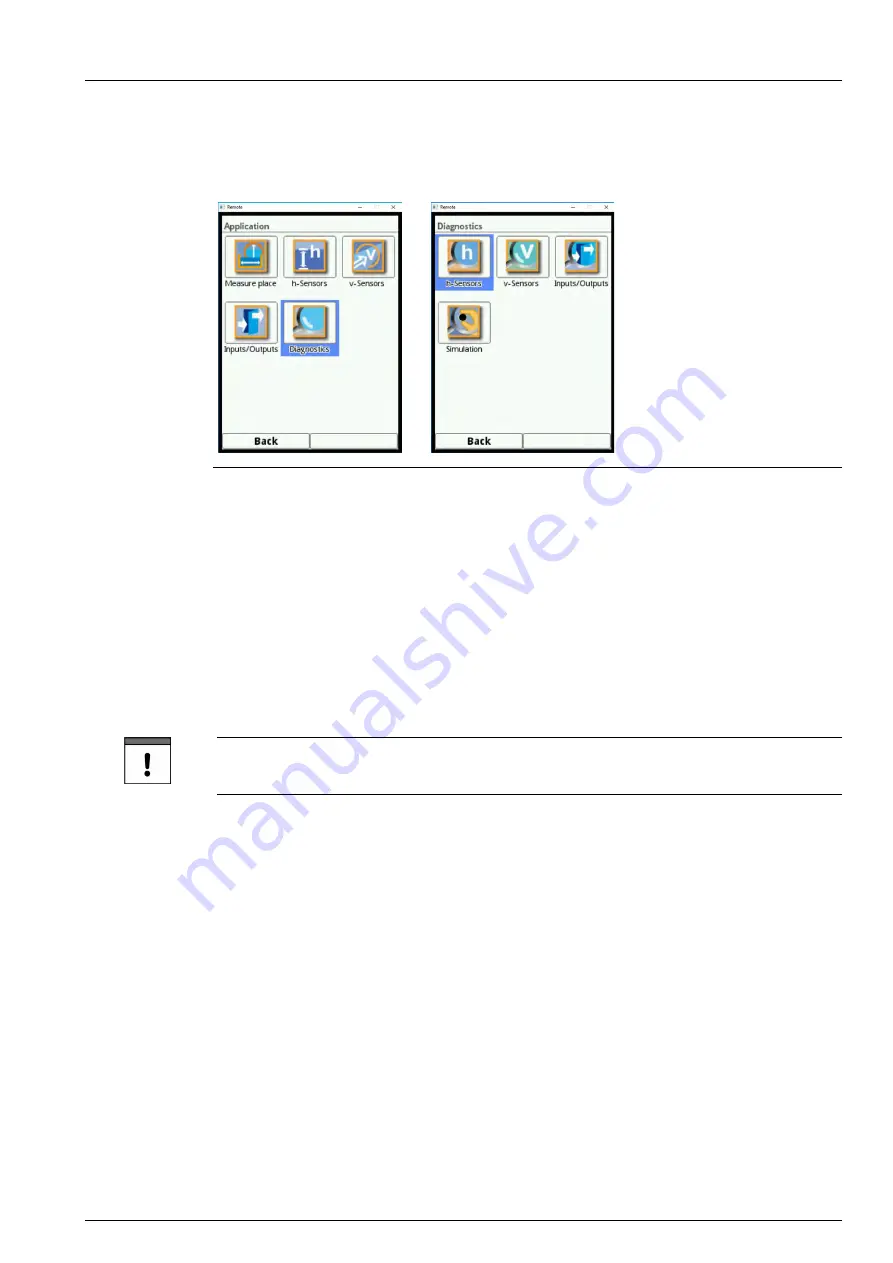
Diagnosis
page 109
rev. 00 / 12.04.2017
Diagnosis
30 Basics of Diagnosis Menus
Fig. 30-1
Diagnosis menu
The >Diagnosis< menu can be found in menu >Application< and is divided into four sub-
menus.
The Diagnosis menu and all submenus are pure read-only and simulation menus.
In this section the following settings can be verified or simulated:
• h-Sensors (level and adjustment height)
• v-Sensors (article no., firmware version, serial no. and velocity)
• Inputs and outputs (status and simulation)
• Simulation
Important Note
Always follow the safety information on simulation on page 117.