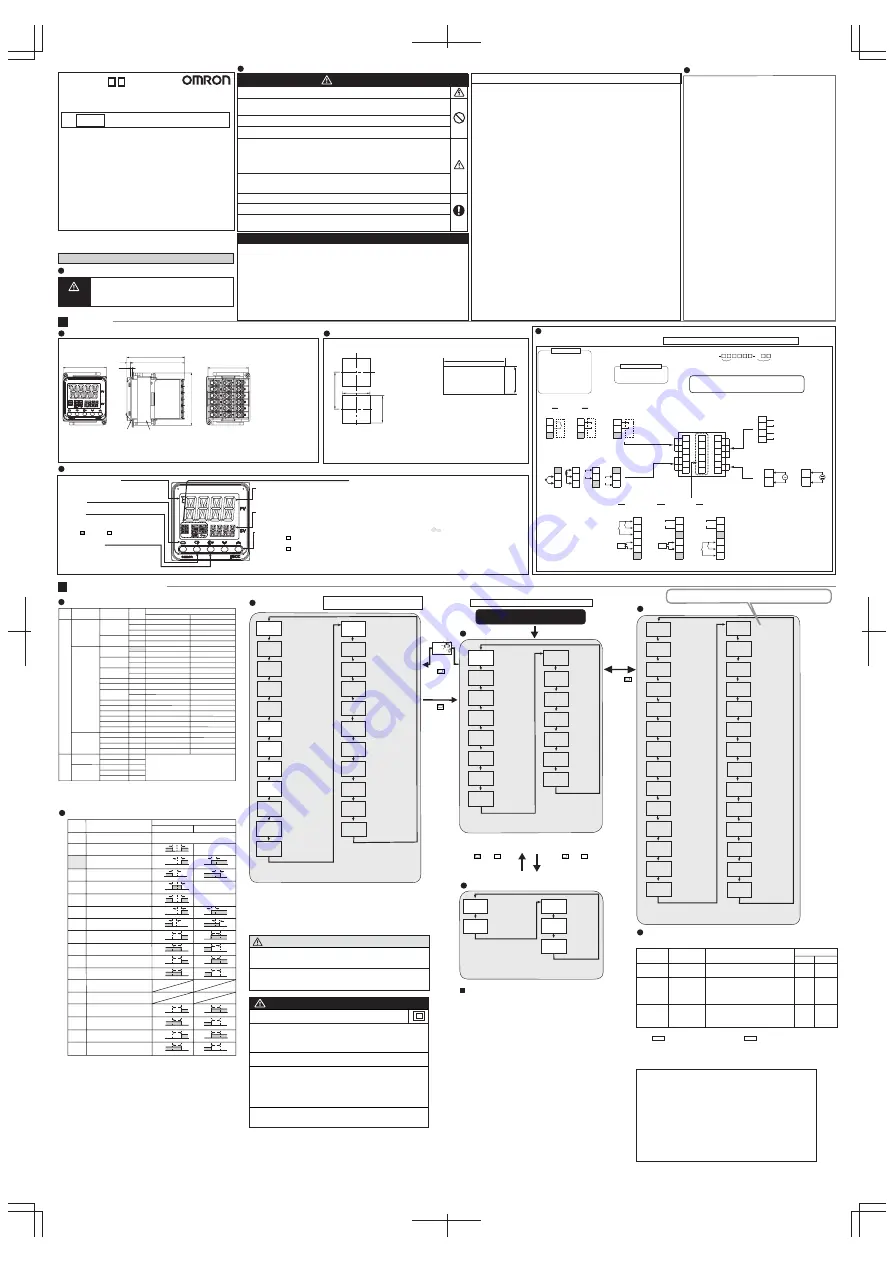
.
ni
m
0
6
45
5
4
+0.6
0
6.
0
+
0
6.
0
+
0
(48 x number of units - 2.5)
+1
0
5
4
Indicates a potentially hazardous situation which, if
not avoided, is likely to result in minor or moderate
injury or property damage. Read this manual
carefully before using the product.
