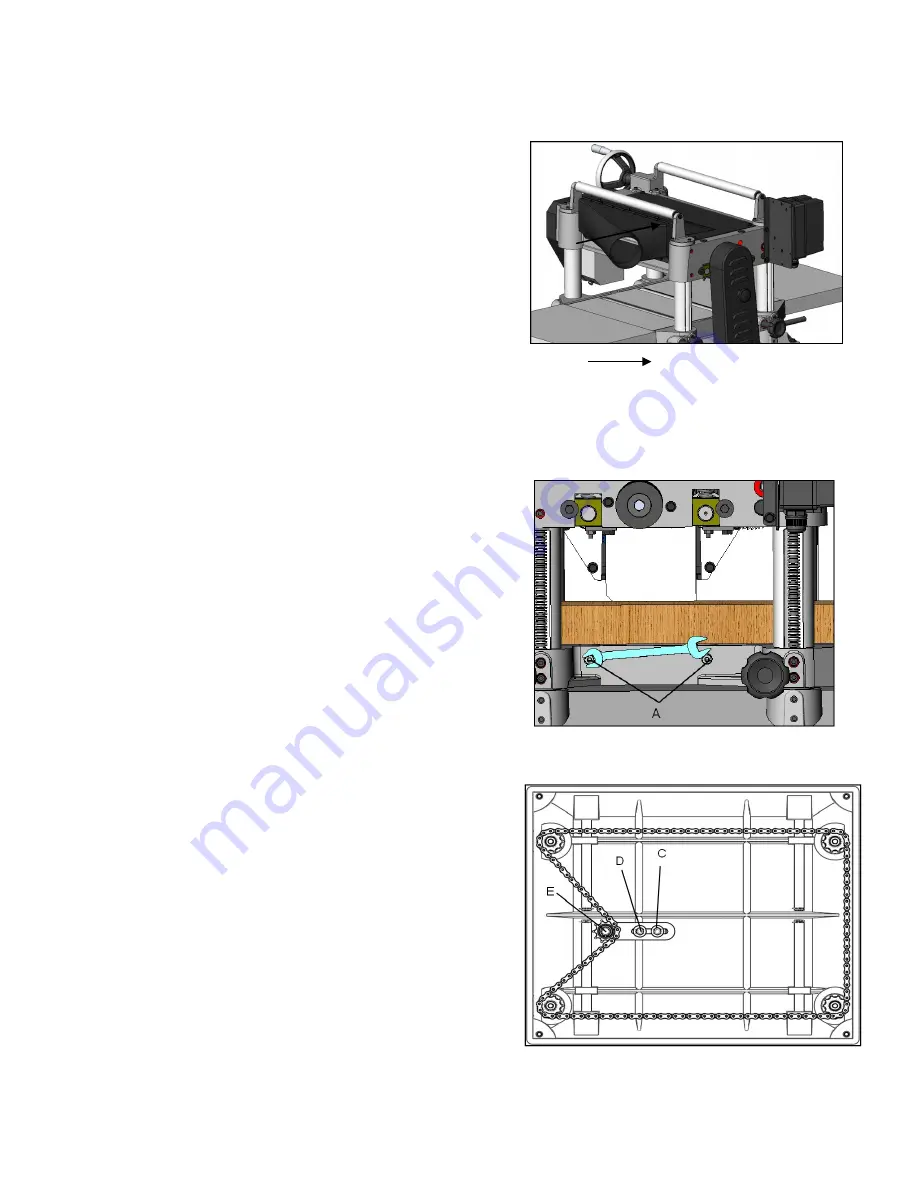
11
TABLE ROLLERS
Your planer is supplied with two idler table rollers
(Figure 15) which help to reduce friction. It is not
possible to give exact dimensions on the proper height
setting of the table rollers because each type of wood
behaves differently. As a general rule, however, when
planing rough stock the table rollers should be set at
high position. When planing smooth stock the rollers
should be set at low position. The down side to the
rollers being high is the increased probability of ‘snipe’
appearing on the work piece. This is an increased
amount of material being removed at the ends of the
board because the board rocks on the table roll.
To make adjustment, turn the eccentric adjusters ‘A’
as shown in Figure 16. Use a straight edge across
both front and rear rollers and check that they are at
the same height side to side.
Note: each adjuster is secured in place by a set
screw on top of the adjuster. It is accessed with
an allen key through the top of the table casting
.
TABLE PARALLELISM
If your material is tapered from left to right the
cutterhead may not be parallel to the table. Using the
guage block constructed earlier, check the cutterhead
to table for parallelism. If the head is not parallel,
remove the bolts securing the planer to the stand and
tilt the planer on it’s side. Remove bolt C and loosen
bolt (D) (Fig.26). This will enable you to move the idler
sprocket assembly (E) this procedure will release the
tension of the chain.
Remove chain from sprocket on the end that must be
adjusted. When chain has to be released, do not turn
the sprocket more than one or two teeth. Turn sprocket
clockwise to decrease the distance, and counter
clockwise to increase the distance between the table
and head casting.
Fig. 15
Fig. 16
Fig. 17
Summary of Contents for 4420
Page 10: ...Figure C Figure D Figure E...
Page 21: ...15...
Page 22: ...16...
Page 23: ...17...
Page 24: ...18 1...
Page 25: ...19...