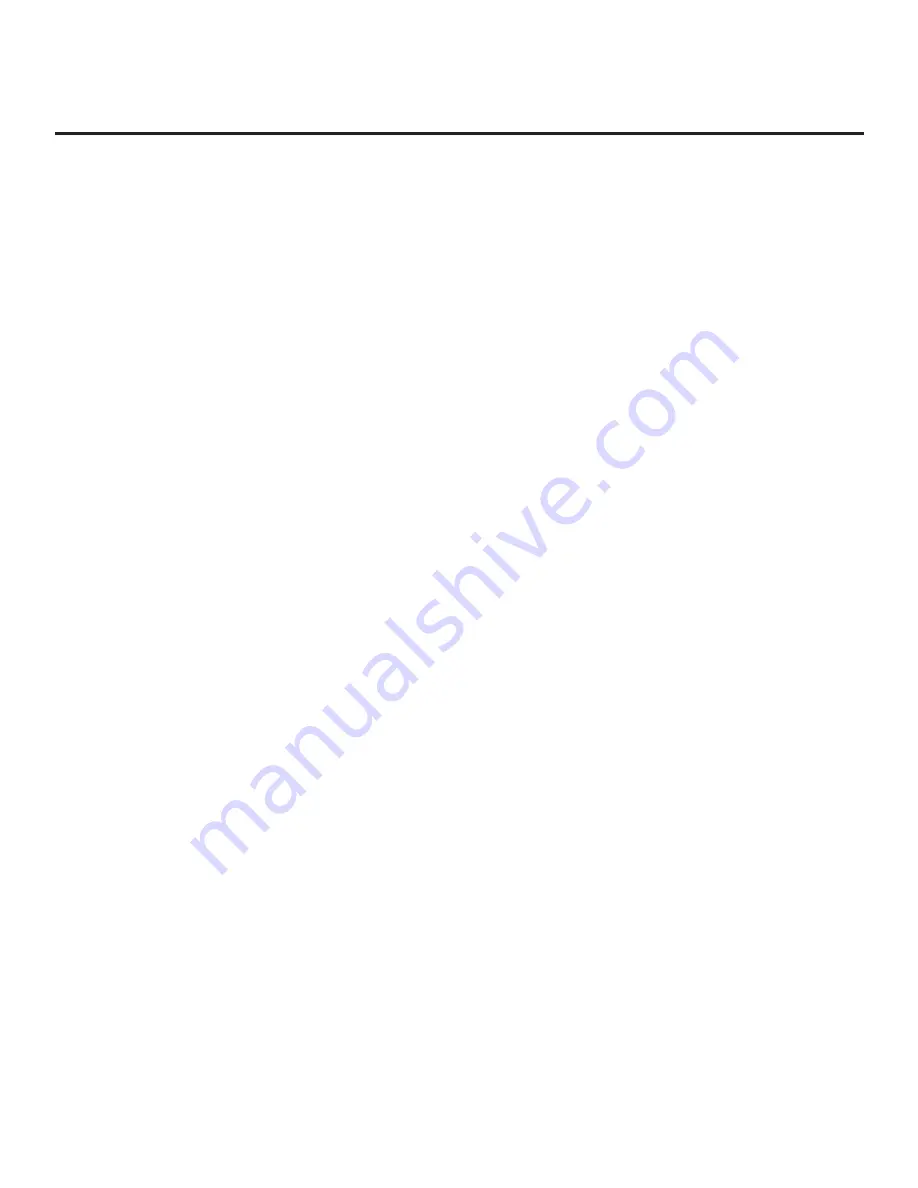
Page 34
OMNI by EconoHeat
Troubleshooting
NO HEAT:
• Check burner power switch and make sure power is available to the whole control system.
• If included in system, check low-water cutoff and/or manual reset high limit.
• Check room thermostat(s) and zone valves or pump relays (if used).
• Make sure there is oil in tank.
• Inquire if reset button on burner oil primary control has been tripped. If reset button continues
to trip then
DO NOT ATTEMPT TO START BURNER
. Open burner door by disconnecting the
plug-in lead and remove the four hex head bolts. Examine the combustion chamber for
unburned oil and oil vapor. If present, clean up oil. With burner door open check cad
cell for soot or dirt deposits, check nozzle and if clogged, replace with nozzle of identical
make and style. Check electrodes for proper gap and for soot or oil deposits. Also check
porcelains for cracks. Close burner door and re-connect electric cord. Press reset button
while watching through the observation port. If burner fires immediately and flame looks
good, cycle several times. If burner does not fire immediately, or if it fires but flame looks
ragged and/or smoky, shut burner down and check the fuel delivery system. The problem
may be air in the intake line so tighten all fittings and tighten the unused intake port plug.
Also check the filter cover and gasket. Also check the pump filter and clean it with a brush
and fuel oil or kerosene if it looks dirty.
INADEQUATE HEAT:
• Check thermostat and heat anticipatory setting. A wrong setting can cause short cycling
and inadequate heating.
• Check to see if the distribution system is air-bound. If pump and boiler are running and the
pipe connection to the boiler supply port is hot, check the pipe temperature at the inlet to
the first radiator. If it is cool or only lukewarm, then the problem is lack of circulation. Look
for air in the system, a valve partially closed, a zone valve failed in the closed position, a
pump failure. The most common fault is air in the system.
RELIEF VALVE LEAKS CONSTANTLY:
• Check system pressure. With system hot, pressure should be in the 20 psi to 25 psi range,
not to exceed 25 psi. With system cold, pressure should be in the 12-14 psi range. If pressure
is over these ranges, then suspect the pressure reducing fill valve or the expansion tank.
A diaphragm tank may be too small, may have a ruptured diaphragm (this would cause
a very sharp rise in pressure as system water heats up and a sudden opening of the relief
valve) or may be over-pressurized. A closed type expansion tank may be undersized, may
be improperly piped to the boiler, may be water logged.
• Relief valve may be defective, or it may have foreign material lodged on the seat.