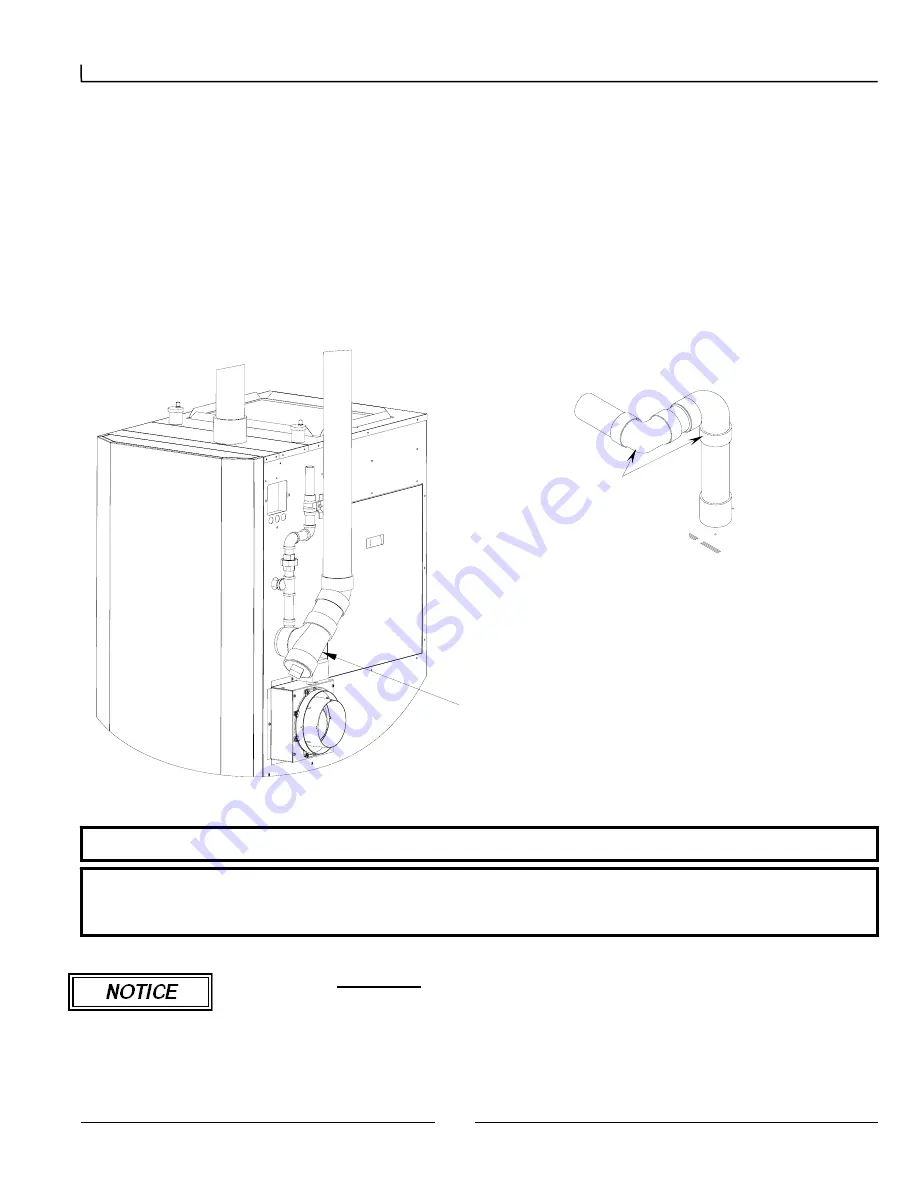
6
Matrix Installation and Operation Instructions
3.0 VENTING
The NY Thermal Matrix is a high efficiency condensing gas furnace/boiler utilizing induced power venting. Exhaust gases are to
be vented directly outdoors, using the venting method detailed in this section. Under no conditions, may this unit vent gases into a
masonry chimney, unless it is vacant, and utilizes Matrix approved venting material as illustrated in the figures in this section.
Attaching Vent Piping to Boiler
It is extremely important for the intake and exhaust piping to be adapted to the appropriate size immediately upon exiting the boiler
cabinet. The Matrix comes with a 3” male PVC fitting to connect the air intake port of the boiler. The Matrix exhaust connection
is 3” male PVC, use approved cement to connect to venting system. Check the flue outlet gasket for proper insertion and sealing
prior to and after attaching the venting. Ensure the venting system does not apply a load or stain on the flue outlet of the boiler
(recommend using two elbows to create a “swing joint” as shown above).
In Canada, the first
3 ft (915 mm)
of vent piping must be readily accessible for inspection.
IMPORTANT
The vent connection and piping must be perfectly aligned to the furnace connection. AND MUST NOT
APPLY ANY WEIGHT OR LATERAL FORCE TO THE FLUE BOX. NTI does not warranty damages to the flue
box.
It is recommended that two elbows be
used, so that the slope of the horizontal
exhaust vent does not affect the vertical
plumb of the pipe connected to the boiler.
Slope all horizontal indoor exhaust
venting ¼” to ½” per linear foot.
Figure 3.1 Venting Construction
It is recommended to have a collection point
for condensation in the intake venting.
Condensation can then be drained to an
open house drain or condensate pump.
Drain line from intake must have an
appropriate trap or shut off valve to avoid
siphoning.