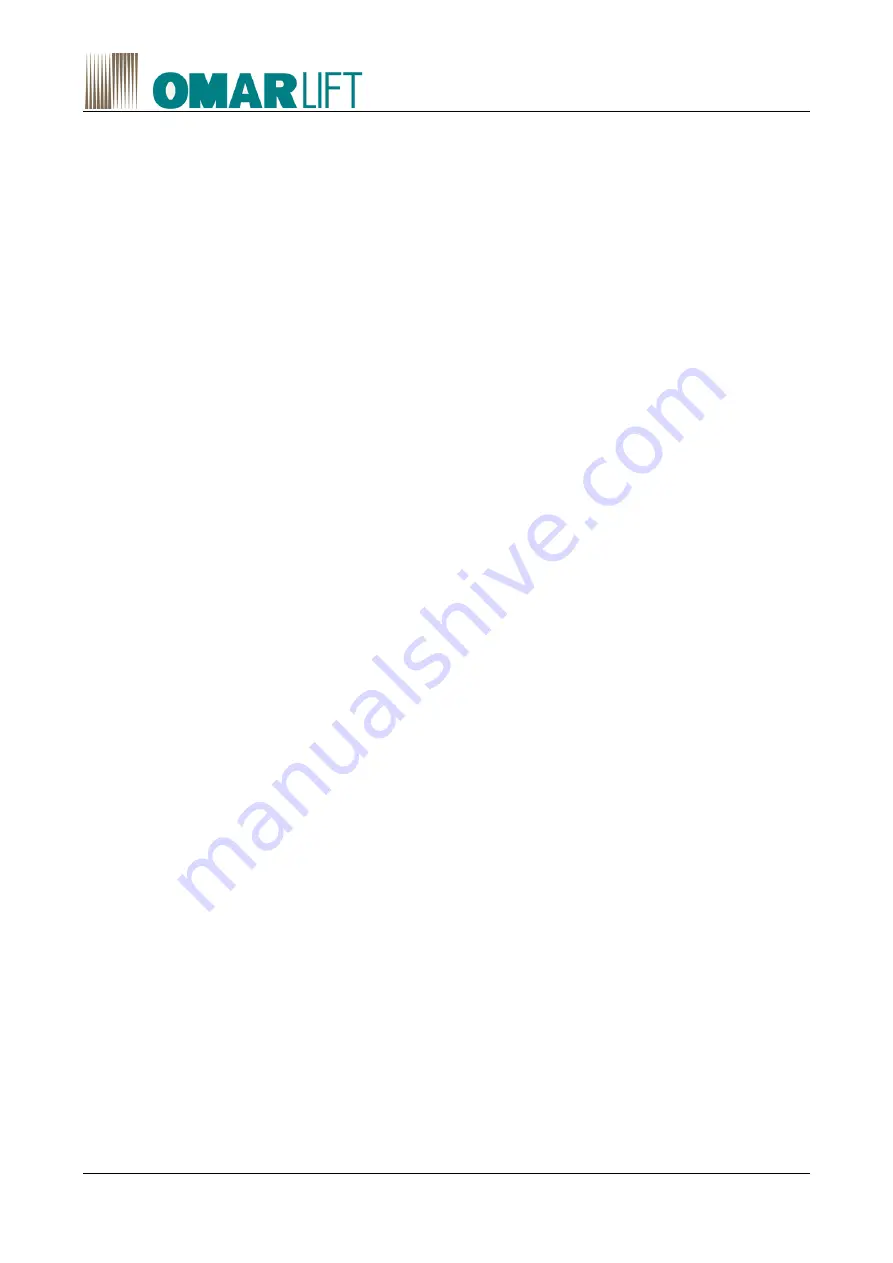
D860MGB rev04
17/32
6.5
CHECK OF THE RUPTURE VALVE INTERVENTION
Be sure that the rupture valve has already been adjusted. If necessary, regulate it according to the handbook
for the adjusting operations or the instruction reported.
The down travel intervention test has to be carried out when the car has been loaded with the nominal load
uniformly distributed according to the instructions reported in paragraph 7.2 "TEST AND WORKING OF THE
RUPTURE VALVE".
6.6
CHECK OF THE INSTALLATION AT TWICE THE STATIC PRESSURE
This check has to be carried out only after the check of the rupture valve intervention and when the oil
temperature is constant.
The oil has not to be hot: the test has to be carried out only when the oil temperature is the same as the
room temperature (please note that in a close circuit, the temperature variation of 1°C can cause a pressure
variation of 9 bar):
-
If necessary, determine the max. static pressure loading the car with the nominal load.
-
Take the piston to upper end position with the main motor until the adjusting pressure is reached and
stop in this position.
-
Increase the pressure slowly with the hand pump until double the max. static pressure.
-
Check pressure fall and losses within 5 minutes, taking into account the possible effects due to the
oil temperature variation. If necessary, repeat the test, re-charging the pressure for 2/3 times with the
hand pump, controlling that pressure does not decrease by 5/6 bar during the first 4/5 minutes. If
needed, read paragraph 10.10. “Periodical recommended maintenance sheet”.
-
When the test has finished, take back the pressure to the value of the static pressure, activating the
emergency button manually and control visually the integrity of the hydraulic system.
6.7
CHECK OF THE ROD COUNTER-PRESSURE AND HAND WORKING
-
For indirect acting installations 2:1, check that, when the car is blocked on the proper parachutes or
lays on its dampers, by activating the red emergency button, the rod does not go down making the
ropes loosen. If necessary, screw the screw n. 3 until it stops.
-
For any kind of installation, check that, when the car is free to go down, it goes down regularly at a
reduced speed when the emergency button is pushed.
6.8
CHECK AND ADJUSTING OF THE HAND PUMP
When the main shut-off valve is closed, activating the hand pump, the pressure on the manometer has to
increase up to the adjusting value.
The safety valve of the hand pump has to be adjusted at 2,3 times the static pressure of the installation with
full load.
The regulation screw of the hand pump is on the left of the lever. If necessary, see instructions at point 8.3.3
for the regulation.
6.9
NOISE
The noise of OmarLift pump units is normally very low, especially during transistors (start / slowdown
example).
With average working conditions, when oil temperature is at 30/40°C and pressure at 25/30 bar, noise does
not normally exceed the following values:
•
pump unit up to 210 l/min: 56÷58dBA
Anyway some external causes can determine an increase in the noise transmission of the installation: in fact
the noise is sometimes transmitted or even expanded by the building walls or by the connecting pipes, thus
reaching the lift space or the rooms next to it. When it happens it is necessary to operate as follows:
1) Use some thick rubber to isolate the connecting pipes from collars used to fix the pipes to the walls.