E5CC
-
8
Digital Controller
Be sure to observe the following precautions to prevent operation failure, malfunction, or adverse affects on the
performance and functions of the product. Not doing so may occasionally result in unexpected events.
Use the product within specifications.
(1) The product is designed for indoor use only. Do not use the product outdoors. Do not use or store the product
in any of the following locations.
Places directly subject to heat radiated from heating equipment.
Places subject to splashing liquid or oil atmosphere.
Places subject to direct sunlight.
Places subject to dust or corrosive gas (in particular, sulfide gas and ammonia gas).
Places subject to intense temperature change.
Places subject to icing and condensation.
Places subject to vibration and large shocks.
(2) Use/store within the rated temperature and humidity ranges. Provide forced-cooling if required.
(3) To allow heat to escape, do not block the area around the product.
Do not block the ventilation holes on the product.
(4) Be sure to wire properly with correct polarity of terminals.
(5) Use the specified size of crimped terminals (M3, width 5.8 mm or less) for wiring. To connect bare wires to the
terminal block, use copper braided or solid wires with a gage of AWG24 to AWG18 (equal to cross- sectional
area of 0.205 to 0.8231 mm
2
). (The stripping length is 6 to 8 mm.) Up to two wires of same size and type, or
two crimped terminals can be inserted into a single terminal.
(6) Do not wire the terminals which are not used.
(7) Allow as much space as possible between the controller and devices that generate a powerful high- frequency
or surge. Separate the high-voltage or large-current power lines from other lines, and avoid parallel or
common wiring with the power lines when you are wiring to the terminals.
(8) Use this product within the rated load and power supply.
(9) Make sure that the rated voltage is attained within two seconds of turning ON the power using a switch or relay
contact. If the voltage is applied gradually, the power may not be reset or output malfunctions may occur.
(10) Make sure that the Digital Controller has 30 minutes or more to warm up after turning ON the power before
starting actual control operations to ensure the correct temperature display.
(11) When executing self-tuning, turn the load and the unit ON simultaneously, or turn the load ON before you turn
the controller ON.
(12) A switch or circuit breaker should be provided close to this unit. The switch or circuit breaker should be within
easy reach of the operator, and must be marked as a disconnecting means for this unit.
(14) Design system (control panel, etc) considering the 2 second of delay that the controller’s output to be set after
power ON.
(15) The output will turn OFF when you move to the Initial Setting Level. Take this into consideration when
performing control.
(16) The number of non-volatile memory write operations is limited. Therefore, use RAM write mode when
frequently overwriting data during communications or other operations.
(17) When disassembling the Digital Controller for disposal, use suitable tools.
(18) Do not exceed the communications distance that is given in the specifications and use the specified
communications cable. Refer to the
E5CC/E5EC Digital Controllers User’s Manual
(Cat. No.H174) for the
communications distance and cable specifications.
(19) Do not turn the power supply to the Digital Controller ON or OFF while the USB-Serial Conversion Cable is
connected. The Digital Controller may malfunction.
Precautions for Safe Use
Refer to the
E5CC/E5EC Digital Controllers User’s Manual
(Cat. No. H174)
for detailed application procedures.
INSTRUCTION MANUAL
Thank you for purchasing the OMRON E5CC Digital Controller.
This manual describes the functions, performance, and
application methods needed for optimum use of the product.
Please observe the following items when using the product.
This product is designed for use by qualified personnel with
a knowledge of electrical systems.
Before using the product, thoroughly read and understand
this manual to ensure correct use.
Keep this manual in a safe location so that it is available for
reference whenever required.
OMRON Corporation
©All Rights Reserved
Refer to the
E5CC/E5EC Digital Controllers User’s Manual
(Cat. No.
H174) for information on the Advanced Function Setting Level,
Manual Control Level, and other functions.
Refer to the
E5CC/E5EC Digital Controllers Communications
Manual
(Cat. No. H175) for information on communications.
