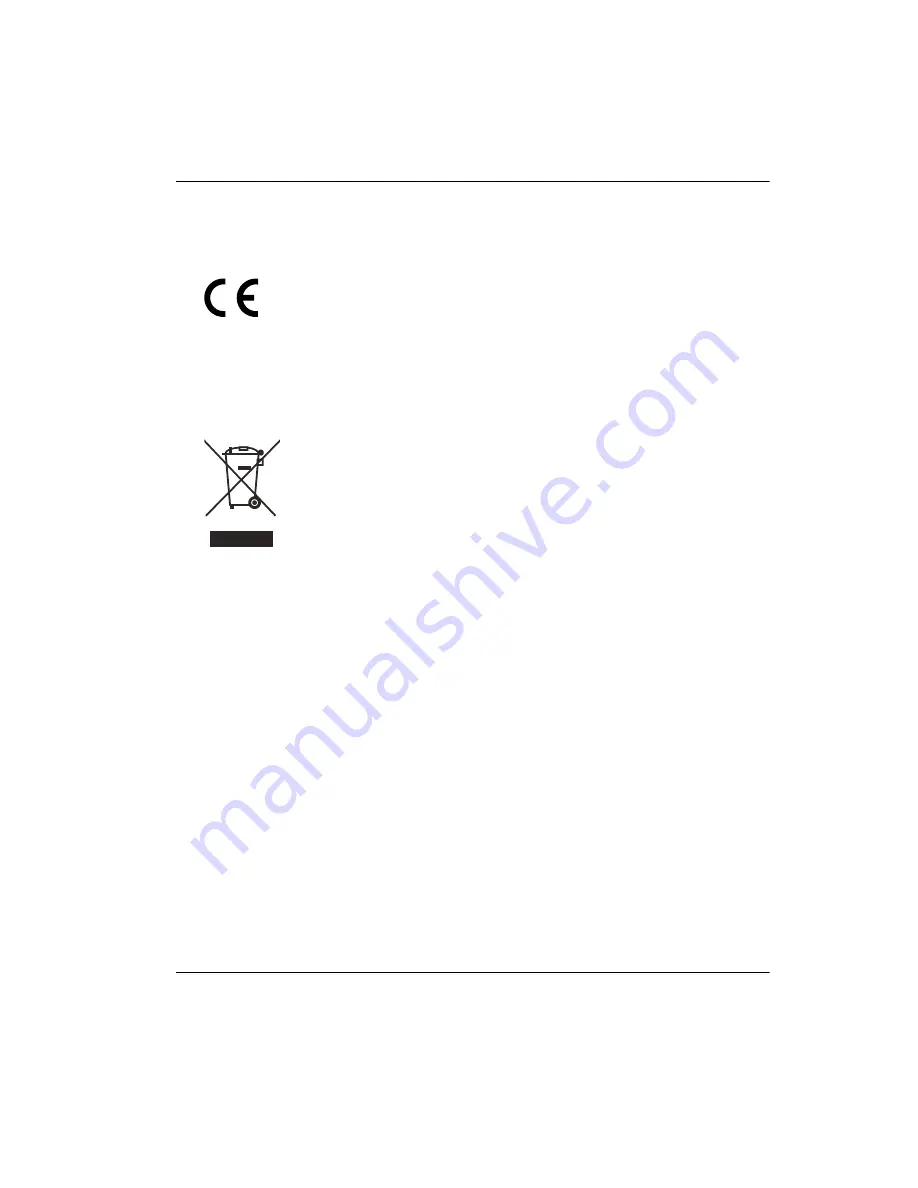
DMTA034-01EN, Rev. B, March 2014
Important Information — Please Read Before Use
11
CE (European Community)
WEEE Directive
EMC Directive Compliance
This equipment generates and uses radio-frequency energy and, if not installed and
used properly (that is, in strict accordance with the manufacturer’s instructions), may
cause interference. The HSMT-Flex scanner has been tested and found to comply with
the limits for an industrial device in accordance with the specifications of the EMC
directive.
Warranty Information
Olympus guarantees your Olympus product to be free from defects in materials and
workmanship for a specific period, and in accordance with conditions specified in the
Olympus NDT Terms and Conditions
available at http://www.olympus-
The Olympus warranty only covers equipment that has been used in a proper
manner, as described in this instruction manual, and that has not been subjected to
excessive abuse, attempted unauthorized repair, or modification.
This device complies with the requirements of both directive
2004/108/EC concerning electromagnetic compatibility and directive
2006/95/EC concerning low voltage. The CE marking indicates
compliance with the above directives.
In accordance with European Directive 2002/96/EC on Waste Electrical
and Electronic Equipment (WEEE), this symbol indicates that the
product must not be disposed of as unsorted municipal waste, but
should be collected separately. Refer to your local Olympus distributor
for return and/or collection systems available in your country.
Summary of Contents for HSMT-Flex
Page 6: ...DMTA034 01EN Rev B March 2014 List of Abbreviations vi ...
Page 20: ...DMTA034 01EN Rev B March 2014 Introduction 14 ...
Page 46: ...DMTA034 01EN Rev B March 2014 Chapter 3 40 ...
Page 56: ...DMTA034 01EN Rev B March 2014 Chapter 6 50 ...
Page 60: ...DMTA034 01EN Rev B March 2014 Chapter 7 54 ...
Page 64: ...DMTA034 01EN Rev B March 2014 List of Tables 58 ...