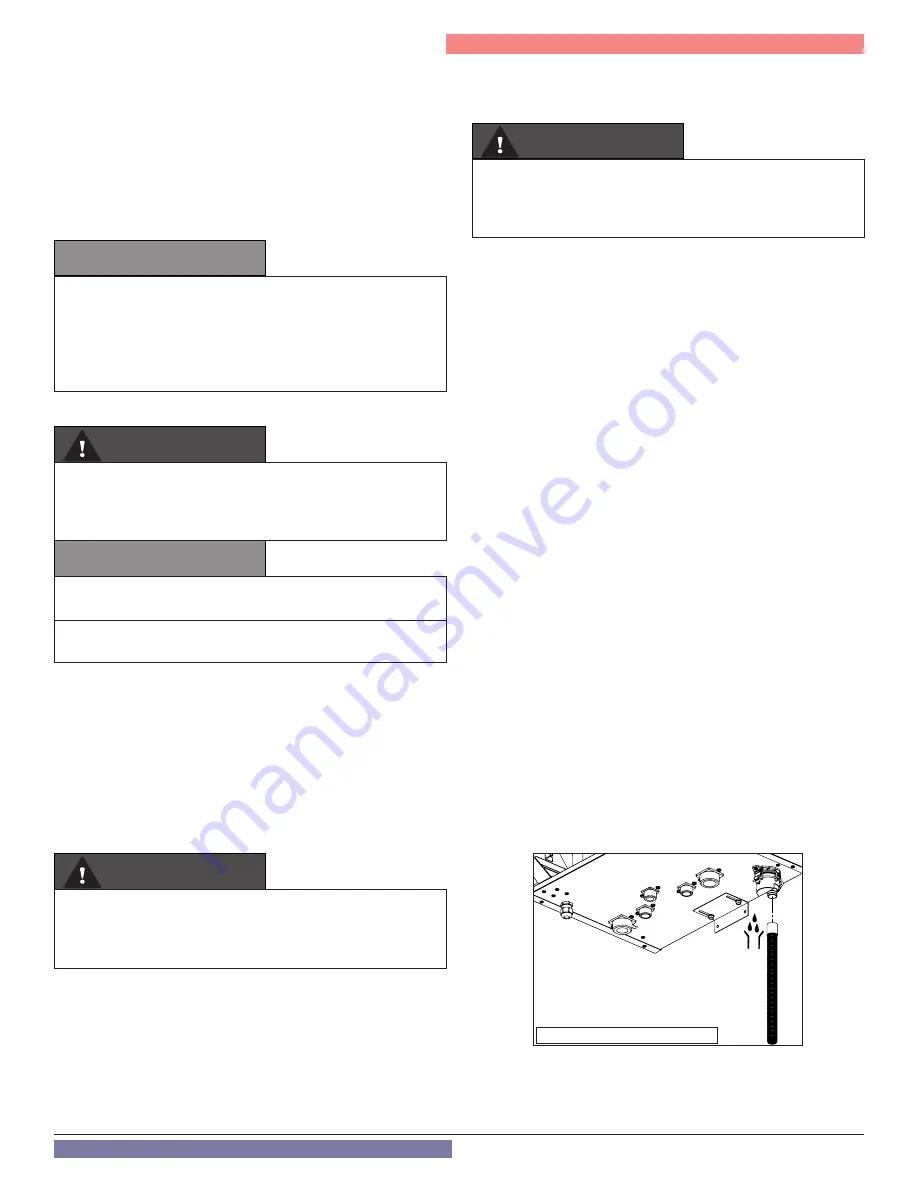
75
Part 10 - Start-Up Preparation
CAUTION
CAUTION
WARNING
WARNING
WARNING
Ensure the boiler is full of water before firing the burner.
Failure to do so will damage the boiler. Such damage IS NOT
covered by warranty, and could result in property damage,
severe personal injury, or death.
Ensure the boiler is full of water before firing the burner.
