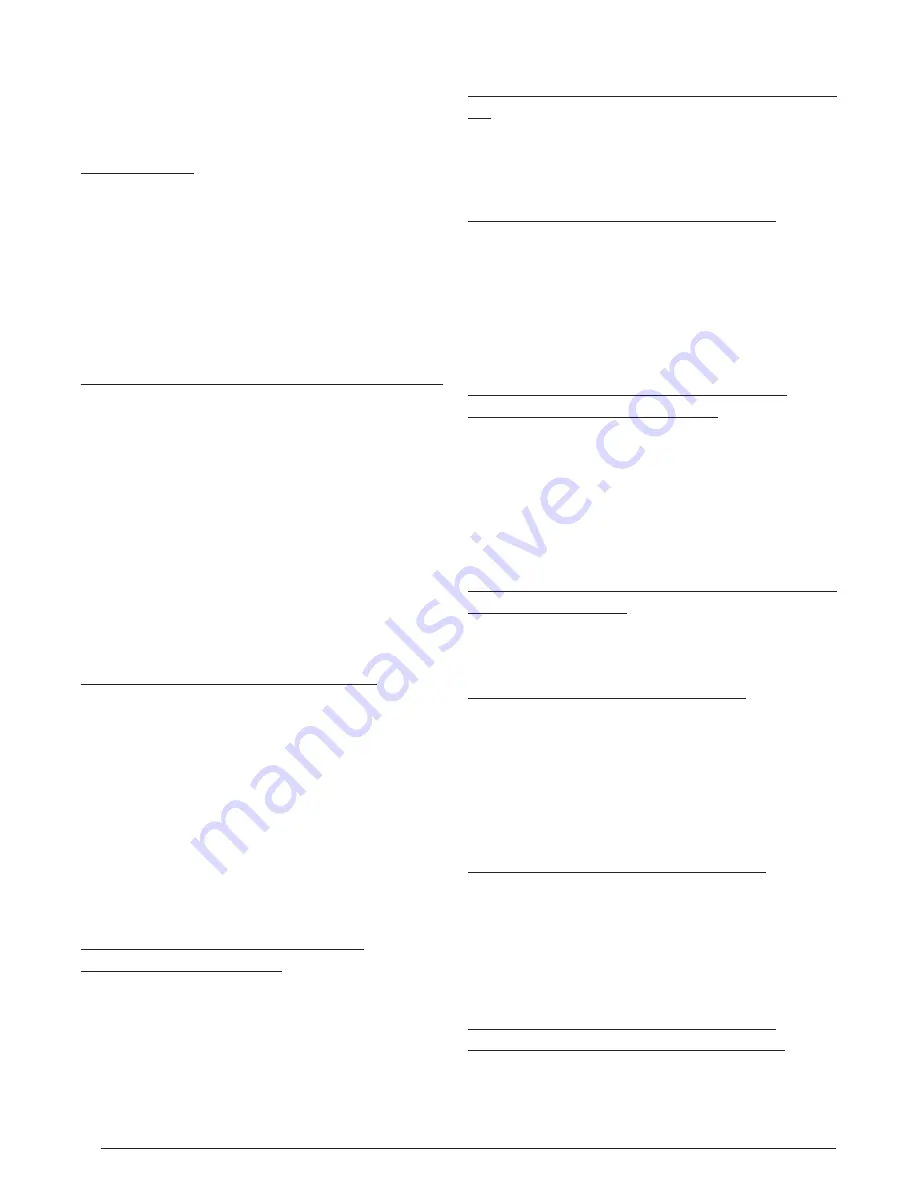
26
TROUBLESHOOTING
Direct Ignition Furnaces (M1M Models) &
Gas Gun Furnaces (M1B Models)
High Gas Bills
a. Verify the proper orifi ce is being used.
b. Check the return air system. Is it clear and free of
blockage?
c. Check the furnace fi lter. Is it clean or need replacing?
d. Verify the home is insulated, windows and doors fi t
tightly, and there are no leaks in the heating duct system.
e. Check the room thermostat. Is the setting higher than
necessary? Low humidity requires higher temperatures
for the same level of comfort. Check for proper humidity
level in the home.