Power supply voltage
100 to 240 VAC, 50/60 Hz or
24 VAC, 50/60 Hz / 24 VDC
Operating voltage range
85 to 110% of the rated voltage
Power consumption
Option 800:
5.2 VA max. (100 to 240 VAC)
3.1 VA max. (24 VAC)/1.6 W max. (24 VDC)
All other specifications:
6.5 VA max. (100 to 240 VAC)
4.1 VA max. (24 VAC)/2.3 W max. (24 VDC)
Indication accuracy
Thermocouple:
(Ambient temperature: 23°C)
(±0.3 % of indication value or ±1°C,
whichever is greater) ±1 digit max.
Platinum resistance thermometer:
(±0.2 % of indication value or ±0.8°C,
whichever is greater) ±1 digit max.
Analog input:
±0.2 % FS ±1 digit max.
Event input
Output current: approx. 7 mA per contact.
Contact input
ON:1 k k
No-contact input
ON: residual voltage 1.5 V max.,
OFF: leakage current 0.1 mA max.
Control output 1 Relay output :SPST-NO
250VAC, 3A(resistive load)
Electrical life of relay: 100,000 operations
Voltage output (for driving SSR):
12 VDC ±20%, 21 mA
Current output: 4 to 20 mA DC, 0 to 20mA DC
Load: 500
Control method
ON/OFF or 2-PID control
Auxiliary outputs
Relay outputs:SPST-NO, 250 VAC,
3 A (resistive load)
Electrical life of relay: 100,000 operations
Ambient temperature
-10 to 55°C
(Avoid freezing or condensation)
Ambient humidity
25% to 85%
Storage temperature
-25 to 65°C
(Avoid freezing or condensation)
Altitude
Max. 2,000m
Recommended fuse
T2A, 250 VAC, time-lag, low-breaking capacity
Weight
Approx. 120 g (Digital Controller only)
Degree of protection
Front panel: IP66
Rear case: IP20, Terminal section: IP00
Installation environment
Installation category II, pollution
degree 2 (as per IEC61010-1)
Memory protection
Non-volatile memory
(Number of write operations: 1,000,000)
CAUTION
CAUTION
Minor injury due to electric shock may occasionally occur.
Do not touch the terminals while power is being supplied.
Electric shock, fire, or malfunction may occasionally occur. Do not allow metal objects, conductors,
cuttings from installation work, or moisture to enter the Digital Controller, the Setup Tool ports, or
between the pins on the connectors on the Setup Tool cable.
Do not use the product where subject to flammable or explosive gas. Otherwise, minor injury from
explosion may occasionally occur.
Never disassemble, modify, or repair the product or touch any of the internal parts. Minor electric
shock, fire, or malfunction may occasionally occur.
CAUTION - Risk of Fire and Electric Shock
a) This is the product UL listed as Open Type Process Control Equipment. It must be mounted in an enclosure
that does not allow fire to escape externally.
b) More than one disconnect switch may be required to de-energize the equipment before servicing.
c) Signal inputs are SELV, limited energy.
d) Caution: To reduce the risk of fire or electric shock, do not interconnect the outputs of different Class 2 circuits.
If the output relays are used past their life expectancy, contact fusing or burning may occasionally occur.
Always consider the application conditions and use the output relays within their rated load and
electrical life expectancy. The life expectancy of output relays varies considerably with the output load
and switching conditions.
Loose screws may occasionally result in fire. Tighten the terminal screws to the specified torque of 0.43
to 0.58
Set the parameters of the product so that they are suitable for the system being controlled. If they are
not suitable, unexpected operation may occasionally result in property damage or accidents.
A malfunction in the Digital Controller may occasionally make control operations impossible or prevent
alarm outputs, resulting in property damage. To maintain safety in the event of malfunction of the Digital
Controller, take appropriate safety measures, such as installing a monitoring device on a separate line.
EN
Safety Precautions
Key to Warning Symbols
Dimensions
*2: Error shown only for "Process value / Set point". Not shown for other status.
When an error has occurred, the No.1 display shows the error code. Take necessary measure
according to the error code, referring the table below.
If the input value exceeds the display limit (-1999 to 9999), though it is within the control
range,
[[[[
will be displayed under -1999 and
]]]]
above 9999. Under these conditions,
control output and alarm output will operate normally.
