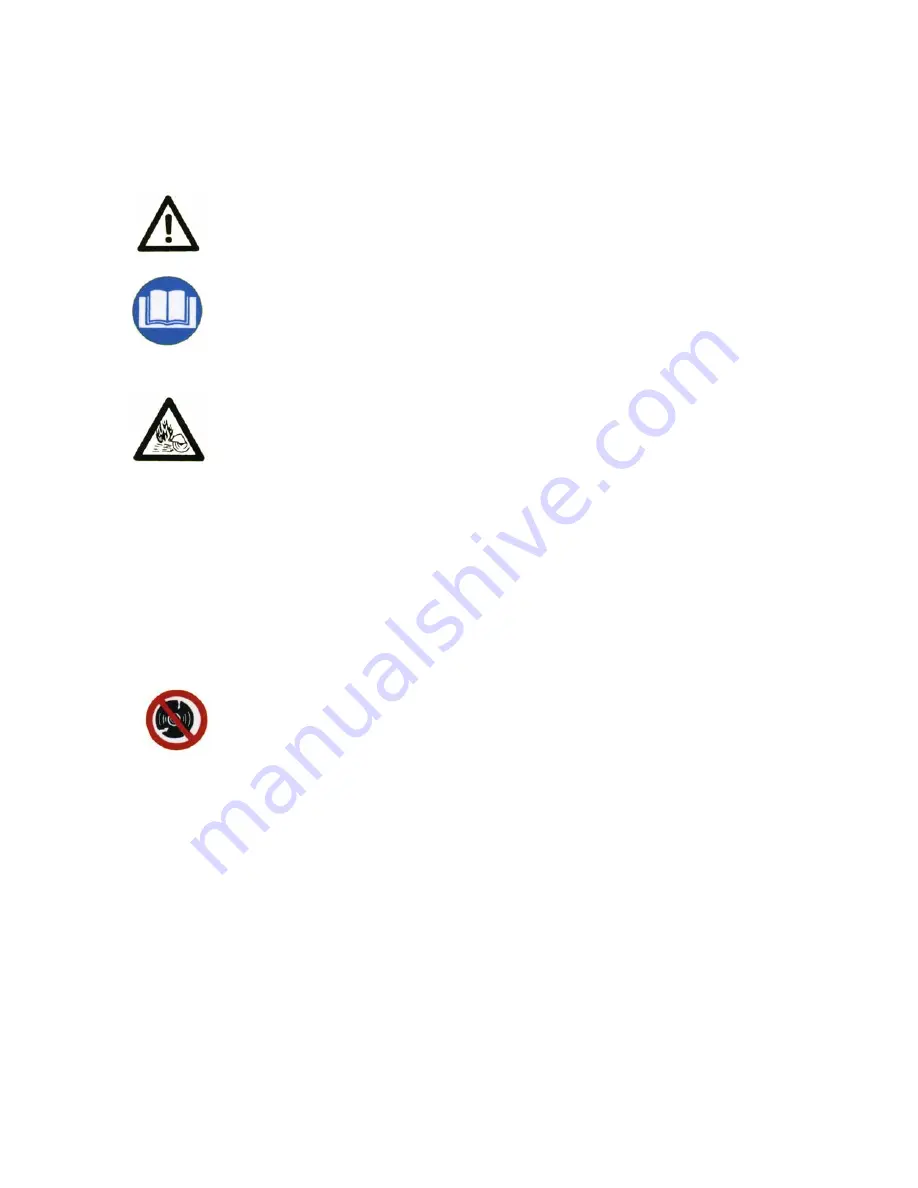
20. Blade Guard Adjusting Lever
Allows adjustment of blade guard to direct dust away from operator.
SAFETY PRECAUTIONS:
As the cutoff saw is a high speed power tool, improper use of this saw might be
hazardous. To avoid property damage or personal injury, it is
EXTREMELY
IMPORTANT
to read, fully understand and observe the following safety
precautions before operating this cutoff saw.
1. Worksite Requirements:
The worksite should be free of any materials or objects that are flammable or
explosive.
Surroundings should be in order, without clutter, have sufficient visibility and be
well ventilated. The flooring the operator stands on should be nonskid. Take extreme care when
working in wet and freezing weather (rain, snow, frost, ice).
Bystanders should keep away from the saw when it is operating. Children, the handicapped and
animals should never be allowed in the work area.
Loose objects may be thrown toward the operator by the cutting tool; position the object to be cut
securely to ensure it can’t be moved by the blade when cutting.
2. Blade:
Before installing a blade, make sure that the maximum operating speed of the blade
is above or equal to the spindle speed of your cutoff saw. Inspect the cutting blade
frequently and replace immediately if the cutting blade is cracked or warped.
Cracked or warped blades may shatter or break and cause serious personal injury.
Failure to follow these directions may cause the blade to shatter or crack in use,
causing serious or fatal injury.
Never use carbide-tipped, woodcutting or circular machine blades. They can cause severe
personal injury from reactive forces, blade contact or thrown objects.
Use of the wrong cutting blade for which it was not designed may cause that blade to shatter,
causing serious or fatal injury. Only use the cutting blade approved for the type of material to be
cut.
Diamond blades have a much better cutting performance than standard abrasive blades. The
blades are steel centered and diamond particles are imbedded in their cutting edges.
Wet or dry cutting is possible. Cutting wet will extend the life of your diamond blades. A water
attachment comes as standard equipment with this cutoff saw. Before using the water attachment,
make sure that the screw that secures the outlet tube is tightened.
5