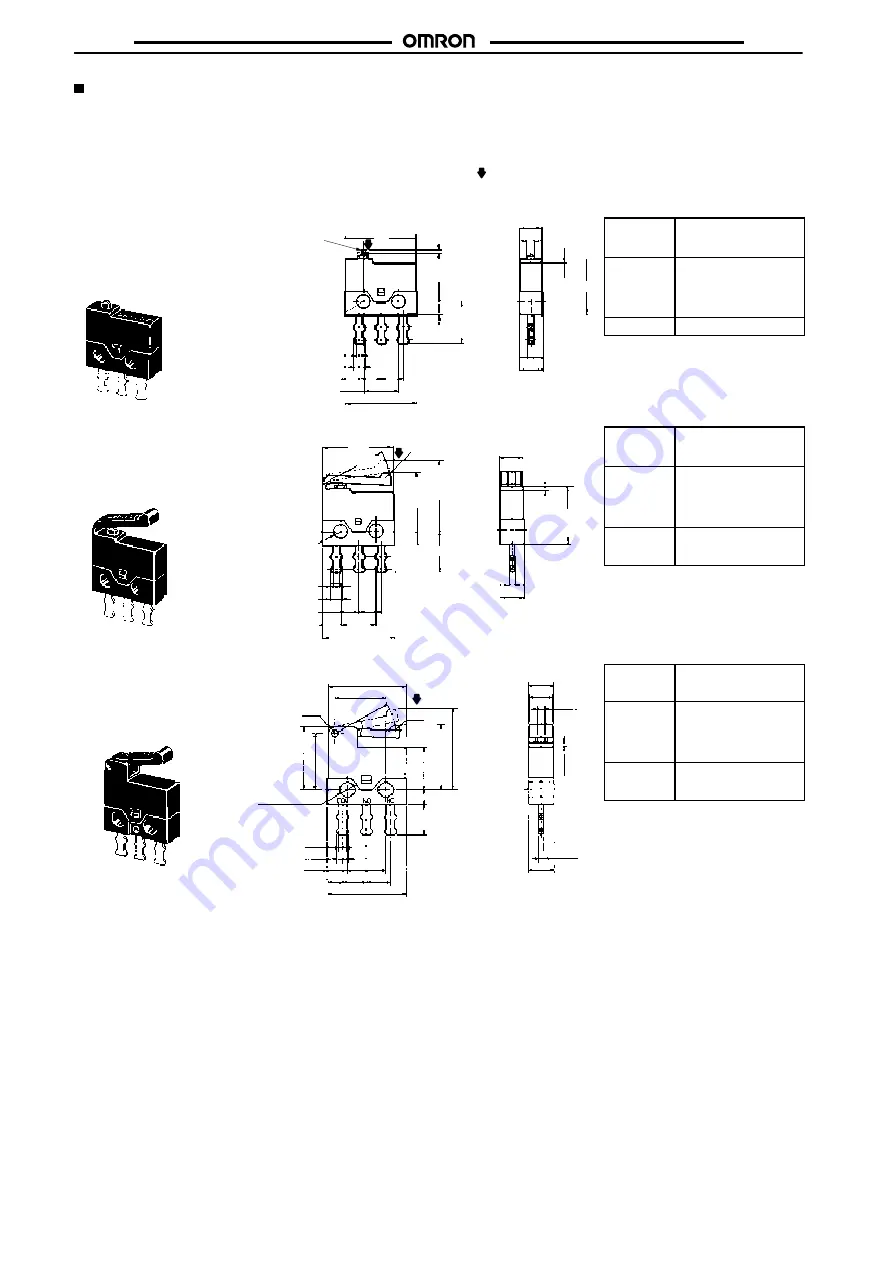
D2MQ
D2MQ
212
Dimensions and Operating Characteristics
Note:
1. All units are in millimeters unless otherwise indicated.
2. Unless otherwise specified, a tolerance of 0.15 mm applies to all dimensions.
3. The following illustrations are for the straight terminal models. Those for the left-angled terminals and right-angled terminals are
different from straight terminal models in terminal size only. Refer to Terminals on page 211 for these terminals.
4. The operating characteristics are for operation in the A direction ( ).
OF max.
1.18 N {120 gf}
RF min.
{
g }
0.19 N {20 gf}
PT max.
0.4 mm
OT min.
0.1 mm
MD max.
0.1 mm
OP
5.7
±
0.2 mm
OF max.
0.59 N {60 gf}
RF min.
{
g }
0.08 N {8 gf}
PT max.
2.4 mm
OT min.
0.3 mm
MD max.
0.7 mm
FP max.
9.6 mm
OP
6.7
±
0.5 mm
OF max.
0.39 N {40 gf}
RF min.
{
g }
0.04 N {4 gf}
PT max.
2.1 mm
OT min.
0.3 mm
MD max.
0.7 mm
FP max.
8.7 mm
OP
7.1
±
0.5 mm
Pin Plunger Models
D2MQ-1 (Straight Terminals)
D2MQ-1-TL (Left-angled terminals)
D2MQ-1-TR (Right-angled terminals)
D2MQ-1-105 (Straight Terminals)
Two, 1.6
+0.1
0
dia.
0.8
8.1
Plastic pin plunger
PT
OP
1.6
5.0
0.8
1.3
1.6
2.1
8.2
2.5 2.5
4
±
0.05
2.6
0.45
6.5
0.6
2.7
A
0.6R (plastic
leaf lever)
FP
OP
1.6
5.0
Two, 1.6
+0.1
0
dia.
0.8
1.3
1.6
2.1
8.2
2.5 2.5
4
±
0.05
2.6
0.45
6.5
0.6
2.7
8.1
7.7R
Leaf Lever Models
D2MQ-1L (Straight Terminals)
D2MQ-1L-TL (Left-angled terminals)
D2MQ-1L-TR (Right-angled terminals)
D2MQ-1L-105 (Straight Terminals)
A
Hinge Leaf Lever Models
D2MQ-4L-1
D2MQ-4L-105-1
D2MQ-4L-1-L
D2MQ-4L-105-1-L
D2MQ-4L-1-R
D2MQ-4L-105-1-R
8.1
5.35
±
0.1
0.5R
6.3R
0.7R
6.6
5.9
OP
FP
Two, 1.6 dia.
+0.1
0
0.8
1.3
3.1 (straight terminals)
1.6
4.45
0.45
2.6
2.4
0.8
0.6
2.7
8.2
2.5
2.5
1.6
2.1
4.0
±
0.05
A