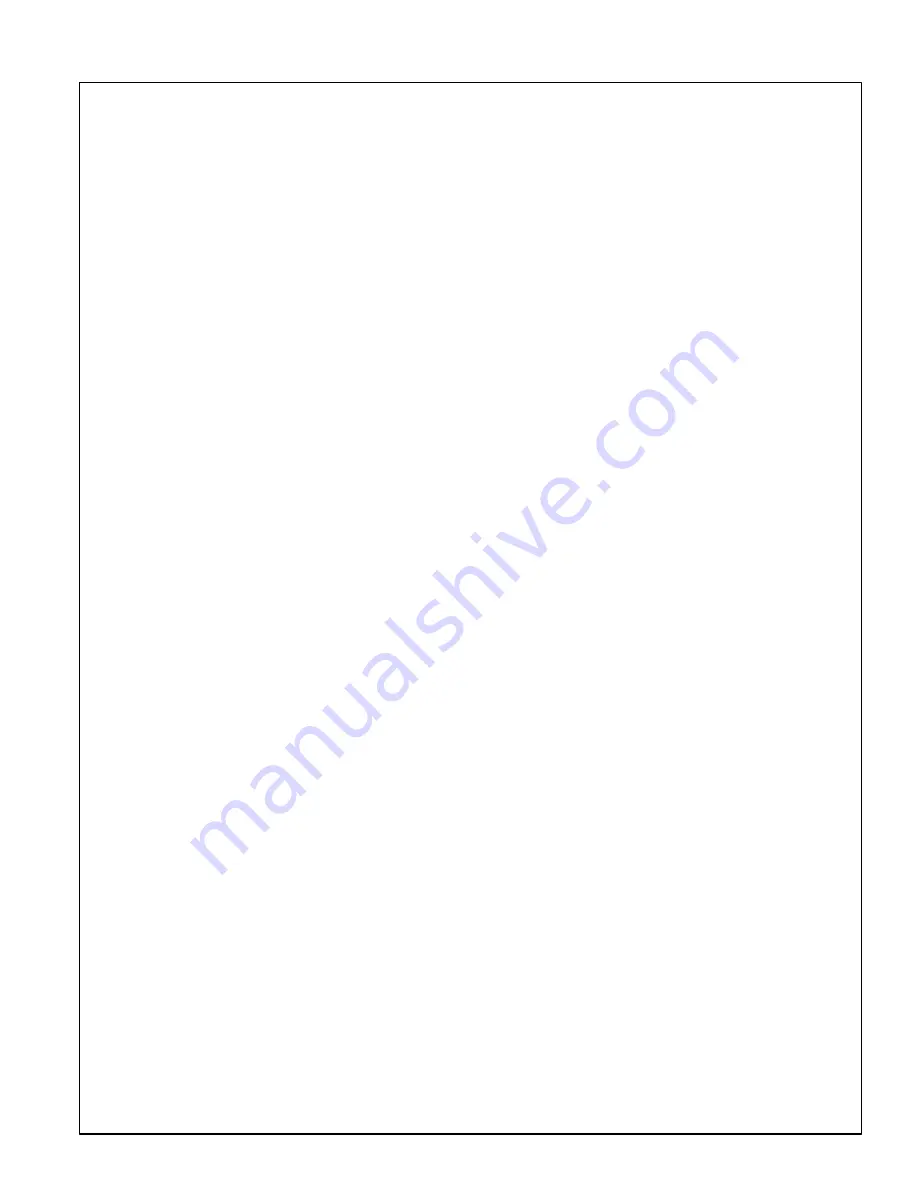
•
Pump pressure is restored by replacement of the bypass valve kit (part number 38-9-203-1) or by replacement
of the pump (part no. 48-9-459-1, 115 volt, or 38-9-201-1, 240 volt).
•
The electric solenoid provides a positive cutoff of solution flow to the spray jet bar assembly. The solenoid is
activated (
“ON”
) when the deadman lever is lifted during operation.
MOTORS
The drive motor, vacuum motor, solution pump and solenoid are located inside the body of this machine.
To gain access to these components, you must complete the following procedures:
•
Disconnect the power cord from the wall.
•
Empty all liquids from the solution tank and recovery tanks.
•
Disconnect the solution hose from the in-line solution filter, at the right side of the body.
•
Remove the vacuum hose from the vacuum shoe. Disconnect the vacuum shoe lift cable from the cable
bracket.
•
Locate the mounting studs and nuts for the swivel casters. Remove only the rear / outer nuts. This will
disconnect the rear of the main body from the chassis.
•
Lift the rear of the machine body to tilt forward for access (the prop rod that holds up the machine, is under the
solution tank).
DRIVE MOTOR / DRIVE CHAIN ADJUSTMENT
•
The propulsion drive motor is mounted at the front of the chassis, and secured by four hex bolts. Access to this
motor, and to the drive chain for chain tension adjustment and lubrication is from underneath the machine (at the
front of the machine).
•
The drive chain tension should be checked every 90 days and adjusted if necessary. To adjust the drive chain
tension, you must first loosen the four hex bolts in the chassis slots under the propulsion motor. Slide the motor
forward to decrease, or backward to increase the chain tension.
•
The drive chain should be lubricated every 90 days with a penetrating moisture resistant lubricant, using a spray
can with attachable straw to apply.
DO NOT
lubricate the chain when the machine is on a carpeted surface.
Wipe off any excess lubricant before operating the machine.
•
The propulsion motor and gear box have no service parts, and must be replaced as a single unit.
BRUSH MOTOR / BRUSH ASSEMBLY / BELT
The brush motor, brush assembly and belt are serviced by removing both parts of the plastic two-piece brush
housing cover.
•
The brush drive belt tension is adjusted by first loosening the brush motor mounting hex nuts. Slide the
motor toward the brush to decrease the tension, and away from the brush to increase the tension. When
the motor is in the proper position, the drive belt should have 1/4” to 3/8” deflection midway between the
motor and brush pulley.
•
To replace the brush drive belt, you must remove the brush shaft mounting screw at the pulley end and
loosen the screw at the opposite end. Install the new belt on the pulleys, replace and tighten the brush
shaft mounting screws, and adjust the belt tension.
•
Bristles will wear to the point where there is not enough agitation of the carpet. The nylon roller wheel can
be raised to lower the brush deeper into the carpet. Remove the roller axle that attaches the roller wheel
from its holding bracket, and reinstall the axle into the upper holes in the bracket.
WARNING
Do not use the upper roller axle position with a new or nearly new brush. This will force the brush to an
exaggerated down position, overload the circuit breaker, and damage the brush drive motor.
•
The brush motor is protected by a circuit breaker mounted on the control panel. The circuit breaker will open
(pop-up) when the brush motor is overloaded. When the circuit breaker “overloads” the stem will pop up to
expose the white portion of the shaft. Unplug the machine. Prior to resetting the circuit breaker, you must inspect
the brush assembly for obstructions such as foreign objects, strings around the brush shaft or “frozen” bearings.
•
Reset the circuit breaker by pushing down on the stem until it “clicks” into the
“ON”
position.
SERVICE AND MAINTENANCE
Summary of Contents for PONY 20 SCA
Page 3: ...WIRING DIAGRAM...
Page 11: ...SOLUTION RECOVERY TANKS...
Page 15: ...BRUSH HOUSING...
Page 19: ...VAC SHOE...