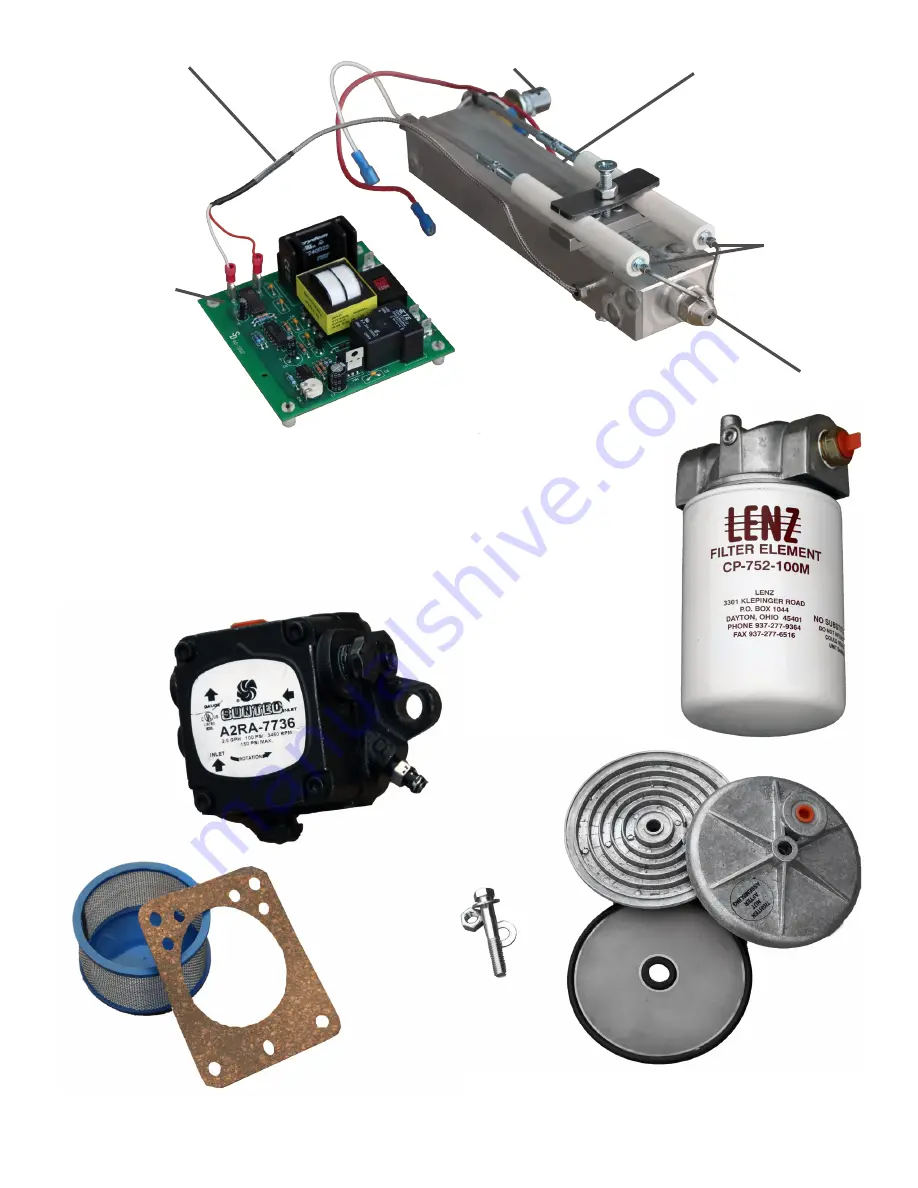
Page 38
OMNI by EconoHeat
Pre Heater Oil Block
Pre-Heater
Control Card
Electrodes
Nozzle
Thermocouple
Figure 39 –
Pre-Heater Block Detail (Removed From Burner for Clarity)
Snap Switch
Figure 41 –
Oil Filter (Spin-On Filter above,
Pancake Style Filter below)
Remove 4 bolts for access to strainer filter.
CAUTION:
must be careful not to destroy the
inner gasket during removal of the housing.
Figure 40 –
Pump Strainer