Refer to the
E5CC/E5EC Digital Controllers User’s Manual
(Cat. No. H174) for the controllable
ranges.
Check the setting of the Input Type parameter,
check the input wiring, and check for broken or
shorts in the temperature sensor.
Turn the power OFF then back ON again. If the
display remains the same, the controller must be
repaired. If the display is restored to normal, then
a probable cause can be external noise affecting
the control system. Check for external noise.
After the correction of A/D converter error, turn the
power OFF then back ON again. If the display
remains the same, the controller must be repaired.
If the display is restored to normal, then a
probable cause can be external noise affecting the
control system. Check for external noise.
No.1 display
Meaning
A/D converter error
*2
Memory error
Input error
*2
s.err
(S. Err)
e111
(E111)
Action
OFF
Alarm
Control
output
Status at error
OFF
OFF
Operates
as above the
upper limit.
OFF
OFF
e333
(E333)
Error Display (troubleshooting)
Warning Symbols
Installation
Connections
(The applicability of the electric terminals varies with the type of machine.)
Specifications
Other functions
Wiring
Names of Parts on Front Panel
°C / °F : temperature unit
The temperature unit is displayed when the displayed value
is a temperature. Either
C
or
F
is displayed according to
the set value of the temperature unit.
Mode key
Press this key to change the contents of the display.
Press this button for 1 s or longer for reverse scroll.
Press the
key and the
M
key together for at
least 3 seconds to switch to protect level.
Level key
Use this key to change levels:
Shift key (PF key)
The default PF Setting parameter is for shifting the digit.
This is a function key. When it is pressed, the function
set for the PF Setting parameter will operate.
:Protection indicator
Lit when Setting Change Protect is
ON (disables the Up and Down Keys).
MANU: Manual output indicator
Lit when the Auto/Manual Mode is set
to Manual Mode.
Operation Menu
*1: Upper and lower limits can be set for parameters 1, 4 and 5 to
provide for different types of alarm. These are indicated by the
letter "L" and "H".
The default alarm type is "2"
Alarms
OMRON EUROPE B.V.
Wegalaan 67-69, NL-2132 JD Hoofddorp The Netherlands
Phone 31-2356-81-300
FAX 31-2356-81-388
OMRON ELECTRONICS LLC
One Commerce Drive Schaumburg, IL 60173-5302 U.S.A
Phone 1-847-843-7900
FAX 1-847-843-7787
OMRON ASIA PACIFIC PTE. LTD.
No. 438A Alexandra Road # 05-05/08 (Lobby 2),
Alexandra Technopark, Singapore 119967
Phone 65-6835-3011
FAX 65-6835-2711
OMRON Corporation
Shiokoji Horikawa, Shimogyo-ku, Kyoto 600-8530 JAPAN
Operation stopped.
(Control/alarm are both stopped.)
*5
Initial Setting Level
Use the following ranges for scaling: -1999
to 9999, -199.9 to 999.9, -19.99 to 99.99,
-1.999 to 9.999
g
ol
a
n
A
e
p
yt
t
u
p
ni
Current input
Voltage input
Do not connect anything to the terminals that are shaded gray.
Dimensions (mm)
The E5CC is set for a K thermocouple (input type of 5)
by default. If a different sensor is used, an input error (
s.err
) will occur.
Check the setting of the Input Type parameter.
Check the wiring before turning ON the power supply.
