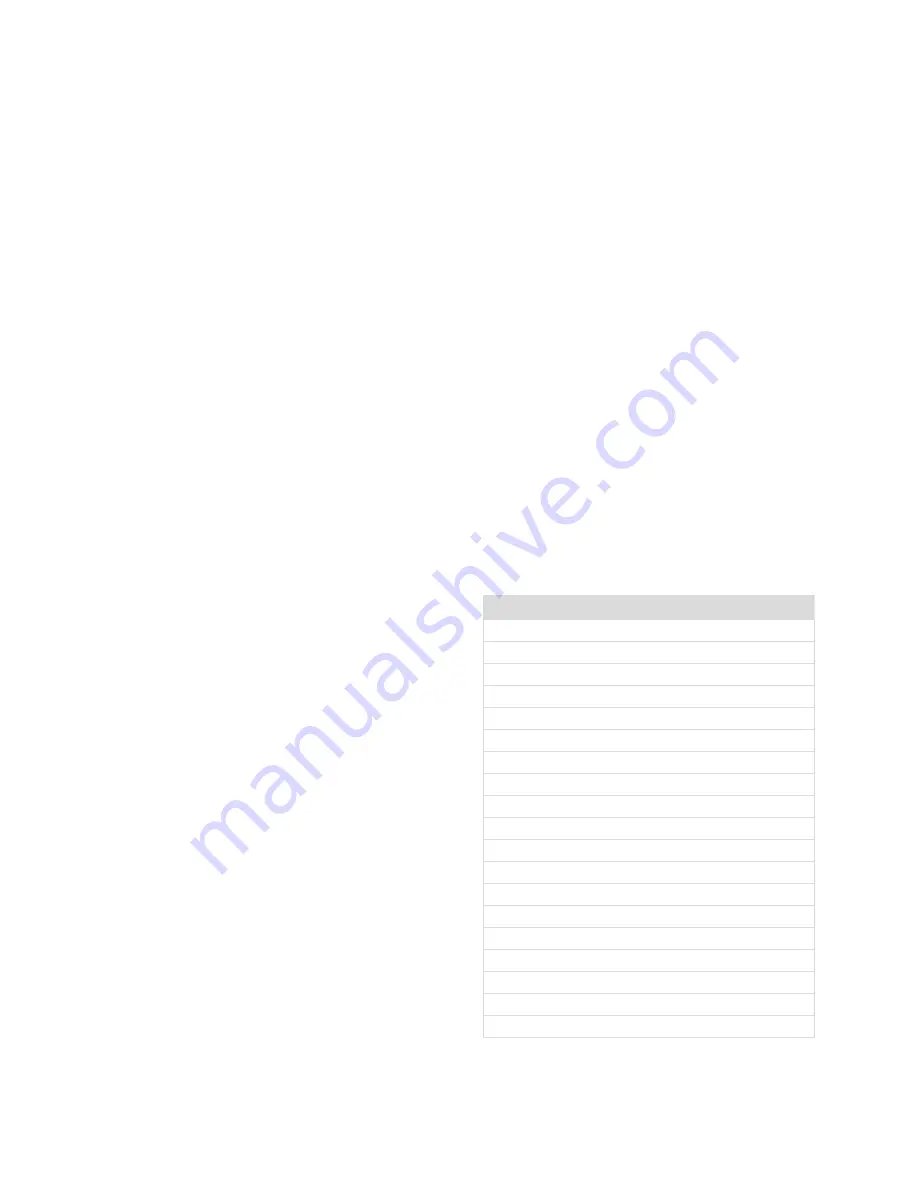
(Fig 5) Mechanical Dimensions
Applications
The Model 760 flame detector is designed for fire detection
applications where sudden fires from hydrocarbon and specified non-
hydrocarbon fuels, may occur . This detector is not recommended for
detection of smoldering materials .
The following is a partial list of materials which when burned, can emit
infrared radiation in the wavelengths common to the detection bands
of the 760 . Response times and detection distances will vary . Contact
a Firefly AB applications engineer for assistance:
Hydrocarbon:
• Petroleum based materials such as liquid fuels, solvents, gases, or
solid compounds
• Wood products
Non-Hydrocarbon:
• Hydrogen, silane, hydrazine
The rugged, weatherproof construction and the operating
temperature range of the detectors will accommodate a variety of
indoor and outdoor applications .
