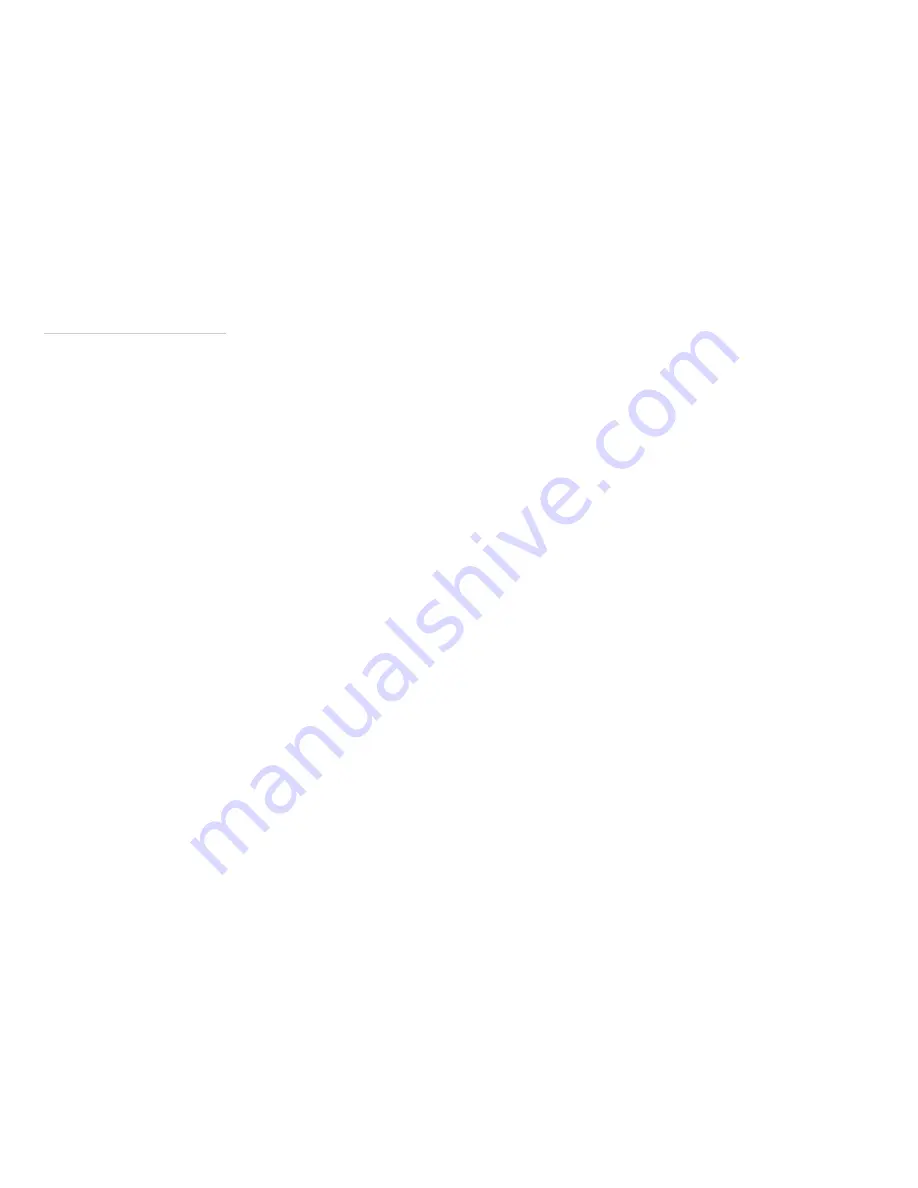
18
General handling set-up
Front suspension.
Front fork travel is not used to its full
capacity. Harsh feeling, front wheel grip is
not satisfactory in bumpy turns.
Suspension too hard.
• Decrease the front fork
compression damping.
• Change to softer springs.
Suspension bottoming, too soft during
entire travel.
Spring too weak or compression damping too soft.
• Increase oil level 5 mm.
• Increase compression damping.
• Change to stiffer springs.
Suspension bottoming, but can handle
smaller bumps.
Damping force not progressive enough.
• Increase the oil level.
Can handle smaller bumps but is too hard
during the last part of the travel.
Damping force is too progressive.
• Decrease the oil level.
Front end feels low, initially feels soft, but is
not bottoming.
The initial spring rate is too soft or spring preload
is too low.
• Increase the spring pre-load.
Feels harsh over small bumps, but using full
wheel travel.
Too much spring pre-load or too much compres-
sion damping.
• Increase the oil level or change
to softer springs.
• Decrease the compression damping.
• Decrease the spring pre-load.
• Clean the oil seals and scrapers. Use Öhlins
grease 146-01 for regreasing.
Can handle the first in a series of bumps but
feels hard after a few more bumps. Frontal
grip insufficient in rough and bumpy turns.
Too much rebound damping.
• Decrease the rebound damping.
Front end rebound too fast after a bump.
Front wheel grip insufficient in bumpy
curves.
Not enough rebound damping, or too much
spring pre-load
• Increase the rebound damping.
• Decrease the spring pre-load.
Front end ”ploughs”, understeers.
Shallow front fork angle. Front end too high in
comparison to rear end.
• Decrease the front fork
compression damping.
• Raise the fork legs approximately
5 mm in the triple clamp.
• Change to softer fork springs.
Front end unstable at high speed, unstable
when accelerating out of curves.
Front fork angle too steep. Front end too low in
comparison to rear end.
• Lower the fork legs approximately
5 mm in triple clamp.
• Change the front fork springs to
harder ones.
Front end unstable during deceleration.
Front fork angle too steep during braking. Front
end too low or rear end too high.
• Increase the oil level in the front fork.
• Change to harder fork springs.
• Increase the front fork
compression damping.
Front end falls into the curves (oversteering)
especially in sand.
Steep front fork angle. Front end too low in com-
parison to rear end.
• Increase the front fork
compression damping.
• Change to harder springs.
• Lower fork leg approximately
5 mm in the triple clamp.