*1
*1
*1
Alarm type
Vary with
"L", "H" values
Vary with
"L", "H" values
Vary with
"L", "H" values
No alarm function
Output off
Deviation upper/lower limit
standby sequence ON
Absolute value upper limit
Absolute value lower limit
Absolute value upper limit
standby sequence ON
Absolute value lower limit
standby sequence ON
LBA (only for alarm 1)
Deviation lower limit
standby sequence ON
Deviation upper limit
standby sequence ON
Deviation upper/lower range
Deviation upper limit
Deviation upper/lower limit
Deviation lower limit
Alarm output function
Positive alarm value (X) Negative alarm value (X)
Setting
PV Change Rate Alarm
X
X
ON
OFF
SP
SP
X
ON
OFF
SP
ON
OFF
SP
X
X
ON
OFF
ON
OFF
SP
L H
ON
OFF
SP
X
ON
OFF
SP
X
ON
OFF
SP
X
ON
OFF
0
ON
OFF
X
0
X
ON
OFF
0
X
ON
OFF
0
ON
OFF
X
0
X
ON
OFF
0
X
ON
OFF
0
X
ON
OFF
0
X
ON
OFF
0
X
ON
OFF
0
ON
OFF
X
0
ON
OFF
X
0
ON
OFF
X
0
ON
OFF
X
0
L H
ON
OFF
SP
SP
ON
OFF
X
ON
OFF
X
0
1
0
2
3
4
5
6
7
8
9
SP absolute value upper limit
SP absolute value lower limit
14
15
MV absolute value upper limit
MV absolute value lower limit
16
17
10
11
12
13
ON
OFF
X
0
POWER ON
MV Monitor
(Heating)
*6
o
0.0
MV Monitor
(Cooling)
*6
c-o
0.0
Alarm Value
Lower Limit 1 *4
*6
al1l
0
Alarm Value 2 *4
*6
al-2
0
Alarm Value
Upper Limit 2 *4
*6
al2h
0
Alarm Value
Lower Limit 2 *4
*6
al2l
0
Input Type *3
Scaling Upper Limit
(only when setting
analog input)
Scaling Lower Limit
(only when setting
analog input)
Decimal Point
(only when setting
analog input)
Temperature
Unit
SP Upper Limit
SP Lower Limit
In ON/OFF control =
onof
In 2-PID control =
pid
Standard or Heating/Cooling
Standard control =
stnd
Heating and cooling control =
h-c
Control Period (Heating)
(Unit: Seconds)
*Voltage output (for driving SSR): 2
Alarm 1 Type:
Specified models only
Control Period (Cooling)
(Unit: Seconds)
*Voltage output (for driving SSR): 2
ST (Self-Tuning)
ST ON =
on
ST OFF =
off
Direct/Reverse Operation
In Reverse operation (Heating) =
or-r
In Direct operation (Cooling) =
or-d
*3
*4
*6
*6
*6
*6
*6
*6
*6
*6
*6
in-t
5
in-h
100
in-l
0
dp
0
d-u
c
sl-h
1300
sl-l
-200
cntl
onof
s-hc
stnd
st
on
cp
20
c-cp
20
orev
or-r
alt1
2
*6
Event Input
Assignment 1
*6
ev-1
msp0
Event Input
Assignment 2
*6
ev-2
stop
Event Input
Assignment 3
*6
ev-3
none
Event Input
Assignment 4
*6
ev-4
none
Move to Advanced
Function Setting
Level
*6
amov
0
*6
Alarm 1
Hysteresis
alh1
0.2
Alarm 2
Hysteresis
alh2
0.2
Alarm 2 Type:
Specified models only
alt2
2
*6
at
off
Heater Current 1 Value
Monitor (unit: A) *7
*6
ct1
0.0
Communications Writing
*6
cmwt
off
*6
Heater Burnout Detection 1
(unit: A) *7
hb1
0.0
MV Upper Limit
*6
ol-h
100.0
Manual Reset Value
Clears the offset
during P or PD control.
*6
of-r
50.0
SP Ramp Set Value
*6
sprt
off
Hysteresis (Cooling)
*6
chys
1.0
PV
Input Shift
*6
ins
0.0
Leakage Current 1 Value
Monitor (unit: A) *7
*6
lcr1
0.0
Integral Time
(Unit: secs)
*6
i
233
Derivative Time
(Unit: secs)
*6
d
40
MV Lower Limit
*6
ol-l
0.0
HS Alarm 1
(unit: A) *7
*6
hs1
5
0.0
SP 0
*6
sp-0
0
SP 1
*6
sp-1
0
SP 3
*6
sp-3
0
SP 4
*6
sp-4
0
SP 5
*6
sp-5
0
SP 6
*6
sp-6
0
SP 7
*6
sp-7
0
SP 2
*6
sp-2
0
25
0
Process Value/Set Point
s.err
is displayed when
connected sensor is
different from input type.
