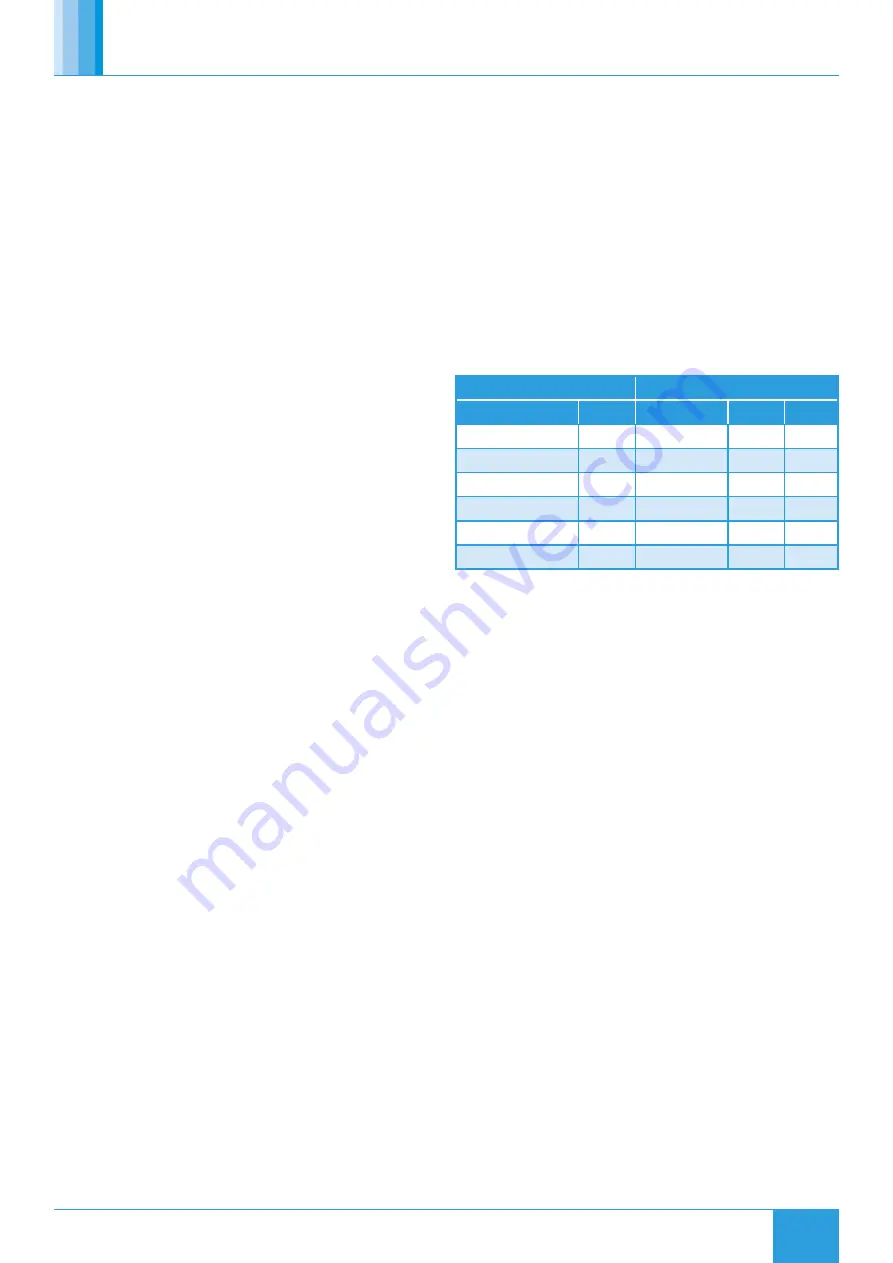
13
08. 12. 21. Document Number 671949
Nuaire | Western Industrial Estate | Caerphilly | CF83 1NA | nuaire.co.uk
XBC+ with Adapt Trend (T) Control
Installation Manual
4.0 SETTING TO WORK
Isolation - Before commencing work, make sure that the unit,
switched live and Nuaire control are electrically isolated from the
mains supply.
4.1 Filters
Remove filter access panels (observe and note airflow direction labels),
inspect filters for contamination with construction debris, replace as
necessary. Replace access panels.
Filter pressure drops will depend on actual flow rate and condition.
Observe and record filter pressure drops after performance
commissioning. Typically, filter “dirty” condition occurs when the initial
filter “clean” readings have been increased by 125Pa.
If filter manometers, pressure switches or indicators have been fitted,
they should be set or adjusted to reflect the commissioned system
operation.