Burner Motor won’t Run - T-stat Calls for Heat
1. Check the electrical supply to the furnace.
2. Verify the furnace furnace On-Off switch is in the ON
position.
3. Defective thermostat circuit - white and red thermostat
low voltage leads (M1/M5M, M1/M5B models). If the
burner motor or combustion fan runs, check:
• Thermostat connections
• Thermostat
4. No voltage to control module - determine if 24 volts (or
120 volts) is available to the control module. If voltage
is not available check for:
• Blown fuse, defective transformer, circuit breaker,
no electrical supply.
• Limit switch open.
• Loose connections.
Combustion Blower Runs - No Flame
1. Defective centrifugal switch (M1B Model).
• Check the operation of centrifugal switch by removing
end bell of the burner motor.
• Clean contacts of motor.
• If the contacts are closed, replace the motor.
2. Defective pressure switch (M1M - 077 & 090 Models)
- check air tube and electrical connections.
3. Burner in purge mode - allow 75 seconds for fl ame
establishing period.
4. Check for proper electrical connections at purge timer,
control box, or gas valve.
5. Check for gas supply - gas line valve on, control lever
on.
120 VAC Is Available At AMP Plug -
Ignitor Does Not Heat Up
1. Disconnect power to the furnace.
2. Disconnect AMP plug to the ignitor, and check ignitor
resistance with an ohm meter. Set on RX1 scale.
• Normal reading should be 40 - 75 ohms.
• If above or below this rating at room temperature
change ignitor.
3. Check for continuity from ignitor receptacle to burner.
Control Module is Powered - Ignitor won’t Heat
Up
1. Disconnect ignitor leads at AMP receptacle and check
for 120 volts at the plug during ignition sequence.
2. Replace ignition control if 120 volts is not available at
AMP plug during ignition sequence.
Main Flame Ignites - Burner Locks Out
• Ignition control is not properly grounded.
• Defective ignition control.
• Improper polarity of 120 volt power supply.
• Ignitor has hairline crack.
• Improper gas pressure or burner air adjustment is not
allowing fl ame to contact ignitor tip for fl ame rectifi cation.
• Misaligned ignitor does not allow fl ame to contact ignitor
tip for fl ame rectifi cation.
Burner Short Cycling - Thermostat Calls
for Heat, Limit Switches Closed
• Check for polarity.
• Check ground.
• Check fl ue.
• Check combustion air.
• Check gas pressure.
• Check orifi ce.
• Check the position of ignitor, a normal reading should
be 40-75 ohms.
24 Volts Supplied To Gas Valve During Ignition
- No Main Gas Flow
• Gas valve may be defective. Replace if necessary.
• Gas piping may be plugged. Check for adequate gas
supply to gas valve at union.
Burner Operates - Insuffi cient Heat
• Check thermostat for proper setting and location.
Thermostat should not be located where it will be affected
by another heat source.
• Check for clean fi lter and proper air fl ow.
• Check burner for proper gas fi ring rate.
• Be sure unit is not undersized for its thermal load.
• Check thermostat anticipator. The nominal setting is
0.4.
Burner Flame Without Motor Running
• Gas valve stuck open, check gas valve for proper
operation (replace if necessary) and inspect heat
exchanger.
• Check for 115 volts to the combustion blower motor;
replace if necessary.
• If no power to combustion blower then check wiring and
control module; replace if necessary.
Circulation Air Blower Will Not Operate
Even Though The Burner Does Operate
• Check thermostat
G
connection.
• Check wiring to motor.
• Check for a defective motor.
Summary of Contents for M1B 066
Page 35: ...35...