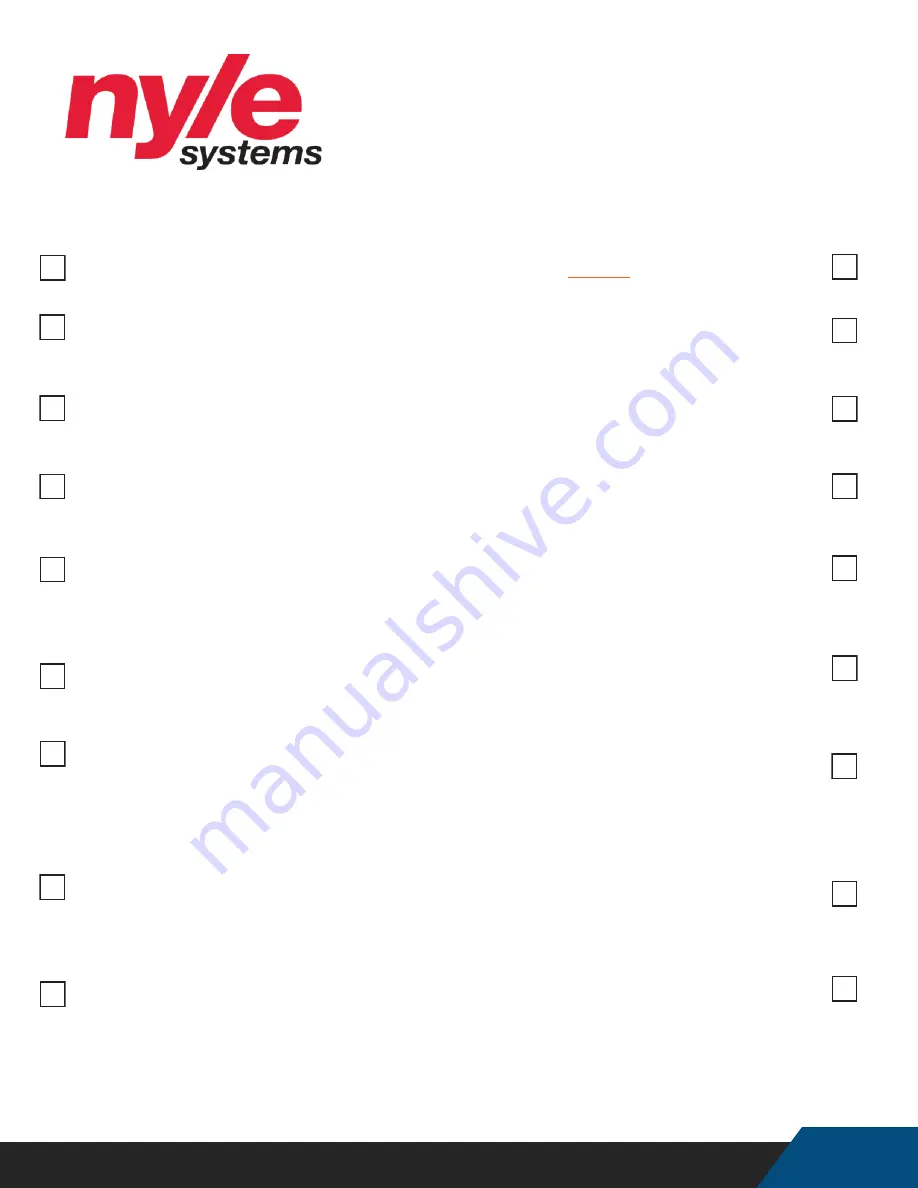
25
Pre-Startup Checklist
1.
Before applying power, check all electrical connections. Tighten if necessary.
2. Verify electrical installation. Power requirements and branch circuit disconnecting
means match equipment nameplate specifications.
3. Make sure the hydronic system is flushed and purged of air. Remove and clean any
strainers or filters if necessary.
4. Make sure the sensor for the temperature control is mounted to either the water tank
or strapped to a water line for proper temperature control.
5. Remove the shipping blocks from under the compressor. Loosen the nuts on the spring
mounting studs and pry up one side of the compressor at a time and remove. Leave the
nuts loose on the spring mounting studs.
6. Power up circulator pump and verify water flow through the heat pump heat
exchanger(s).
7. Apply power to the heat pump. Confirm power with an electrical meter. Check for
proper control power, should be between 120 to 125 volts. *Note: The control power
should be on for 4 to 6 hours so the compressor crankcase heater has time to warm
up the base of the compressor.
8. Start the heat pump by pressing the Start key on the Touchscreen. Go to the INFO
screen and monitor the refrigerant pressures, hot water in and out temperatures and
cold water in and out temperatures.
9. There are Fan, (or Blower, if so equipped), Direction stickers, mounted on each unit.
It may be helpful to record the operating data initially every 10 to 15
minutes just to see how the heat pump is performing.
12 Stevens Drive, Brewer, ME 04412 l (800)777-6953 l [email protected] l www.nyle.com
Unit 2
Unit 1