Failure to do so will damage the boiler. Such damage IS NOT
covered by warranty, and could result in property damage,
severe personal injury, or death.
Eliminate all system leaks. Continual fresh make-up water
will reduce boiler life. Minerals can build up in the heat
exchanger, reducing heat transfer, overheating the heat
exchanger and causing heat exchanger failure.
It is highly recommended to carefully follow the glycol
manufacturer’s recommended concentrations, expansion
requirements, and maintenance recommendations (pH
additive breakdown, inhibitor reduction, etc.) You must
carefully calculate the additional friction loss in the system
as well as the reduction in heat transfer coefficients.
Connect the condensate discharge pipe before filling and
purging the heating circuit.
It is important to purge the system of air to avoid damage to
the boiler.
6. Anti-freeze solutions expand more than water. For example: A 50%
by volume solution expands 4.8% in volume for a temperature
increase from 32 - 80
o
F, while water expands 3% over the same
temperature rise. Allowances must be made in system design for
expansion.
7. A 30% mixture of glycol will result in a BTU output loss of 15% with
a 5% increase in head against the system circulator.
8. A 50% mixture of glycol will result in a BTU output loss of 30% with
a 50% increase in head against the system circulator.
NOTE:
BTU losses apply to both CH and DHW.
D. System Water Fill, Purge, and Test
The boiler and heating system must be thoroughly purged of air during
the initial installation or system maintenance. Proceed as follows to
purge the boiler and heating system:
1. An automatic air purge valve has been provided inside the boiler to
aid the purging process.
2. Gradually open the main water valve until water flows. Do not open
fully.
3. Thoroughly purge each zone starting with the lowest point and
close them only when clear water free of air is visible.
4. Continue filling the system until at least 12 psi registers on the
pressure gauge.
F. Check Thermostat Circuit(s)
1. Disconnect the two external wires connected to the boiler
thermostat terminals TT1/TT2 (low voltage terminal strip).
2. Connect a voltmeter across these two incoming wires with power
supplied to the thermostat circuits. Close each thermostat, zone
valve and relay in the external circuit one at a time and check the
voltmeter reading across the incoming wires.
3. There should NEVER be a voltage reading.
4. If a voltage reading does occur under any condition, check and
correct the external wiring. (This is a common problem when using
3-wire zone valves.)
5. Once the external thermostat circuit wiring is checked and corrected
if necessary, reconnect the external thermostat circuit wires to the
boiler low voltage terminal strip. Allow the boiler to cycle.
E. Purge Air from DHW System
1. Make sure the CH and DHW lines are open and full of water. Turn on
all electric power to boiler.
2. Open hot water faucets in the DHW system. Start with the faucets
nearest the boiler.
3. Keep faucets open until water runs freely and all air is purged. Then
move on to faucets further away from the boiler in the system.
4. When water flows freely from all hot water faucets, DHW purging is
complete.
G. Condensate Removal
1. The boiler is a high efficiency condensing appliance. Therefore, the
unit has a condensate drain. Condensate fluid is nothing more than
water vapor, derived from combustion products, similar to that
produced by an automobile when it is initially started.
Condensation is slightly acidic (typically with a pH of 3 to 5) and
must be piped with the correct materials. Never pipe the condensate
using steel, copper, brass or other materials that will be subject to
corrosion. Plastic PVC or CPVC pipe are the only approved materials.
A condensate neutralizer, if required by local authorities, can
be made up of lime crystals, marble or phosphate chips that will
neutralize the condensate.
2. The boiler is equipped with a barbed outlet fitting, to which the
supplied hose must be installed and routed to a local drain. It is very
important that the condensate line is sloped downward away from
the boiler to a suitable indoor drain.
Figure 71 - Condensate Discharge
If the condensate outlet on the boiler is lower than the drain, you
must use a condensate removal pump. This pump is equipped with
two leads that can be connected to an alarm or another type of
warning device to alert the user of a condensate overflow, which, if
not corrected, could cause property damage.
Summary of Contents for TRX150
Page 98: ...98 Maintenance Notes...