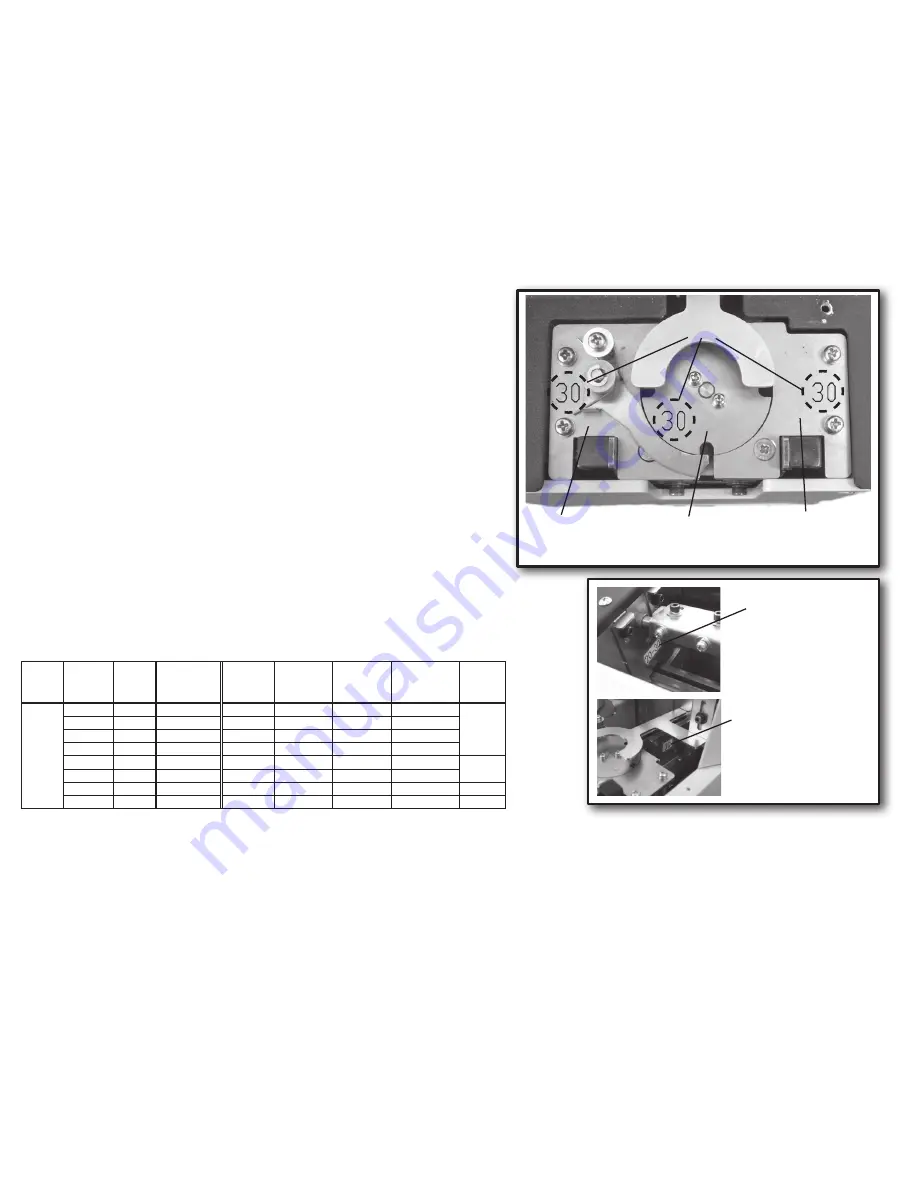
-
7
-
5.
ADJUSTMENTS AND CHECKS BEFORE USE
5-1.
Checking the model number of the main body
Check if the machine has the parts which match the nominal diameter of
the screws to be loaded. Check the model number of the rail, escaper,
stopper assembly, escaper guide-right,
and passing plate by referring to the following table.
