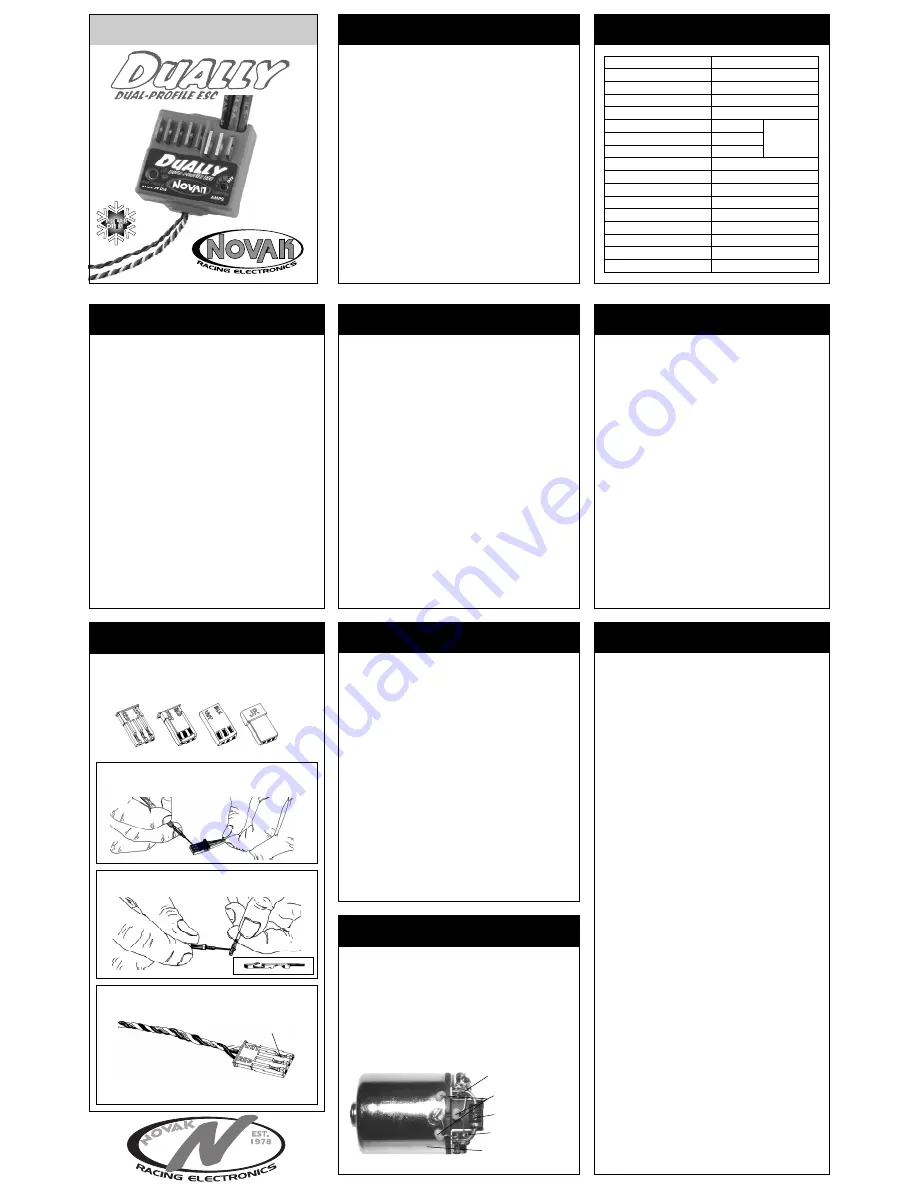
OPERATING INSTRUCTIONS
DUALLY DUAL-PROFILE
SPECIFICATIONS
Input Voltage
4-7 cells
(1.2 volts DC/cell)
Case Width
1.63 inches [4.14 cm]
Case Depth
1.72 inches [4.37 cm]
Case Height
0.65 inch
[1.65 cm]
Weight
(w/o heat sinks)
2.10 ounces [59.53 g]
On-Resistance
@ Transistors
0.0007
Ω
Rated Current
400 amps
Braking Current
100 amps
BEC Voltage / Current
6.0 volts DC / 3.0 amps
Wire Size
(Battery/Motor)
14 gauge
Wire Length
(Battery/Motor)
9 inches
[22.8 cm]
Signal Harness Length
8 inches
[20.3 cm]
Transistor Type
HYPERFET
III
Current Limiter Range
20 to 100 amps / OFF
Throttle Profiles
(1) Modified (2) Stock
PWM Drive Frequency
(1) 7.8 kHz
(2) 1.0 kHz
Minimum Drive
(% Full Drive)
(1) 3 %
(2) 6 %
@ 25
°
C transistor
junction temp.
The Novak Dually is a microprocessor-based high-frequency
ESC (Electronic Speed Control) using advanced components
and the best HYPERFET
III
transistors for high performance.
