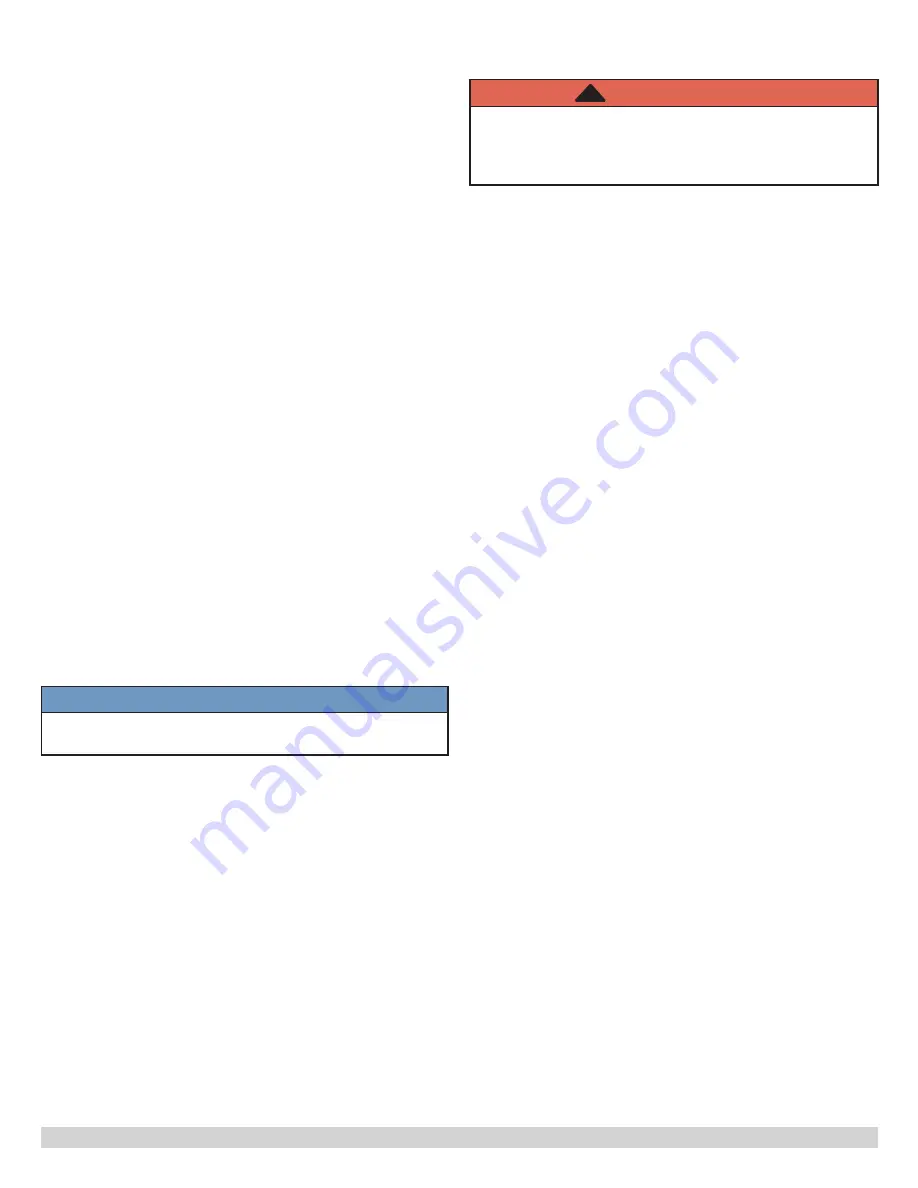
8
240011511 REV. C [05/31/2017]
18. Oil Burner Nozzles
Furnaces are certified for multiple firing rates. Furnace may be
fired at ideal rate for wide range of structures by manipulating oil
burner setup and blower settings. Refer to Table A-1 thru A-9, and
furnace rating plate to determine proper combinations. Nozzles for
alternate firing rates are included with furnace.
