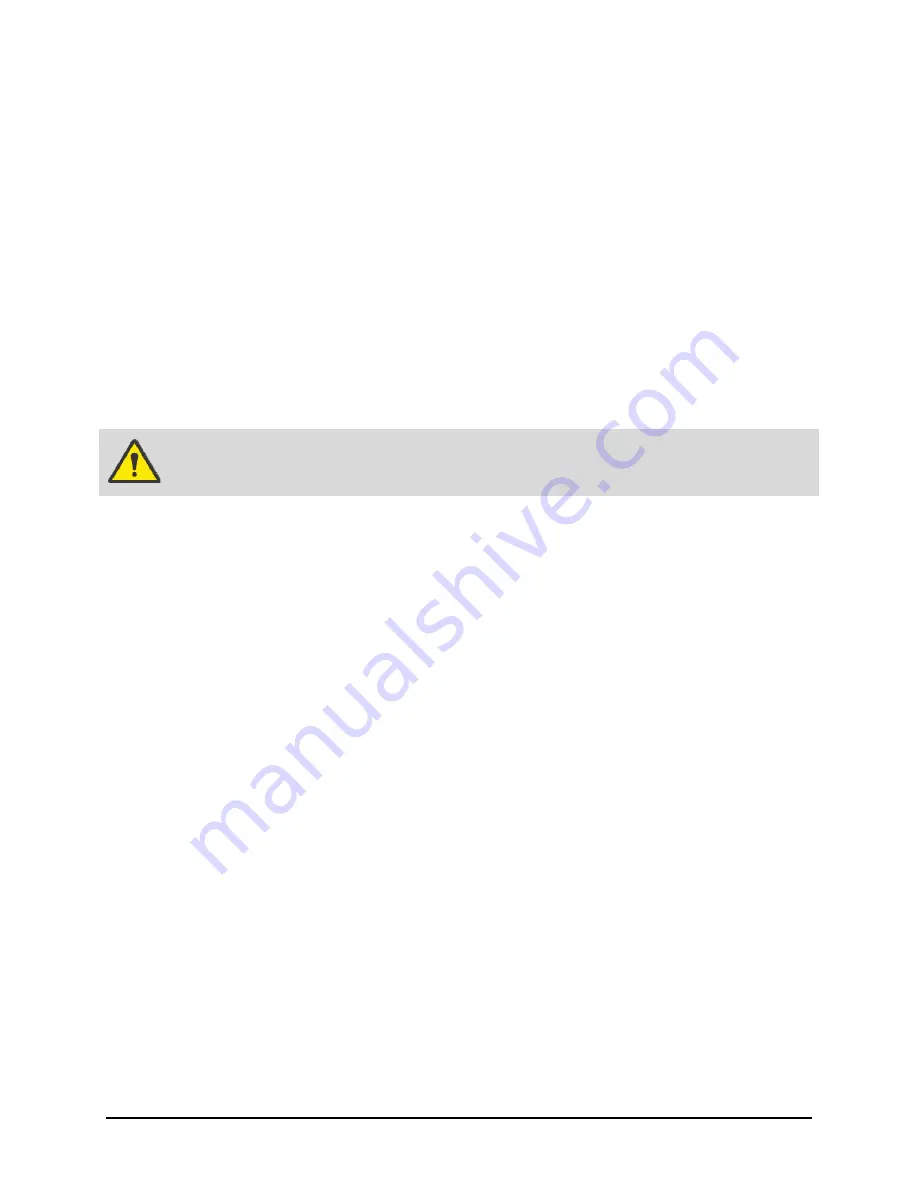
8-4
Parts Replacement
8.10 Replacing the Conveyor Belts
Checking the condition of the conveyor belts should be part of the routine maintenance schedule for the
dispensing system. Cracked, worn, or broken belts should be replaced immediately.
To maintain reliable system performance, it is recommended that the conveyor belts be changed every six
months. However, the belts may need to be changed more frequently or less frequently, depending upon
the volume of workpiece production.
Tools and Materials Needed
•
4 mm Hex Key
•
Soft Cloth and Cotton Swabs
•
2.5 mm Hex Key
•
Replacement Conveyor Belts
•
Isopropyl Alcohol
•
Removable Thread Locker (P/N 40-0019)
•
Phillips Head Screwdriver
•
Torque Wrench
To remove a conveyor belt:
WARNING!
This procedure should only be performed by a trained service technician.
NOTES
Only one belt should be removed at a time. Use the other belt as a reference for proper
orientation of the belt being replaced.
All components and fasteners removed during this procedure should be retained in an
orderly manner and in a safe location for reinstallation or shipment back to Nordson
ASYMTEK.
1.
Move the dispensing head to the home position.
2.
Use the Fluidmove Jog Controls to move the rear conveyor rail to the extreme back of the
dispensing chamber.
3.
Perform a service shutdown as specified in
4.
Open the hatch.
5.
Remove any rail-mounted components that interfere with belt removal/replacement.
If stop pins interfere, use a 2.5 mm hex key to remove the stop pins along the length of
the conveyor rails.
NOTE
For ease of reinstallation, you should note the locations and orientations of
rail-mounted components before removing them.
6.
Slide the old belt off the pulley tires and discard.
If necessary, loosen the pulley screws at each end of the conveyor and move the pulleys
to the right or left to loosen the belt.
Summary of Contents for Spectrum II S2-900 C Series
Page 2: ......
Page 36: ...1 22 Introduction 1 11 8 Rear View Open Figure 1 9A S2 900 Rear View Open 1 2 3 4...
Page 40: ......
Page 124: ......
Page 157: ...Calibration and Adjustment 5 33 Figure 5 38 Dispense Lift Table Controls...
Page 159: ...Calibration and Adjustment 5 35 Figure 5 40 Beacon Configuration Window...
Page 186: ......
Page 197: ...Troubleshooting 7 11 Figure 7 1 Scale Setup Menu Figure 7 2 Scale Error Message...
Page 200: ......
Page 215: ...Parts Replacement 8 15 Figure 8 11 Replacing a Panel Mounted Fuse...
Page 218: ......
Page 223: ...Specifications 9 5 Top View mm Back View mm Figure 9 2 S2 900 System Dimensions 2 of 2...
Page 225: ...Specifications 9 7 Top View mm Back View mm Figure 9 4 S2 9XXC System Dimensions 2 of 2...
Page 228: ...A 2 Appendix A Material Safety Information A 2 1 Multemps PS NO 2...
Page 229: ...Appendix A Material Safety Information A 3...
Page 230: ...A 4 Appendix A Material Safety Information...
Page 231: ...Appendix A Material Safety Information A 5...
Page 232: ...A 6 Appendix A Material Safety Information...
Page 233: ...Appendix A Material Safety Information A 7...
Page 235: ...Appendix A Material Safety Information A 9...
Page 236: ...A 10 Appendix A Material Safety Information...
Page 237: ...Appendix A Material Safety Information A 11...
Page 238: ...A 12 Appendix A Material Safety Information...
Page 239: ...Appendix A Material Safety Information A 13...
Page 240: ...A 14 Appendix A Material Safety Information...
Page 246: ......
Page 252: ......
Page 258: ......