The Dually
Dual-Profile
ESC gives you extra flexibility with
two user-selectable throttle profiles for optimum control
of both modified and stock motors with a single speed
control. The Dually also has Novak’s
CLC
III
current limiter
that delivers extra smooth control, and is adjustable from
20 to 120 amps or completely off for full power.
With Novak’s exclusive
Polar Drive Technology™
, and
Digital
Anti-Glitch Circuitry™
, the Dually runs faster, longer, and
smoother than other speed controls.
Set-up is quick and easy with Novak’s original
One-Touch
Set-Up™
, and
Radio Priority Circuity™
maintains complete
control of the vehicle’s steering servo even after the battery
pack has dumped and can no longer run the motor. The
Dually’s
heavy-duty BEC
(Battery Eliminator Circuit) handles
today’s high power servos.
Other features include the Novak
Input Plug System™
for
compatibility with all major radio systems,
Thermal Over-
load Protection,
and purple anodized Micro Fin™ heat sinks
for optimum cooling and performance.
ACCESSORIES
MOTOR CAPACITORS
To prevent radio interference problems, you must have
three 0.1
µ
F capacitors properly installed on every motor.
Included with the Dually speed controls are three 0.1
µ
F
(50v) capacitors for one motor. Additional 0.1
µ
F (50V)
capacitors are also available in Novak kit #5620.
Refer to Step 3 for motor capacitor installation instructions.
SCHOTTKY DIODES
The Dually has an internal Schottky diode, and does not
require an external Schottky diode. However, an optional
external Schottky diode can also be added for increased
performance. Refer to Step 3 for installation instructions.
Additional Schottky diodes are available in Novak kit #5640.
HEAT SINKS
The added cooling that is provided by heat sinks will
result in increased efficiency and optimum speed control
operation. A replacement Heat Sink Set for the Dually is
available as Novak kit #5403. Heat sinks are required with
the Dually, and all applications should allow adequate air
circulation through the heat sink’s fins to provide proper
speed control cooling.
PRECAUTIONS
• READ INSTRUCTIONS CAREFULLY BEFORE USING!
• WATER & ELECTRONICS DON’T MIX!
Do not operate
model in or around water. Never allow water, moisture,
or other foreign materials to get inside the ESC.
• 4 to 7 CELLS ONLY
Never use more than 7 cells (8.4
volts DC) in the main battery pack.
• MOTOR CAPACITORS REQUIRED
Three 0.1
µ
F (50V)
ceramic capacitors must be properly installed on every
motor to prevent radio interference.
• NO REVERSE VOLTAGE!
Reverse battery polarity can
damage speed control––Disconnect battery immediately.
• DON’T LET TRANSISTOR TABS TOUCH
Never allow
the two transistor tab banks to touch each other or any
exposed metal, as this will create a short circuit and
damage the speed control.
• DISCONNECT THE BATTERIES
Always disconnect the
battery pack from the speed control when not in use.
• TRANSMITTER ON FIRST
Always turn on the power of
your transmitter first so that you will have control of the
radio equipment when you turn on the speed control.
• DON’T GET BURNT!
Transistor tabs can get hot, so be
careful not to touch them until they cool. If transistor
tabs get extremely hot use optional heat sinks.
• INSULATE WIRES
Always insulate exposed wiring with
heat shrink tubing to prevent short circuits.
RADIO INTERFERENCE
The high frequency switching operation of electronic
speed controls can generate radio interference. Here are
some common causes of radio interference problems:
• CAPACITORS NOT INSTALLED ON MOTOR
Electric motors generate radio noise that can interfere
with the operation of the receiver. To prevent radio
problems, every motor must have three 0.1
µ
F (50V)
ceramic capacitors installed on it.
Refer to Step 3 for proper motor capacitor installation.
• RECEIVER/ANTENNA INCORRECTLY MOUNTED
The receiver and antenna should be mounted as far
from the motor, power wires, battery, and servo as
possible, as these components all emit radio noise. On
graphite or aluminum, place the receiver on edge with
the crystal and the antenna as far above the chassis as
possible. Mount the antenna close to receiver and trail
any excess wire off the top of antenna.
Do not cut or coil excess wire!
• MOTOR BRUSHES WORN
As motor brushes continue to wear, excessive motor
noise will be generated. To avoid radio interference,
worn motor brushes should be replaced. The motor
commutator may also need to be cleaned or trued and
can be machined to help the motor run more efficiently.
Included with the Dually ESC is the Novak Input Plug
System
TM
to convert the Futaba J style signal harness to
be compatible with Sanwa, KO, Kyosho, JR, and Hitec
radios. Refer to Figures 1 through 3 to convert plug.
Sanwa (A) KO Kyosho (KYO) JR/Hitec/AirZ
FIGURE 1
With a small standard screwdriver, press on
each of the three metal prongs until the wires are easy to
remove. Remove wires.
FIGURE 2
With the screwdriver, carefully lift each of the
metal locking tabs to the angle shown.
STEP 1
CHANGING THE INPUT PLUG
Part #1660
FIGURE 3
Insert each pin into the correct plug slot. Each
pin should "click" into place.