AT Execute / Cancel
100%AT Execute
at-2
40%AT Execute
at-1
Dead Band
*6
c-db
0.0
Hysteresis (Heating)
*6
hys
1.0
*6
Control Output 1
Signal
o1st
4-20
Proportional
Band
*6
p
8.0
Integral Time
(Cooling)
(unit: s)
*6
c-i
233
Derivative Time
(Cooling)
(unit: s)
*6
c-d
40
Proportional Band
(Cooling)
*6
c-p
8.0
4 to 20mA
0 to 20mA
1 to 5V
0 to 5V
0 to 10V
25
26
27
28
29
Setting range
Input type
Input
Pt100
JPt100
Thermocouple
Infrared
Thermosensor
ES1B
K
J
T
E
L
U
N
R
S
B
W
PL
II
Setting
10 to 70°C
60 to 120°C
115 to 165°C
140 to 260°C
0
1
2
3
4
5
6
7
8
9
10
11
12
13
14
15
16
17
18
19
20
21
22
23
24
17
18
12
15
16
1
2
13
14
3
11
4
6
7
8
9
10
5
Operation indicators
SUB1: Auxiliary output 1 indicator
SUB2: Auxiliary output 2 indicator
OUT1: Control output 1 indicator
6
4
5
6
5
6
Pt
+
mA
+
5
4
*2 Sensor Temperature/Analog Input
V
5
V
6
+
4
TC
4
I
(no polarity)
11
12
*4 Input Power Supply
11
12
100 to 240 VAC
24 VAC/DC
(64)
8
5
60
4
1
44.8
u
44.8
5. Options
1. Control outputs
10
7
8
9
*3 Auxiliary Outputs
Auxiliary outputs 1 and 2
Auxiliary output 1
Auxiliary output 2
16
17
18
13
14
15
13
14
15
18
16
804
Communications (RS-485)
and event inputs 3 and 4
13
14
15
16
*5 Options
801
Event inputs 1 and 2,
and CT1
17
17
18
802
Communications
(RS-485) and CT1
EV1
EV2
EV3
EV4
CT1
CT1
B(+)
A(
)
RS-485
B(+)
A(
)
RS-485
+
3
1
2
3
1
2
One linear
current output
One relay
output
3
*1 Control Outputs 1
1
2
One voltage output
+
RX
QX
CX
Sold Separately
*Terminal cover (E53-COV23)
*USB-Serial Conversion Cable
(E58-CIFQ2)
In the pack:
*Main unit
*Instruction manual
*Watertight packing (Y92S-P8):
c
*Adapter (Y92F-49):
d
* Do not remove the terminal block. Doing so may result in failure or malfunction.
* A Setup Tool port is provided on the upper of the product. Use this port to connect a personal computer to the product when using
the Setup Tool. E58-CIFQ2 USB-Serial Conversion Cable is required to connect the personal computer to the product. (Do not use
the product with the USB-Serial Conversion Cable left permanently connected.)
Refer to the instruction manual provided with the USB-Serial Conversion Cable for details on connection methods.
Relay output
250 VAC, 3 A (resistive load)
Voltage output (for driving SSR)
12 VDC, 21 mA
Current output
0 to 20 mA DC
4 to 20 mA DC
Control output 1
No.1 display
Process value or set data type
No.2 display
Set point, set data read-out value or changed input
value
Up and Down keys
Each press of
U
key increments or advances the
values displayed on the No.2 display.
Each press of
D
key decrements or returns the
values displayed on the No.2 display.
TUNE:
Flashing during self-tuning.
Lit during auto-tuning.
STOP: Control stopped indicator
Lit when event input or “Run/Stop” is stopped during
operation.
During control stop, functions other than control output
are valid.
CMW: Communications writing
enabled/disabled indicator
Lit when communications writing is enabled and not lit
when it is disabled.
