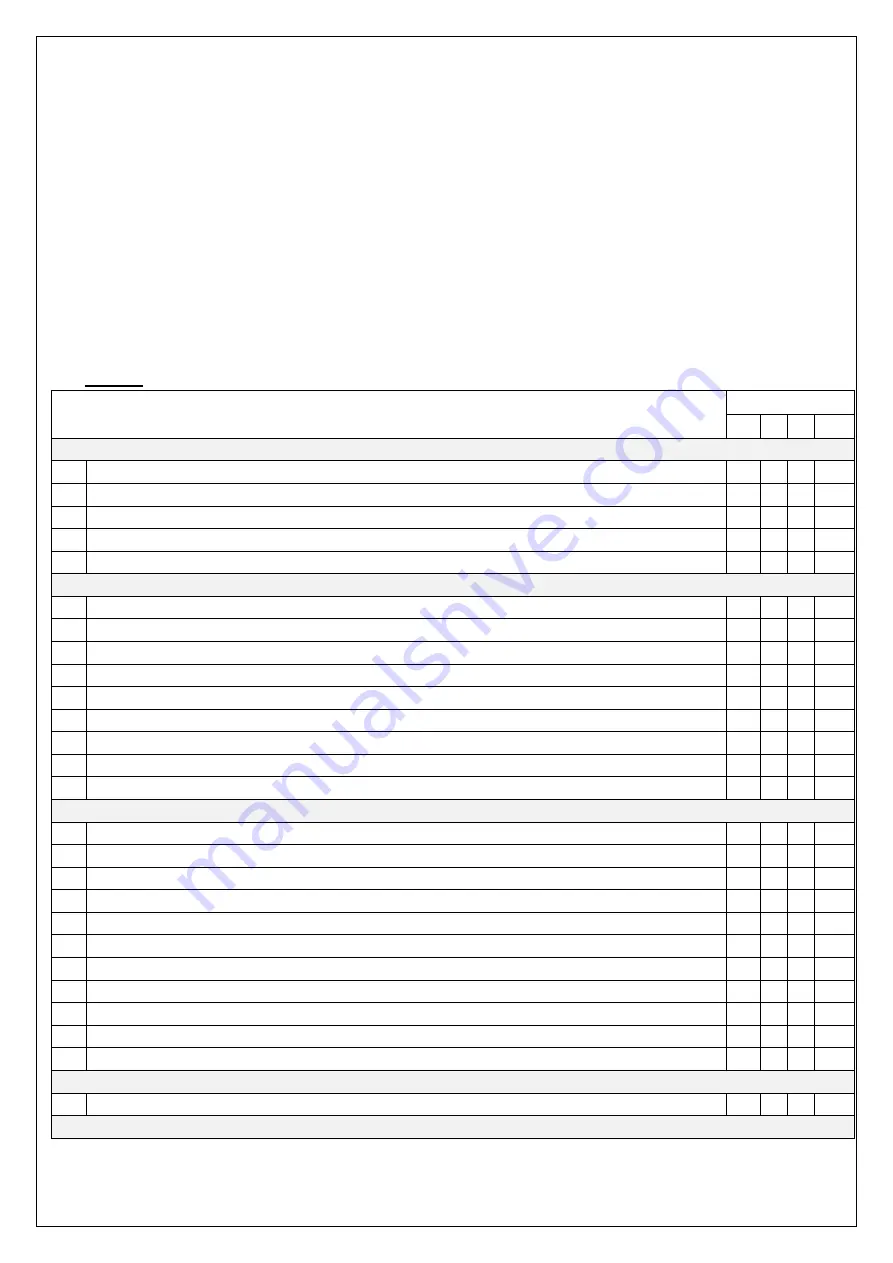
17
Please pay attention by maintain the tiller arm. The gas pressure spring is
pre-loaded by compression, carelessness can cause injury.
Use approved and from your dealer released original spare parts.
Please consider that oil leakage of hydraulic fluid can cause failures and accidents.
It is allowed to adjust the pressure valve only from trained service technicians.
If you need to change the wheels, please follow the instructions above. The castors must
be round and they should have no abnormal abrasion.
Check the items emphasized maintenance checklist.
a.
Maintenance checklist
Table 3: Maintenance checklist
Interval(Month)
1
3
6
12
Hydraulic
1
Check the hydraulic cylinder(s), piston for damage noise and leakage
2
Check the hydraulic joints and hose for damage and leakage
3
Inspect the hydraulic oil level, refill if necessary
4
Refill the hydraulic oil ( 12 month or 1500 working hours )
5
Check and adjust function of the pressure valve (0/+10%)
Mechanical system
6
Inspect the forks for deformation and cracks
7
Check the chassis for deformation and cracks
8
Check if all screws are fixed
9
Check the push rods for deformation and damages
10 Check the gearbox for noise and leakage
11 Inspect the wheels for deformation and damages
12 Inspect and lubricate the steering bearing
13 Inspect and lubricate the pivot points
14 Lubricate the grease nipples
Electrical system
15 Inspect the electric wiring for damage
16 Check the electric connections and terminals
17 Test the Emergency switch function
18 Check the electric drive motor for noise and damages
19 Test the display
20 Check, if correct fuses are used
21 Test the warning signal
22 Check the contactor(s)
23 Check the frame leakage (insulation test)
24 Check function and mechanical wear of the accelerator
25 Check the electrical system of the drive motor
Braking system
26 Check brake performance, if necessary replace the brake disc or adjust the air gap
Battery