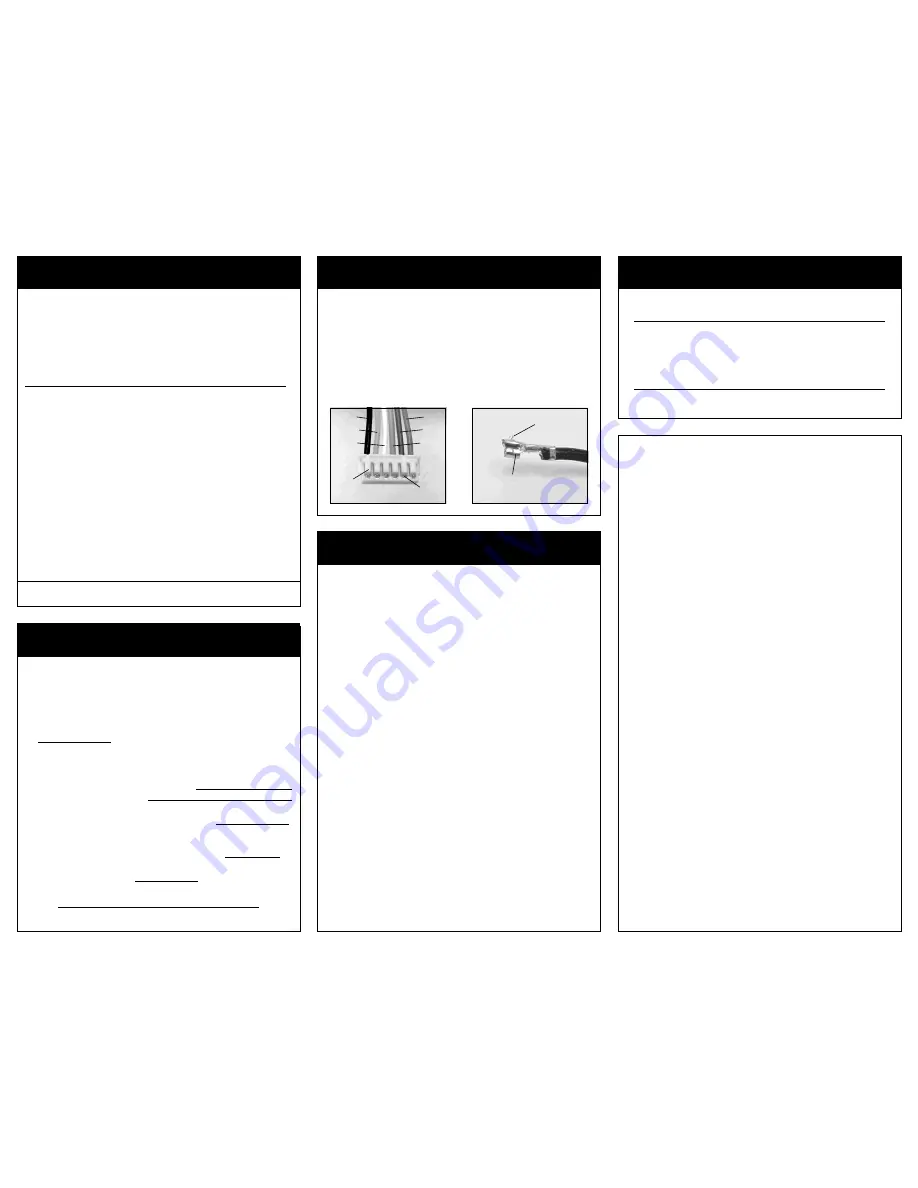
The Super Sport 10.5 ESC is equipped with dual throttle
programs: Forward, Brake, & Reverse
(
Mode 1
)
, and Forward
& Brake only
(
Mode 2
)
. By disabling the reverse feature of
the Super Sport 10.5, the speed control can be set-up for
forward and brake only operation, which may be useful if
you are going to use this vehicle at your local track and
they do not allow reversible ESCs to be used during racing.