(Sanwa plug shown)
WHT
= White wire terminal (signal)
BLK
= Black wire terminal (negative)
RED
= Red wire terminal (positive)
CAUTION
Improper installation of these wires may cause
damage to the receiver, servo, and speed control.
The locking tab must not extend
outside the plastic plug housing.
1. DETERMINE THE BEST ESC MOUNTING LOCATION
The speed control should be positioned away from the
receiver and antenna as shown in set-up photo on back
page. Choose a mounting position that will keep power
wires away from the receiver and antenna. Choose a
position that will provide maximum airflow through the
transistor tabs or heat sinks to allow for proper cooling.
2. INSTALL THE SPEED CONTROL
Use the included double-sided tape to mount ESC.
3. INSTALL THE ON/OFF SWITCH
Determine a convenient place to mount the switch
where it will be easy to get to. Mount switch using a
piece of double-sided tape or with a screw through the
hole in the base of the switch housing.
4. INSTALL THE RECEIVER AND ANTENNA
Mount receiver as far from ESC, motor, power wires,
battery, and servo as possible. These components all
emit radio noise when the throttle is being applied. On
graphite or aluminum, it may help to place the receiver
on edge with the crystal and antenna as far above the
chassis as possible. Mount the antenna close to the receiver
and trail any excess wire off the top of the antenna mast.
Cutting or coiling excess wire will reduce radio range.
STEP 2
MOUNTING INSTRUCTIONS
STEP 3
HOOK-UP INSTRUCTIONS
STEP 3
HOOK-UP INSTRUCTIONS
(Cont.)
Refer to Set-Up photo on back
2. CONNECT SPEED CONTROL TO THE RECEIVER
After the proper input plug plastic has been installed
to match the receiver (Refer to Step 1), plug the speed
control into the
THROTTLE CHANNEL
of the receiver.
3. CONNECT SPEED CONTROL TO THE BATTERY PACK
Cut the
BLACK
wire of speed control to the desired
length and strip about 1/8”-1/4” of insulation off the
end. Solder to the
negative
side of a completely
charged 4 to 7 cell battery pack (1.2 volts DC/cell).
Strip a short section of the insulation (1/4”-3/8”) from
the middle section of the speed control’s
RED
wire
where it will attach to
positive
of the battery pack.
Solder the stripped middle section of the
RED
wire to
positive
of the battery pack.
4. CONNECT SPEED CONTROL TO THE MOTOR
Cut the
RED
wire (after battery pack connection) to the
desired length and strip about 1/8”-1/4” of insulation off
the end. Solder to the
positive
motor tab.
Cut the
BLUE
wire of speed control to desired length
and strip about 1/8”-1/4” of insulation off the end.
Solder to the
negative
tab of the motor.
TIP:
Twisting the BLUE & RED motor wires one or two times
around each other as they go to motor can help reduce any
radio noise that may be emitted from the power wires.
5. USE OF OPTIONAL EXTERNAL SCHOTTKY DIODE
Solder the lead
CLOSEST
to the silver stripe on the body
of the Schottky diode to the
POSITIVE
(+) motor tab.
Solder the lead
OPPOSITE
the silver stripe on the body
of the Schottky to the
NEGATIVE
(–) motor tab.
If installed backwards, a Schottky diode will be destroyed. The
body of a bad diode will normally crack open. Replace only with
Schottky diodes that have a minimum rating of 35 volts / 8 amps.
Schottky diodes are available in Novak kit #5640.
6. USING PLUGS FOR BATTERY & MOTOR CONNECTION
High-quality/low-resistance connector plugs, such as
Dean’s Ultra Plugs, can also be used to connect the
motor and battery pack. While connectors make com-
ponent changes quick and easy, they will never have
the low resistance of a good solder joint.
Use connectors that can not be connected backwards.
It is always good practice to use the female connectors
on the battery packs to avoid short circuiting of the
connector and the battery pack.
If you use connectors for both the battery and the
motor, use a male connector on the speed control
wires going to the battery and a female connector on
the wires going to the motor. By doing this, you will
avoid plugging the battery pack into the speed
control’s motor output by mistake.
1. INSTALL MOTOR CAPACITORS
Electric motors generate radio noise that can interfere with
your receiver and cause radio problems. Included in the
accessory kit with the ESC are three 0.1
µ
F (50V) non-
polarized, ceramic capacitors. These capacitors must be
installed on every motor to help reduce noise generated
by the motor and also to prevent possible ESC damage.
Solder 0.1
µ
F (50V) capacitors between:
• POSITIVE (+) motor tab & NEGATIVE (–) motor tab.
• POSITIVE (+) motor tab & GROUND tab*.
• NEGATIVE (–) motor tab & GROUND tab*.
*If motor has no ground tab, solder the capacitors to motor can.
Negative (–) motor tab
0.1
µ
F Capacitors
Schottky diode
Positive (+) motor tab
Ground / motor can
Extra 0.1
µ
F capacitors are available in Novak kit #5620.