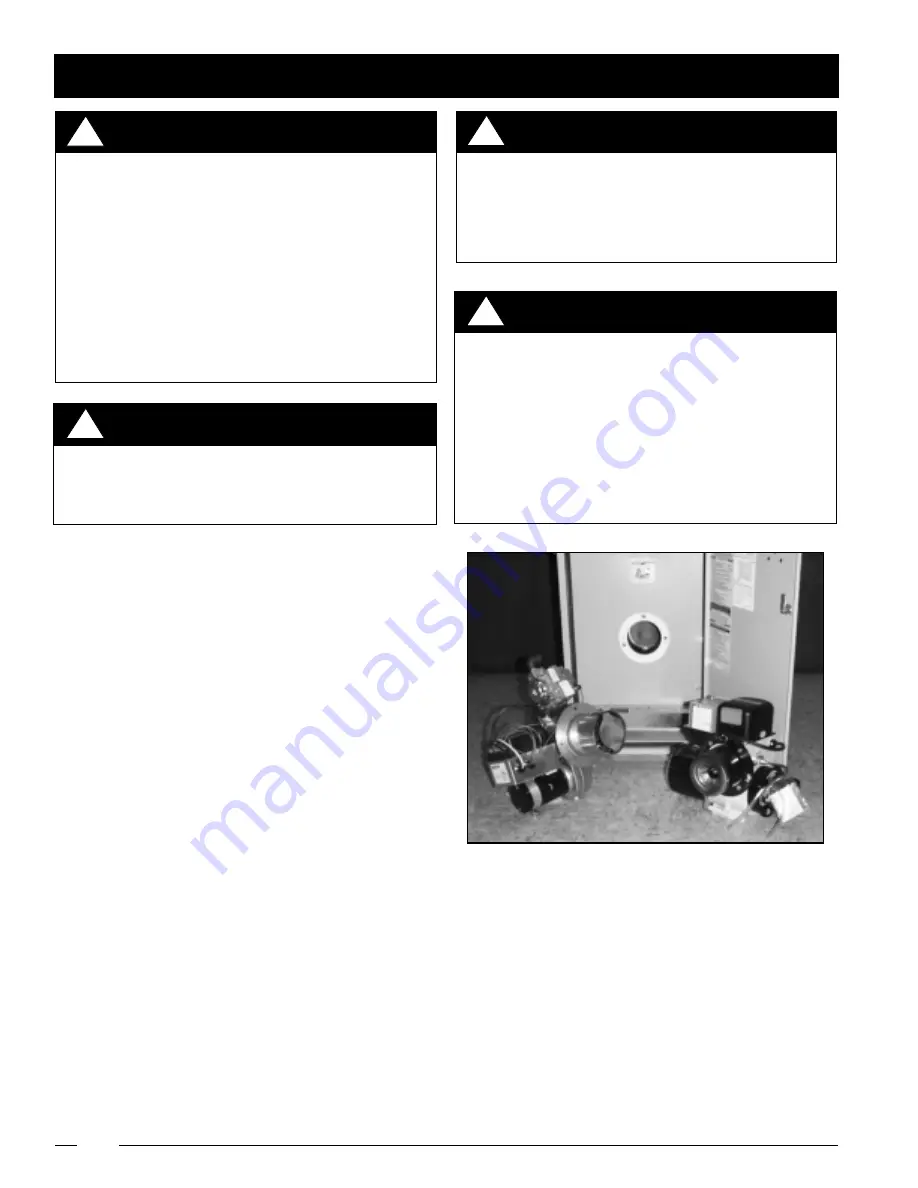
18
CMF Oil to Gas Conversion
WARNING:
!
This furnace must be installed by a qualified
installing agency and in accordance with local
codes and ordinances. Failure to properly install
the furnace, base assembly and venting system
as described herein may damage the equipment
and/or the home, can create a fire or asphyxiation
hazard, violates U.S. listing requirements, and
will void the warranty. This furnace is NOT
approved for installation with split system air
conditioning. Use a NORDYNE packaged air
conditioning system.
FOR YOUR SAFETY:
!
Do not store gasoline or other flammable vapors
and liquids in the vicinity of this or any other
appliance.
WARNING:
!
Improper installation, alteration, service or
maintenance can cause injury or property
damage. Refer to this manual. For assistance or
additional information consult a qualified
installer, service agency, or the gas supplier.
Figure 1.
Before installing the power gas burner, removal of present
burner is required. (See Figure 2.)
1. Shut off electric power supply to furnace. Remove
power cord from 120v receptacle, remove low voltage
(thermostat) wiring from primary control connections.
2. Shut off fuel supply to burner, close line or tank valve if
applicable. Disconnect fuel line at inlet fitting on burner
pump and remove fuel line.
3. Loosen and remove the three (3) 2/16" hex nuts, and
remove the burner.
4. Inspect the combustion chamber and heat exchanger
for cracks, corrosion, or soot. If signs of sooting are
present, the heat exchanger should be cleaned to insure
proper draft.
Installing Gas Burner
1. Place new burner gasket on mounting plate. (See Figure
3.) Insert burner tube into heat exchanger through
mounting flange. Mount burner on studs, making sure
burner will pull up tight to flange, and fasten to mounting
flange using the three hex nuts.
2. Reconnect thermostat leads to appropriate connections
on burner. Attached power cord may then be plugged
into 120v receptacle.
3. Connect gas piping and check for leaks.
a. Gas piping should be sized and installed in accordance
with local codes and utility regulations.
4. Thermostat - It may be necessary to change the heat
anticipator setting. Failure to do so could result in a wide
temperature fluctuation in home.
FOR YOUR SAFETY:
!
WHAT TO DO IF YOU SMELL GAS
Do not try to light any electrical switch; do
not use any phone in your building.
Immediately call your gas supplier from a
neighbor's phone. Follow gas supplier's
instructions.
If you cannot reach your gas supplier, call
the fire department.