Relay outputs
250 VAC
,
3 A (resistive load)
Auxiliary outputs 1 and 2
E5CC
Input Type
-200 to 850
-199.9 to 500.0
0.0 to 100.0
-199.9 to 500.0
0.0 to 100.0
-200 to 1300
-20.0 to 500.0
-100 to 850
-20.0 to 400.0
-200 to 400
-199.9 to 400.0
-200 to 600
-100 to 850
-200 to 400
-199.9 to 400.0
-200 to 1300
0 to 1700
0 to 1700
100 to 1800
0 to 2300
0 to 1300
0 to 90
0 to 120
0 to 165
0 to 260
-300 to 1500
-199.9 to 900.0
0.0 to 210.0
-199.9 to 900.0
0.0 to 210.0
-300 to 2300
0.0 to 900.0
-100 to 1500
0.0 to 750.0
-300 to 700
-199.9 to 700.0
-300 to 1100
-100 to 1500
-300 to 700
-199.9 to 700.0
-300 to 2300
0 to 3000
0 to 3000
300 to 3200
0 to 3200
0 to 2300
0 to 190
0 to 240
0 to 320
0 to 500
Platinum
resistance
thermometer
st
u
p
ni
er
ut
ar
e
p
m
e
T
*The default is“5”.
*
s.err
will be displayed when a platinum resistance thermometer is mistakenly connected
while input type is not set for it. To clear the
s.err
display, correct the wiring and cycle the
power supply.
°C=
c
°F=
f
*3
*4
Initial setting level enables users to specify their preferred
operating conditions (input type, alarm type, control method, etc.)
*3: Refer to the adjoining tables for details of input types and alarm types.
*4: Applicable only to models with alarm functions.
*5: Operation is stopped when moved to the initial setting level.
(control/alarm are both stopped.)
*6:
The grayed-out setting items are not displayed for some models and
some settings of other setting items.
*7: Applicable only to models with heater burnout functions.
Hold
down
for at least
1 second
(No.1 display flashes,
then the control stops.)
Hold
down
for at least
3 seconds
Operation Level
Set Point During
SP Ramp
*6
sp-m
0
Heater Current 1
Value Monitor
(unit: A)
*7
*6
ct1
0.0
Multi-SP Set Point
Selection
*6
m-sp
0
Auto/Manual Switch
PID 1 control only.
Auto/Manual Select
Addition.
*6
a-m
Leakage Current 1
Value Monitor
(unit: A)
*7
*6
lcr1
0.0
RUN/STOP
*6
r-s
run
Alarm Value 1 *4
*6
al-1
0
Alarm Value
Upper Limit 1 *4
*6
al1h
0
When control start =
run
When control stop =
stop
Operation level should normally be used during operations.
Hold
and
M
keys
down for at least
1 second
Hold
and
M
keys
down for at least
3 seconds
Press
(less than
1 second)
Adjustment Level
Only the value set to the
ins
: Temperature Input Shift parameter is applied to the entire temperature input range.
When the process value is 200°C, the process value is treated as 201.2°C after input shift if the input shift value
is set to 1.2°C. The process value is treated as 198.8°C after input shift if the input shift value is set to -1.2°C.
Adjustment level is for entering set values and shift values for control.
M
M
M
M
M
M
M
M
M
M
M
M
M
M
M
M
M
M
M
M
M
M
M
M
M
M
M
M
M
M
M
M
M
M
M
M
M
M
M
M
M
M
M
M
M
M
M
M
M
M
M
M
M
M
M
M
M
M
M
M
M
M
M
M
M
* When complying with EMC standards, the line connecting the sensor must be 30 m or less.
If the cable length exceeds 30 m, compliance with EMC standards will not be possible.
Individual mounting (mm)
Side-by-side mounting (mm)
!!$&anel (1 to 5 mm thickness). Insert the
mounting brackets (supplied) into the fixing slots located on the top and bottom of the rear
case.
Tighten the two mounting screws on the top and bottom of the adapter to keep them
balanced, and finally tighten them to a torque of between 0.29 and 0.39 N·m.