Before delivery, each section of the machine is checked and adjusted
with panhead screws matching the nominal diameters of the model
ordered. Operate the machine with the screws loaded to check that the
pick up is smooth. If the height or or shape of the screw head is different
or if the operation is regarded as abnormal, each section must be
readjusted.
If this is the case, make the following checks and adjustments:
Identification stamp
※
This photo shows removal of the bit guide.
Stopper assembly
Escaper
Escaper guide-right
If the rail, escaper, stopper assembly, escaper guide-right and passing plate are replaced, screws with a different nominal
diameter can be accepted. After these parts are replaced, fine adjusting is required.
The respective adjusting procedures will be described elsewhere. Please read these procedures.
The rail identification
seal can be located
after removing the front
cover.
○ Check the screw load amount
○ Check and adjust the passing plate
○ Check and adjust the holding plate
○ Check and adjust the timer
○ Check and adjust the brush
○ Check and adjust the rail vibration
○ Check and adjust the front and rear sides of the rail
P a s s i n g p l a t e
identification seal
㻾㼑㼒㼑㼞㼑㼚㼏㼑㻌㼠㼍㼎㼘㼑㻌㼛㼒㻌㼠㼔㼑㻌㼟㼜㼑㼏㼕㼒㼕㼑㼐㻌㼟㼏㼞㼑㼣㼟
㻿㼏㼞㼑㼣
㼒㼑㼑㼐㼑㼞