19. Oil Burner Adjustment
• Adjust burner air supply to maintain fuel to air ratio to obtain
ideal combustion conditions.
•
Lack of air causes "soft" and "sooty" flames, resulting in soot
build-up throughout heat exchanger passages.
•
Excess combustion air causes bright roaring fire and high
stack temperatures resulting in poor fuel efficiency.
•
LRF and LRFV operate most efficiently with No. 1 smoke
spot on Bacharach Scale. Dust will eventually build up on
air moving components of oil burner assembly resulting in
decreased air supply with potential soot build up in flue gas
passageways of heat exchanger. Soot behaves as insulator
and impairs good heat transfer. Stack temperature increases,
and efficiency decreases. To avoid this problem, adjust the air
supply as follows:
»
Chimney vented units
- adjust air supply to provide no
more than a trace smoke spot on the Bacharach scale.
»
Direct vented units
- adjust air supply for zero smoke per
the Direct Vent Supplement Installation, Operation and
Maintenance Manual included with direct vent furnace.
20. Burner Electrodes
Correct positioning of electrode tips with respect to each other,
fuel oil nozzle, and burners is essential for smooth light ups and
proper operation.
Refer to oil burner instructions provided with furnace and
Appendix A Section A.2 in this manual for electrode specifications.
21. Burner Primary (Safety) Control
Furnace is equipped with primary combustion control, also
referred to as burner relay or burner protector relay, which uses
a cad cell located in burner housing, to monitor and control
combustion.
Dust or combustion residuals can build up on lens of cad cell
impairing its response to flame. Check cad cell for cleanliness
and proper alignment if primary control frequently shuts down
combustion.
NOTICE
Do not tamper with furnace controls they are sensitive.
If problems persist, call your service contractor.
WARNING
Fire, burn, asphyxiation hazard. Do not start the
burner unless blower access door is secured in place.
Failure to follow these instructions could result in death
or serious injury.
!
22a. CIRCULATING AIR BLOWER (LRF/LRFV)
• LRF furnace models may be equipped with either direct
drive or belt drive blower systems.
• LRFV furnace models are equipped with direct drive blower
systems.
• LRF models are equipped with PSC motors.
• LRFV models are equipped with electronically commutated
motors (ECM).
Direct Drive Blower Systems
• Direct drive blower speed adjustments are not normally
required in properly sized extended plenum duct systems.
Motor RPM and air CFM delivery will vary automatically to
accommodate conditions within usual range of external
static pressures typical of residential duct systems.
• Under-sized duct systems may require higher blower speed
to obtain system temperature rise.
• Some older duct systems were not designed to provide
static pressure. They typically feature special reducing
fittings at each branch run and lack block ends on the trunk
ducts. These systems may require modification to provide
some resistance to the airflow to prevent over-amping of
direct drive blower motor. Selecting a lower blower speed
may correct this problem.
• Direct drive blower speeds are adjusted by changing
"hot" wires to motor winding connections. Refer to wiring
diagrams in Appendix B or wiring diagram label affixed to
furnace.
• Do not move neutral wire (normally white wire) to
adjust blower speed.
• Single blower speed for both heating and cooling modes
may be used. Use a "piggy-back connector" accommodating
both wires on a single motor tap.
• It is also acceptable to connect selected motor speed with a
pigtail joined to both heating and cooling speed wires with
a wire nut.
• Safety precaution against accidental disconnection of wires
by vibration, secure wire nut and wires with few wraps of
electricians tape.
• Do not connect power leads between motor speeds.
Always connect neutral wire to motor's designated
neutral terminal.
• If joining blower speed wiring is done in furnace junction
box, tape off both ends of unused wire.
• Do not use blower speed wires as source of power to
accessories as electronic air cleaners and humidifier
transformers. Unused motor taps auto-generate
sufficiently high voltages to damage accessory
equipment.