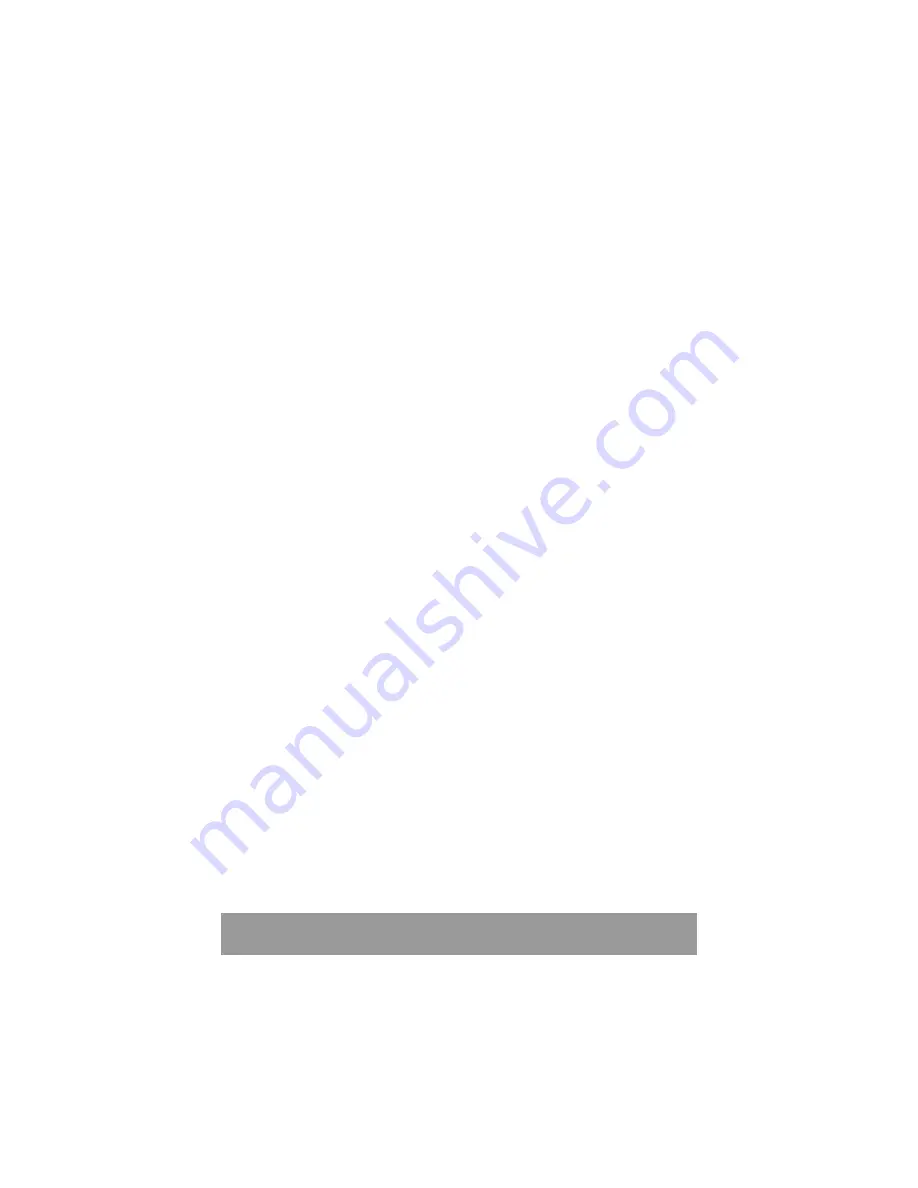
5
Safety Instructions
Please read this manual and the related documentation thoroughly and
familiarize yourself with the directions before installing, operating,
performing inspection and preventive maintenance. Make sure to follow
the directions correctly to ensure normal operation of the product and
your safety.
• When designing a system using this product, consider proper
prevention against external environmental fluctuations, power failure
and noise, etc., in accordance with installation requirements. Design
and implement an external circuit that allows your system to operate
continually and safely in any system failure.
• Make sure to disconnect the external power to the product before
performing mounting, wiring, inspection, maintenance and cleaning.
Never touch the power terminal when the power is on. Otherwise, it
may cause an electrical shock.
• Do not connect AC-powered products to a DC I/O terminal. Do not
connect externally- powered products to an internal 24V DC output
terminal.
• If you need to perform a special operation during run, such as program
editing, operation control or forced output, make sure to perform it after
ensuring safety.
• Do not connect an external device or a hand-held programmer (HHP)
that uses internal power to the product when runnig. Make sure to stop
the system and ensure safety before connecting them.
• Make sure to use an external device to PLC when configuring the
protective circuit breakers for emergencies.
• When the self-diagnostics functionality detects an error, such as internal
arithmetic error, watchdog time error, and/or connection failure, power
continues to be provided to the controller’s power supply so that your
system still works. Design and configure the circuits so that your system
runs safely under those conditions.
• The internal 24V DC power supplied to the circuits inside the PLC may
have voltage fluctuations, depending on the volume of load. These
voltage fluctuations may cause malfunction of the PLC or I/O devices
connected. Therefore, use the internal power within the allowed rating.
• Do not apply an impact to the terminal blocks or the product itself when
the power is on. Otherwise, it may cause malfunction and failure of the
product, or electrical shock.