All installations should comply with local fire codes and regulations .
Do not proceed with the installation if you do not understand the
installation procedure or operation of the detectors . Firefly AB
applications engineers are available to assist you .
Installation
To ensure trouble-free operation and reliable fire protection, follow
these installation guidelines:
1 . Locate the Detector(s) in an area where they will have an
unobstructed view of the area to be protected . The detector(s) must
be accessible for periodic cleaning . Failure to maintain clean sensor
windows and self-test optics will impair the performance of the
detector .
2 . Separate the base from the housing by removing the four M8 X
1 .25 cap screws . This will require a 6mm hex key . Store the housing
assembly, containing the electronics, in a clean and dry environment
while installing the base .
3 . Mount the detector base to a previously installed swivel mount
or other appropriate support structure so that the detector has an
unobstructed view of the area to be protected . Position the base such
that the conduit opening faces down . It will be necessary to seal the
conduit within 18 inches of the fire detector enclosure . This will insure
that water and airborne moisture do not enter the detector housing
through the conduit . Provide conduit drains as necessary to prevent
moisture from collecting inside the conduit .
4 . Determine the critical areas where fires are most likely to occur . Use
these areas as focal points for aiming the detectors . The detectors
have a conical field-of-vision as shown earlier in Figures 1 and 2 .
The type of fuel and the size of the fire will determine the range of
detection . Aim the detector at a point equal to or below horizontal so
that water, dust and dirt will not accumulate on the optical surfaces
of the detector . As a general rule, mount the detector so that it will
view the base of the area to be protected . The aiming of the detectors
becomes increasingly critical the greater the detection distance
becomes . There should be few if any obstructions between the
detector and the area to be protected .
5 . Complete the installation by wiring the detector according to the
wiring diagram located inside the rear cover . Before assembling the
detector housing to the base, verify that the terminal block assembly is
plugged in all the way and is located at the top . Insure that the wires
are arranged so as not to interfere with the main electronics module .
If a Torque wrench is available, it is recommended that the four cap
screws be tightened to a value of 35 to 40 in-lbs . (3 .95 to 4 .52 NM) .
Note: The electronics module contains no re-useable parts . It should
never be removed from the housing assembly . This will result in the
voiding of the warranty .
6 . Use a 20 to 30 Vdc regulated and filtered power supply, with a ripple
not exceeding 1 percent . The detectors should be protected from
induced and transient voltages as well as radio frequency interference
(RFI) . To ensure compliance to CE requirements, a dedicated conduit is
highly recommended for the detector wiring . Connect every detector
base to earth ground via an independent wire . Earth ground and
-24 VDC RTN should be isolated and not connected anywhere in the
installation .
Electronics
User Selectable Factory Settings
The electronic module has been factory configured to provide the user
with the following:
Time Delay:
3 Seconds (fire)
35 Seconds (Warning)
Sensitivity:
Normal
Relays:
Fire: Normally Open, Latching .
Fault: Normally Open, Non-latching (Relay is failsafe,
it closes upon application of power to
detector and will clear after a successful test) .
Optical Self-Test: Automatic
0 to 20 mA:
“OFF”
RS485:
“OFF” MODBUS RTU
User Selectable Interface (USI) Options
Refer to Figure 8 for locations of User Selectable Interface Options .
Figure 7 provides the user with a quick reference of switch setting
options for the various models . The text following these figures
describes in more detail the function of each switch setting .
SPST dip switch (S1) located on rear I/O board
Option
Off
On
Automatic & Manual Test Activated
1, 2
No Test Feature
1, 2
Manual Test Only
2
1
Automatic Test Only*
1
2
Sensitivity — Long Distance
3, 4
— Enhanced
3
4
— Normal
4
3
— (Reserved)
3, 4
Warning Alarm5
5
No Warning Alarm*
5
Fire Output Latching*
6
Fire Output Non-latching
6
0 to 20 mA
7
No 0 to 20 mA*
7
RS485 MODBUS RTU
8
No RS485 MODBUS RTU*
8
Program
9
No Program*
9
*Denotes factory settings for auto test units only
(Fig 7) Switch Options For the User Selectable Interface
7
©Firefly AB (Oktober 2016)