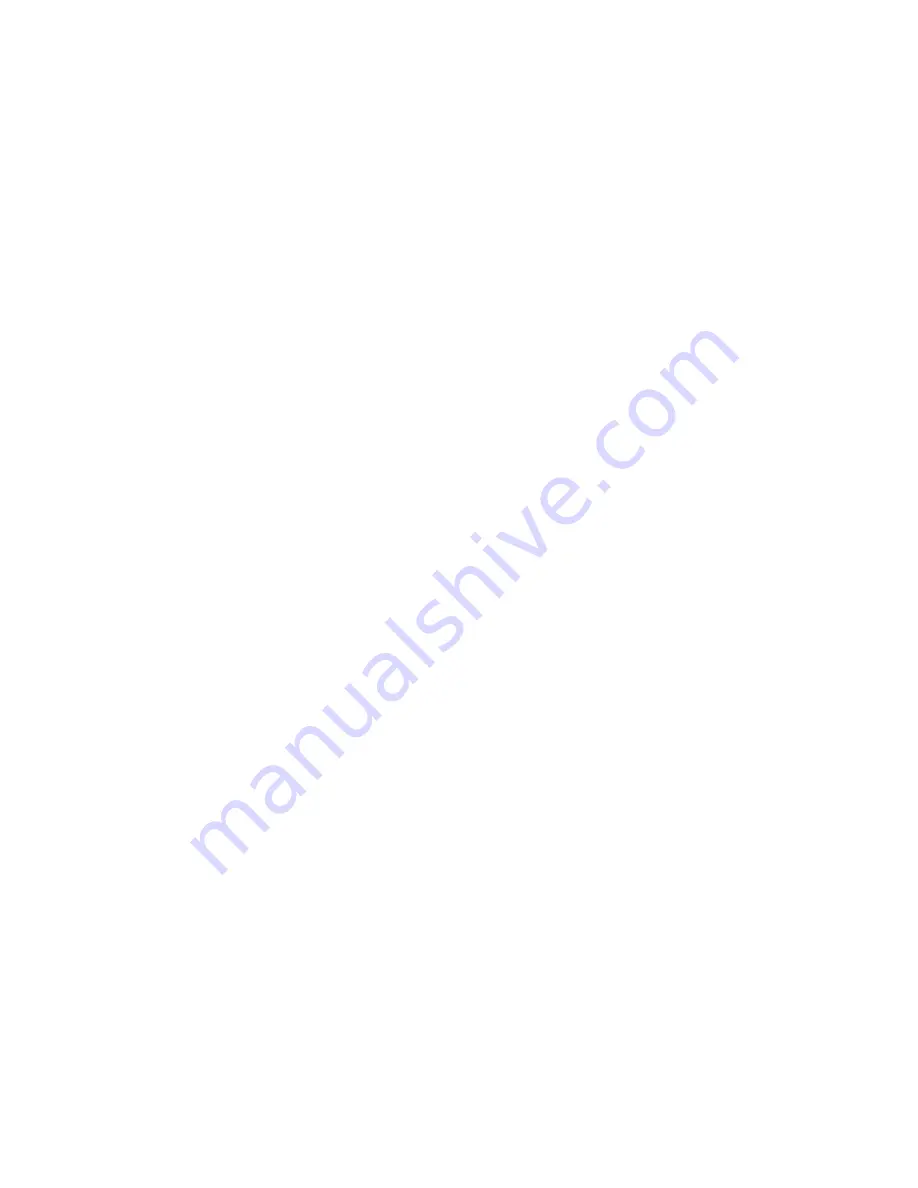
6
3.
Design, Operation, Illustrations
The hot water high pressure cleaner comprises an inline plunger high pressure
pump with safety shut-down system a high capacity oil heating system with
stainless steel heat exchanger.
The high pressure pump is directly flanged to the electric motor. It sucks the
feed water from a level controlled water tank and directs it via the safety/
control unit into a heating coil where it is heated up to operating temperature.
Between high pressure pump and heating coil a safety/control valve is installed
which opens as soon as max. operating temperature is exceeded by more
than 10 % and returns the water which is not taken by the nozzle into the
suction line of the pump.
By activating the heating system, the fuel pump sucks fuel from the storage
tank via a filter system and injected into the burner chamber. The required
oxygen is pressed into the burner chamber by a blower system. The mixture is
atomized and ignited by the ignition electrodes which are continuously
powered by the high voltage transformer. The heating flame totally burns
without touching the heat exchanger shells. During this procedure infra-red
rays are generated which, in common with hot exhaust fumes, economically
heat up the water to the working temperature which is adjusted at the
thermostat.
The working pressure can continuously be adjusted by means of the adjusting
handle at the double lance.
If required, suitable detergent can be injected into the water stream from the
storage tank, via filter and non-return valve and applied onto the cleaning
object.
In order to protect the machine against formation of mineral deposits, an anti-
scaling system is installed which continuously feeds an anti-scalant liquid into
the water storage tank.
The machine is equipped with a safety shut-down system. When closing the
spray pistol the machine keeps on running for approx. 15 seconds in
circulation mode and afterwards switches into stand-by mode. In prallel, a
safety-/control unit interrupts the fuel supply so that the burner is deactivated.
When releasing the spray pistol again, the machine is restarted, pressure
generated and burner activated, so that the cleaning task can be continued
without delay.