';$$ <that the ambient temperature does
not exceed the specified limit.
Waterproofing is impossible
with side-by-side
installation. When
waterproofing is required, fit
watertight packing on the
backside of front panel.
°C
°F
C
Q
R
48
u
48
c
d
Solderless terminal size
M3
OUT1
OUT1
OUT1
A
B
B
Conformance to EN/IEC Standards
This is a class A product.
In residential areas it may cause radio interference, in which case the user
may be required to take adequate measures to reduce interference.
Ͳ͑匏͑匶匶͙͑櫋怺殯͑愯暧皻柦匶沖沲͚͑
決͑匶匶垚͑櫋怺殯͙Ͳ͑匏͚͑洊沖砒洇穯匶匶嵢昢͑砖廪沖嬖垚͑斲殯沖垚͑決͑洖汊͑
渂汞穞柢匶͑愚岂彶͑͝儆洛歾汞滆櫳櫖昢͑斲殯穞垚͑冉汊͑徯洇求嵢͑穯城埪͑͟
L H
ON
OFF
SP
(13) Wipe off any dirt from the Digital Controller with a soft dry cloth. Never use thinners, benzine, alcohol, or any
cleaners that contain these or other organic solvents. Deformation or discoloration may occur.
Operation / Adjustment Protect
Restricts displaying and
modifying menu items in
Operation, Adjustment,
and Manual Control Levels.
oapt
0
Changed
Parameters Only
Initial Setting / Communication Protect
Restricts movement to the
Initial Setting, Communications
Setting, and Advanced Function
Setting Levels.
icpt
1
Setting Change Protect
Restricts changes to
settings by operating
the front panel keys.
wtpt
off
pfpt
off
PF Key Protect
Restricts PF key
operation.
Protect Level
Restricts which settings can be displayed or changed, and
restricts change by key operation.
M
M
M
M
M
M
chgp
off
8
*6
Suitability for Use
Omron Companies shall not be responsible for conformity with any standards, codes or regulations which
apply to the combination of the Product in the Buyer’s application or use of the Product.
At Buyer’s request, Omron will provide applicable third party certification documents identifying ratings and
limitations of use which apply to the Product. This information by itself is not sufficient for a complete
determination of the suitability of the Product in combination with the end product, machine, system, or
other application or use. Buyer shall be solely responsible for determining appropriateness of the particular
product with respect to Buyer’s application, product or system. Buyer shall take application responsibility in
all cases.
NEVER USE THE PRODUCT FOR AN APPLICATION INVOLVING SERIOUS RISK TO LIFE OR
PROPERTY WITHOUT ENSURING THAT THE SYSTEM AS A WHOLE HAS BEEN DESIGNED TO
ADDRESS THE RISKS, AND THAT THE OMRON PRODUCT(S) IS PROPERLY RATED AND INSTALLED
FOR THE INTENDED USE WITHIN THE OVERALL EQUIPMENT OR SYSTEM.
(20) The maximum terminal temperature is 75°C.
Temporary overvoltage
Short term: 1200 V+
(
power supply voltage)
Long term: 250 V+ (power supply voltage)
Conformance to Safety Standard
Reinforced insulation is provided between input power
supply, relay outputs, and between other terminals.
Do not allow temporary overvoltages on the primary circuit to exceed
the following values.
Check the power supply voltage to the Digital Controller.
Short-term overvoltage: 1,200 V + (Power supply voltage)
Long-term overvoltage: 250 V + (Power supply voltage)
Always externally connect the recommended fuse that is specified
in the Instruction Manual before you use the Digital Controller.
Analog Input
If you input an analog voltage or current, set the Input Type
parameter to the correct input type.
Do not use the Digital Controller to measure a circuit with
Measurement Category II, III, or IV.
Do not use the Digital Controller to measure an energized circuit to
which a voltage that exceeds 30 Vms or 60 VDC is applied.
The protection provided by the Digital Controller may be impaired if the
Digital Controller is used in a manner that is not specified by the
manufacturer.