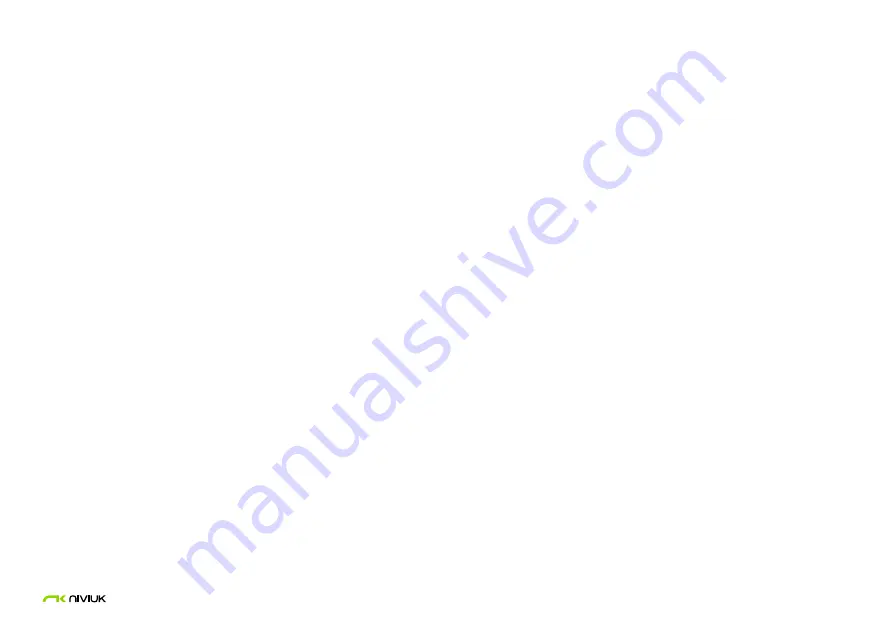
6
3D Pattern Cut Optimisation (3DP)
– the latest generation of wings
require a new fabric panel pattern and cutting system. Creating separate
panels for each of the sections at the front of the wing means the sail
fabric is more taut and crease-free. During the cutting, the optimal
orientation of the fabric section is selected, depending on its final
location. If the fabric pattern is properly aligned with the axes of load, it
suffers less deformation after repeated use, to the long-term benefit of
the leading edge.
3D Leading Edge (3DL)
- adding an extra seam to the longitudinal
axis of the glider helps, on the one hand, give more consistency and
volume to the profile (a more efficient 3D contour) and on the other, joins
and shapes the leading edge panels. The fabric is guided by the panel
position to ensure fewer creases and better load distribution. The result
is a cleaner profile, which benefits the wing in terms of performance and
durability.
The use of these technologies is a big technological leap forward in
building wings and a big improvement in flight comfort.
For the construction process of the LINK 2 we use the same criteria,
quality controls and manufacturing processes as in the rest of our range.
From Olivier Nef’s computer to fabric cutting, the operation does not
allow for even a millimetre of error. The cutting of each wing component
is performed by a rigorous, extremely meticulous, automated computer
laser-cutting robotic arm.
This program also paints the guideline markers and numbers on each
individual fabric piece, thus avoiding errors during this delicate process.
The jigsaw puzzle assembly is made easier using this method and
optimises the operation while making the quality control more efficient.
All Niviuk gliders go through an extremely thorough and detailed final
inspection. The canopy is cut and assembled under strict quality control
conditions facilitated by the automation of this process.
Every wing is individually checked with a final visual inspection.
The line diameter has been calculated depending on the workload and
aims to achieve the required best performance with the least drag. The
sheath protects the line cores from UV rays and abrasions.
The lines are semi-automatically cut to length and all the sewing is
completed under the supervision of our specialists.
Every line is checked and measured once the final assembly is
concluded.
Each glider is packed following specific maintenance instructions as
recommended by the fabric manufacturer.
Niviuk gliders are made of premium materials that meet the requirements
of performance, durability and certification that the current market
demands.
Information about the various materials used to manufacture the wing
can be viewed in the final pages of this manual.
1.5 ELEMENTS AND COMPONENTS
The LINK 2 is delivered with a series of accessories that will greatly assist
you in the maintenance of your paraglider:
- A Kargo bag. This bag is large enough to hold all equipment
comfortably and with plenty of space.
- An inner bag to protect the wing during storage and transport.
- An adjustable compression strap to compress the inner bag and reduce
its volume.
- A repair kit with self-adhesive Ripstop tape in the same colour as the
wing and spare O-rings to protect the maillons.
Summary of Contents for LINK 2
Page 1: ...LINK 2 User s manual ...
Page 21: ...24 10 3 RISERS PLAN ...
Page 22: ...25 10 4 SUSPENSION PLAN ...
Page 25: ...28 LINK 2 21 LINK 2 23 10 9 CERTIFICATION ...
Page 26: ...29 LINK 2 25 LINK 2 27 ...
Page 27: ......