4.2 Heating Coils (LPHW)
Observe the Flow and Return connection labels on the unit. Drain and
bleed valves are located on the coil. Other valves may be required in the
system pipe-work depending on the installation (by others).
Where the wet system is at risk of frost damage, the addition of a
proprietary anti-freeze solution to the water is recommended. Any
frost protection offered by the unit’s integral control system will
not operate if the power supply to the unit is interrupted.
Frost protection is activated on any unit fitted with LPHW heating,
when the outlet air temperature is 4ºC or below. The unit reacts by
shutting down the fan to prevent a ‘wind chill’ effect reducing the
temperature to a point whereby the coil could freeze and burst. The
unit will also drive open the LPHW valve to a fully open position to
allow full water flow through the coil and the main PCB will close the
‘Heat demand’ contacts. These contacts could be used to send a signal
to activate the boiler and/or valve to open to provide heat if not already
doing so.
Piped connections should be made to the unit using appropriate
techniques, and all pipework must be independently supported.
No hot work is permitted within one metre of the unit.
Ensure that installed pipework runs do not prevent or restrict access to
the unit at any point.
The completed installation (including the connections within the unit,
as these may be disturbed during installation) shall be pressure tested
to the project engineer’s specification (This is a condition of the unit
warranty).
4.3 Fan Sections
Access to the fan section is via lift off panels (Figures 1 & 23).
With the unit electrically isolated, rotate the fan impeller / drive
manually, checking that it spins freely.
Check all fixings are secure.
Units must not be operated without all access panels in place – damage
to equipment or injury to personnel may result. Units must not be
operated unless control interlocks are in place – damage to equipment
may result.
Test run motor for condition and correct rotation. Check that the
correct current overloads are fitted and that the current being drawn
does not exceed the motor nameplate value. Excessive current
normally indicates that the ductwork system resistance is different to
design.
5.0 ELECTRICAL INSTALLATION
The electrical wiring must be carried out by competent persons, in
accordance with good industry practice and should conform to all
governing and statutory bodies i.e. IEE, CIBSE, COHSE etc.
5.1 Supply
The control is powered by a 240Vac 50Hz supply. This must be isolated
local to the unit and fitted with appropriate overcurrent and fault
protection.
5.1.1 Electric Heater Supply
For models with electric heating, the heating circuit is powered by a
separate, higher current, 240VAC supply. This must be isolated local to
the unit and fitted with appropriate overcurrent protection. The main
supply is still required.
5.1.2 Electrical Supply Details - FLC
5.2 Volt Free Contacts
Note that the volt free contacts are not fused. If these are used to
power any external equipment, the installer must provide adequate
fusing or other protections.
Volt free relay contacts are rated at 5A resistive, 0.5A inductive.
Run Connections
- Contacts closed when the fan is running
Fault Connections
- No Fault = Contacts are closed
Fault
- Contacts are opened
Heat Demand
- Contacts closed when heating is selected.
5.3 Switched Live
Switch Live (SL) terminal
- A signal of 100-230V AC will activate the
switched live signal.
Switch Live 2 Boost (SL2) terminal
- A signal of 100-230V AC will
activate the switched live 2 (Fan Boost) signal.
Note that a signal from an isolating transformer will produce an
unpredictable result and is not recommended.
Volt free versions of the switched live signals are also available at
terminals T33-T34 & T35-T36. Link two contacts to activate the signal.
5.4 Damper Connections
A fan start delay can be imposed to allow the damper time to open.
This is adjustable via display screens or commissioning tools.
If an I/O damper is fitted, it must be wired to the fan run relay, and the
relay supplied with the relevant supply voltage.
See I/O Damper connection diagram for details.
5.5 Network Settings
Default IP address:
192.168.11.12
Subnet mask:
255.255.255.0
LAN 011, node 012
Unit Without Electric Heater
Unit With Electric Heater
Unit Code
FLC
Unit Code
Fan FLC Heater
XBC10HA-(N/L)**
3.0 A
XBC10HA-E**
3.0 A
6.3 A
XBC15HA-(N/L)**
4.0 A
XBC15HA-E**
4.0 A
12.5 A
XBC25HA-(N/L)**
8.0 A
XBC25HA-E**
8.0 A
18.8 A
XBC45HA-(N/L)***
6.0 A
XBC45HA-E**
6.0 A
18.8 A
XBC55HA-(N/L)**
6.0 A
XBC55HA-E**
6.0 A
37.5 A
XBC65-HA-(N/L)**
6.0 A
XBC65HA-E**
6.0 A
37.5 A