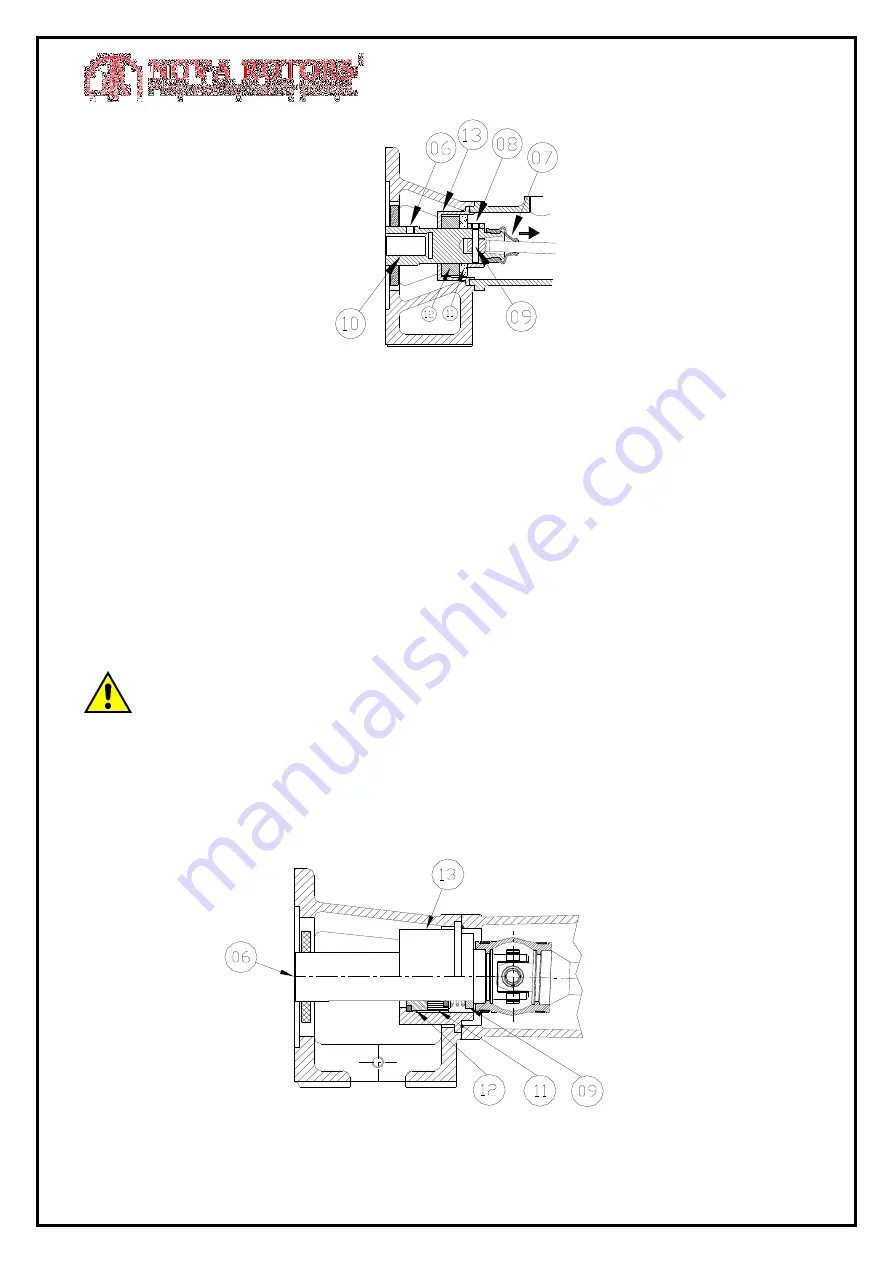
Pag.29 (Funct. and Maint.Manual n.03 – Fourth edition) OMI.EN-PCP001 R01
9.4.2.1.2. RE-ASSEMBLY
1. Check the condition of O’Rings, seal and stationary seat faces.
2. Check the condition of the hollow shaft.
3. Clean the hollow shaft, the housing (13) (see picture above) and all involved parts.
4. Clean and oil the propeller shaft (Rust jams the shafts coupling, thus increasing the
danger of damage during disassembly).
5. Wet with glycerine the hollow shaft (10) and the bush (08) on the involved area to
ease the insertion of the mechanic seal.
6. Carefully clean the seal faces before assembly.
7. Perform the steps backwards described in Chap. 9.4.2.1.1.
DANGER: During re-assembly, it is necessary to distribute the pressure uniformly
on the fixed ring, to prevent malfunctioning or failures.
9.4.2.2 Single mechanical seal (TEN4) for 030, 040, T062-1 pumps type