Selecting Throttle Mode with TRANSMITTER ON
With transmitter ON & ESC connected to receiver and battery:
1. TURN ON THE SPEED CONTROL’S POWER
2. PRESS & HOLD SPEED CONTROL’S SET BUTTON
With the transmitter throttle at neutral,
press and hold
the SET button
on Super Sport 10.5, and
continue
holding button until all 4 status LEDs turn on
.
3. RELEASE SPEED CONTROL’S SET BUTTON
All
status LEDs will flash together
. The number of times
the LEDs flash indicates the Throttle Mode selected.
4. PRESS & RELEASE SET BUTTON TO SELECT MODE
Each press will change the Throttle Mode.
5. WAIT FOR SPEED CONTROL TO EXIT PROGRAMMING
When the speed control’s SET button is not pressed for
about 3 seconds, the
ESC loads the selected Throttle Mode
into memory and exits programming--the red status LED
will turn solid red indicating that the speed control is back
at neutral and ready to go.
REMEMBER: Whenever One-Touch set-up is performed, ESC automatically reverts to
factory default settings & the Throttle Mode reverts to Mode1 (Fwd, Brake, & Rev).
TROUBLE-SHOOTING GUIDE
This section describes possible ESC problems, causes, and solutions.
Steering Channel Works But Motor Will Not Run
• Make sure motor sensor harness is plugged into ESC––check for
damaged wires. Green & red status LEDs will be blinking fast.
• Make sure input signal harness is plugged into ESC & throttle
channel of receiver. Check throttle channel operation with a servo.
Check wiring sequence of receiver signal harness. Green & red
status LEDs will both be on solid.
• ESC may have shut down due to locked rotor detection––return
throttle to neutral position to regain motor control––check
vehicle’s drive train for free operation. Blue & green status LEDs
will both be blinking.
• ESC or motor may have shut down due to thermal overload––
allow system to cool down & return throttle to neutral position
to regain motor control––check for free operation of drive train
for possibly overloading that could result in overheating. Blue
status LED will be blinking until cooled down.
• ESC may have shut down due to thermal overload or locked
rotor detection & ESC’s neutral point is too far off to sense that
throttle has been returned to neutral.
Blue & green status LEDs blinking indicates Locked Rotor Detection.
Blue LED blinking indicates thermal shut-down.
• Possible internal damage––Refer to Service Procedures.
Receiver Glitches/Throttle Stutters During Acceleration
• Receiver or antenna may be too close to speed control, power
wires, or battery.
• Bad connections––Check wiring, connectors, and sensor harness.
• External Power Capacitor damaged or not installed.
Motor and Steering Servo Do Not Work
• Check wires, receiver signal harness wiring & color sequence,
radio system, crystals, battery/motor connectors, & battery pack.
• Possible internal damage––Refer to Service Procedures.
Speed Control Runs Hot
• Gear ratio has been changed and is too low––Increase gear ratio
(see ‘VEHICLE GEARING’ section).
Model Runs Slowly/Slow Acceleration
• Gear ratio has been changed and is too low––Increase gear ratio
(see ‘VEHICLE GEARING’ section).
• Check battery connectors––Replace if needed.
• Incorrect transmitter/ESC adjustment––Refer to ‘ONE-TOUCH
PROGRAMMING’ section.
• External Power Capacitor damaged or not installed.
• Motor bearings worn––Refer to ‘MOTOR MAINTENANCE’ section.
ESC Is Melted Or Burnt/ESC Runs With Switch Off
• Internal damage––Refer to Service Procedures.
*For more assistance call our Customer Service Department.
MOTOR MAINTENANCE
• CHECK MOTOR SCREWS
Check all motor screws for
loosening at regular intervals, just like other hardware on
your vehicle.
Note: The 3 main 4-40 socket head screws on the
shaft end of the motor may become loose after a few runs of the
motor and will need to be tightened.
Also check the 3 flat head
screws securing the end cap on the back of the motor.