㼟㼑㼞㼕㼑㼟
㻿㼏㼞㼑㼣
㼒㼑㼑㼐㼑㼞
㼙㼛㼐㼑㼘
㻿㼏㼞㼑㼣
㼟㼕㼦㼑
㻱㼤㼏㼔㼍㼚㼓㼑㻌㼗㼕㼠
㻺㼛㻚
㻾㼍㼕㼘㻌㼙㼛㼐㼑㼘
㻺㼛㻚
㻱㼟㼏㼍㼜㼑㼞
㼙㼛㼐㼑㼘㻌㻺㼛㻚
㻿㼠㼛㼜㼜㼑㼞
㼍㼟㼟㼑㼙㼎㼘㼥
㼙㼛㼐㼑㼘㻌㻺㼛㻚
㻱㼟㼏㼍㼜㼑㼞
㻌㼓㼡㼕㼐㼑㻙㼞㼕㼓㼔㼠
㼙㼛㼐㼑㼘㻌㻺㼛㻚
㻼㼍㼟㼟㼕㼚㼓
㼜㼘㼍㼠㼑
㼙㼛㼐㼑㼘㻌㻺㼛㻚
㻿㼏㼞㼑㼣
㼟㼕㼦㼑
㻿㼏㼞㼑㼣㻌㼟㼔㼍㼒㼠
diameter(
φ
)
㻿㼏㼞㼑㼣
㼔㼑㼍㼐
㼐㼕㼍㼙㼑㼠㼑㼞
(
φ
)
㼃㼍㼟㼔㼑㼞
㼐㼕㼍㼙㼑㼠㼑㼞
(
φ
)
㻿㼏㼞㼑㼣
㼔㼑㼍㼐
㼠㼔㼕㼏㼗㼚㼑㼟㼟
(mm)
㻿㼏㼞㼑㼣
㼟㼔㼍㼒㼠
㼘㼑㼚㼓㼠㼔
(mm)
㻿㼑㼙㼟
㻰㼛㼡㼎㼘㼑
㼟㼑㼙㼟
㼃㼍㼟㼔㼑㼞
㼔㼑㼍㼐
㻻㻹㻙㻞㻢㻹㻞㻜
φ
㻞㻚㻜
㻻㻹㻹㻞㻜㻿㻱㼀
㻻㻹㻹㻞㻜
㻿㻵㻱㻞㻜
㻿㻵㻱㻿㻞㻜
㻿㻵㻱㻹㻞㻜
φ
㻞㻚㻜
1.9~2.1
2.4~6
2.4~10
0.35~6
2.6~25
○
○
○
○
○
○
㻻㻹㻙㻞㻢㻹㻞㻟
φ
㻞㻚㻟
㻻㻹㻹㻞㻟㻿㻱㼀
㻻㻹㻹㻞㻟
㻿㻵㻱㻞㻟
㻿㻵㻱㻿㻞㻟
㻿㻵㻱㻹㻞㻟
φ
㻞㻚㻟
2.2~2.4
2.7~6
2.7~10
0.35~6
2.9~25
○
○
○
○
○
○
㻻㻹㻙㻞㻢㻹㻞㻢
φ
㻞㻚㻢
㻻㻹㻹㻞㻢㻿㻱㼀
㻻㻹㻹㻞㻢
㻿㻵㻱㻞㻢
㻿㻵㻱㻿㻞㻢
㻿㻵㻱㻹㻞㻢
φ
㻞㻚㻢
2.5~2.7
3.0~6
3.0~10
0.35~6
3.2~25
○
○
○
○
○
○
㻻㻹㻙㻞㻢㻹㻟㻜
φ
㻟㻚㻜
㻻㻹㻹㻟㻜㻿㻱㼀
㻻㻹㻹㻟㻜
㻿㻵㻱㻟㻜
㻿㻵㻱㻿㻟㻜
㻿㻵㻱㻹㻟㻜
φ
㻟㻚㻜
2.9~3.2
3.5~6
3.5~11
0.35~6
3.6~25
○
○
○
○
○
○
㻻㻹㻙㻞㻢㻹㻟㻡
φ
㻟㻚㻡
㻻㻹㻹㻟㻡㻿㻱㼀
㻻㻹㻹㻟㻡
㻿㻵㻱㻟㻡
㻿㻵㻱㻿㻟㻡
㻿㻵㻱㻹㻟㻡
φ
㻟㻚㻡
3.4~3.7
4.0~8
4.0~11
0.35~6.5 4.1~25
○
○
○
○
○
○
㻻㻹㻙㻞㻢㻹㻠㻜
φ
㻠㻚㻜
㻻㻹㻹㻠㻜㻿㻱㼀
㻻㻹㻹㻠㻜
㻿㻵㻱㻠㻜
㻿㻵㻱㻿㻠㻜
㻿㻵㻱㻹㻠㻜
φ
㻠㻚㻜
3.8~4.2
4.5~8
4.5~12
0.35~6.5 4.6~25
○
○
○
○
○
○
㻻㻹㻙㻞㻢㻹㻡㻜
φ
㻡㻚㻜
㻻㻹㻹㻡㻜㻿㻱㼀
㻻㻹㻹㻡㻜
㻿㻵㻱㻡㻜
㻿㻵㻱㻿㻡㻜
㻿㻵㻱㻹㻡㻜
㻻㻹㻡㻜
φ
㻡㻚㻜
4.8~5.2
5.5~10
5.5~12
0.35~7
5.6~25
○
○
○
○
○
○
㻻㻹㻙㻞㻢㻹㻢㻜
φ
㻢㻚㻜
㻻㻹㻹㻢㻜㻿㻱㼀
㻻㻹㻹㻢㻜
㻿㻵㻱㻢㻜
㻿㻵㻱㻿㻢㻜
㻿㻵㻱㻹㻢㻜
㻻㻹㻢㻜
φ
㻢㻚㻜
5.8~6.2
6.5~11
6.5~12
0.35~7.5 6.6~25
○
○
○
○
○
○
㻌㻌㻌㻌㻌
㻌
㻻㻹㻙㻞㻢㻹
㻻㻹㻞㻜㻙㻟㻜
㻻㻹㻟㻡㻙㻠㻜
㻿㼔㼍㼜㼑㻌㼛㼒㻌㼟㼏㼞㼑㼣㻌㼔㼑㼍㼐
㻼㼍㼚㻌㼔㼑㼍㼐
㼎㼕㼚㼐
㻲㼘㼍㼠㻌㼔㼑㼍㼐
㼔㼑㼤㼍㼓㼛㼚
㼒㼘㼍㼚㼓㼑
㼎㼛㼘㼠