• CHECK MOTOR BEARING WEAR
After extensive use,
the ball bearings in the end bells of your brushless motor
may need to be replaced. While the design of the motor
will keep the majority of the debris out of the bearings, some
debris may get in, and eventually wear will occur. If the shaft
will not spin freely, you may need to replace the motor
bearings
(replacement bearings available in Novak kit #5904--
Contact
our Customer Service Dept. if you do not feel comfortable changing
the bearing on your own
)
. A small drop of light oil on the
bearings periodically can help extend bearing life--too much
oil will cause problems, so apply sparingly.
• PERIODIC MOTOR CLEANING
We recommended that
you disassemble the motor and clean the inside of it at
regular intervals. About once a month, if you subject the
motor to heavy weekly usage (like club racing once a week),
is a good schedule. Every few months if you used less heavily.
CLEAN INSIDE MOTOR:
Remove 4-40 socket head cap
screws on the shaft side & remove end bell. Next, remove
the rotor by pulling it out by the shaft--be careful not to
damage magnet or lose shaft spacers
(if epuipped with)
. Use
compressed air to blow debris off rotor and out of the
inside of the motor--
DO NOT USE SOLVENTS
. Reassemble,
making sure the short spacer is on the pinion side of rotor.
CLEAN THE REAR BEARING:
Remove 4-40 flat heat screws
and remove the black plastic end cap (cap may stick--pry
up gently). Wipe off the rear bearing & replace end cap.
SENSOR HARNESS WIRING
Should any of the 26G Teflon wires pull out of the connector
on the end of the motor’s sensor harness, replace them into
the appropriate slot in the connector as shown below. The
connector has small plastic tabs that grab a small raised barb
on the back of the metal socket that is crimped onto the ends
of the Teflon wire. The plastic tab should be checked to make
sure it has not deformed excessively before inserting the
socket into the plastic connector housing.
Note: If the motor’s sensor harness becomes damaged, contact the
Novak Customer Service Department.
black
orange
white
plastic
tabs
red
blue
green
metal
barbs
raised
metal
barb
metal socket
on end of Teflon
sensor harness wires
The Losi vehicle this brushless speed control and motor came
with used 19 tooth pinion gear and a 90 tooth spur gear.
The stock gearing is for general outdoor use--If the model
is going to be run in a confined area, a smaller pinion gear
may be necessary to prevent over-heating.
{If operating temperatures get too high, the ESC and/or motor may thermally
shut down & may cause internal damage that voids product warranty}
Similarly, increasing the pinion size can cause over-heating.
The Super Sport 10.5 ESC and SS4300 motor are designed to operate
comfortably from 160ºF-170ºF (warmer than a typical brush-type ESC/motor).
VEHICLE GEARING
(Important)
REVERSE DISABLE
NOTE: If transmitter’s throttle end point adjustments are
changed, the ESC’s One-Touch programming will need to
be performed. If you do not, you might not get optimal
performance from your brushless ESC/motor system.
With ESC connected to receiver & a charged battery pack:
1. TURN ON THE TRANSMITTER’S POWER
2. PRESS & HOLD SPEED CONTROL’S SET BUTTON
3. TURN ON THE SPEED CONTROL’S POWER
With transmitter throttle at neutral, and still
pressing the
SET button
slide the
ON/OFF switch
to ON position
.
4. CONTINUE HOLDING SET BUTTON UNTIL RED LED IS ON
5. RELEASE SET BUTTON AS SOON AS LED TURNS RED
6. PULL TRANSMITTER THROTTLE TO FULL-ON POSITION
Hold it there until the
green status LED
turns solid green
.
Note: Motor will not run during programming even if connected.
7. PUSH TRANSMITTER THROTTLE TO FULL-BRAKES
Hold it there until the
green status LED
blinks green
.
8. RETURN TRANSMITTER THROTTLE TO NEUTRAL
Red status LED
will
turn solid red
, indicating that the
speed control is at neutral and that proper programming
has been completed.
If you experience any problems during One-Touch programming,
turn off the ESC and repeat above programming steps.
ONE-TOUCH PROGRAMMING